진공 열성형은 플라스틱 시트를 가열하고 진공 압력을 사용하여 단일 금형 주위에 성형하여 플라스틱 재료를 특정 형태로 성형하는 데 사용되는 제조 공정입니다.이 공정은 플라스틱을 유연해질 때까지 가열하고 금형 위에 배치한 다음 진공 흡입을 적용하여 재료를 금형의 윤곽에 단단히 끌어당기는 과정을 거칩니다.재료가 식으면 금형의 모양이 유지되어 고품질의 유연한 제품이 만들어집니다.이 방법은 비용 효율성과 다용도로 인해 맞춤형 디자인 및 프로토타입 제작에 널리 사용됩니다.
핵심 사항을 설명합니다:
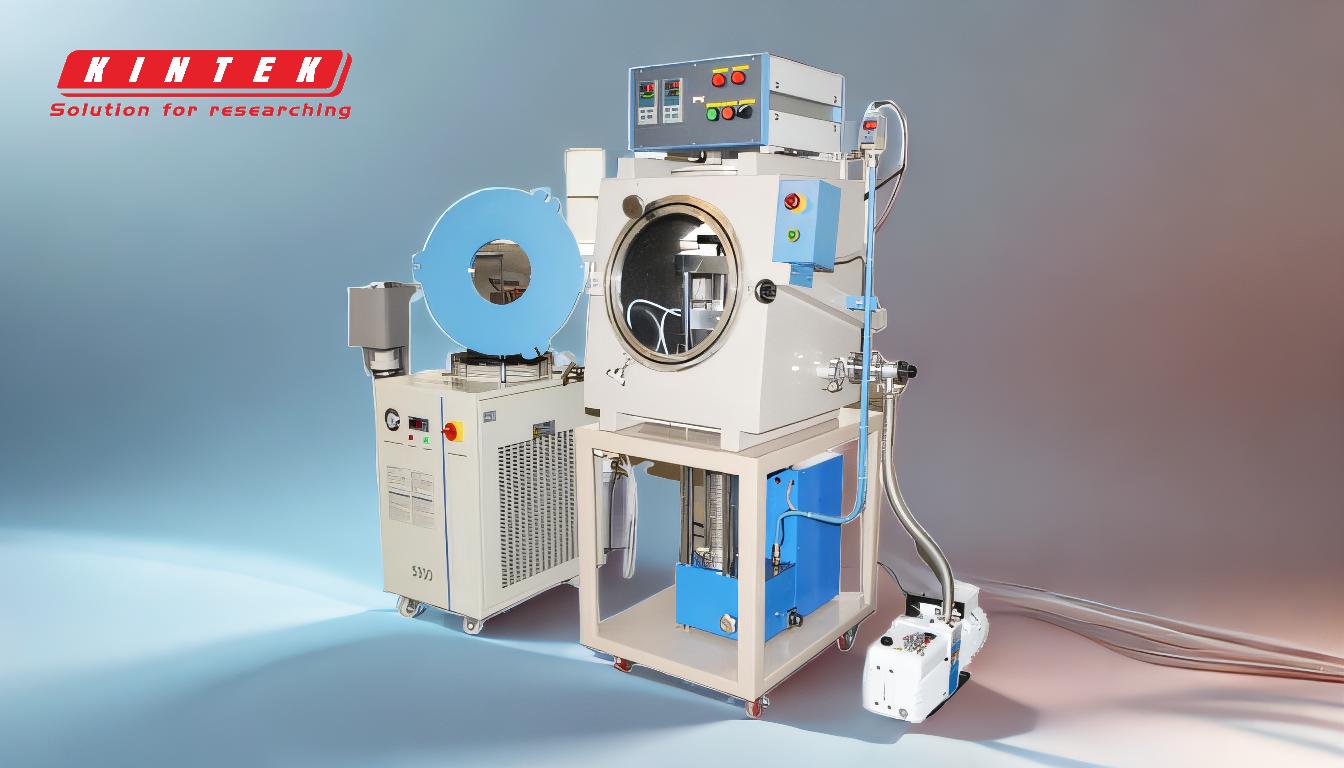
-
재료 준비:
- 두께, 유연성, 내구성 등 최종 제품의 원하는 특성에 따라 열가소성 소재의 평평한 시트가 선택됩니다.
- 시트는 프레임에 고정되어 가열 및 성형 단계에서 제자리에 단단히 고정됩니다.
-
플라스틱 시트 가열하기:
- 플라스틱 시트는 최적의 성형 온도에 도달할 때까지 복사열 히터를 사용하여 균일하게 가열됩니다.이 온도는 사용되는 플라스틱의 종류에 따라 다릅니다.
- 가열하면 플라스틱이 유연해지고 갈라지거나 찢어지지 않고 모양을 만들기 쉬워집니다.
-
금형 위에 배치하기:
- 가열되면 플라스틱 시트가 몰드 바로 위에 배치됩니다.몰드는 일반적으로 목재, 알루미늄 또는 복합 재료로 만들어지며 원하는 최종 모양과 일치하도록 설계됩니다.
- 올바른 정렬을 통해 플라스틱이 금형의 윤곽에 정확하게 맞출 수 있습니다.
-
진공 압력 적용:
- 진공 펌프가 작동하여 가열된 플라스틱 시트를 금형 주위로 단단히 잡아당기는 흡입력을 생성합니다.이 단계를 통해 플라스틱이 미세한 디테일과 복잡한 형상을 포함하여 금형의 정확한 모양을 갖출 수 있습니다.
- 진공 압력은 에어 포켓을 제거하고 매끄럽고 균일한 표면을 보장할 수 있을 만큼 충분히 강해야 합니다.
-
냉각 및 응고:
- 플라스틱이 형성된 후 진공 압력을 유지한 채로 냉각 및 응고되도록 합니다.팬이나 물 스프레이를 사용하여 냉각 속도를 높일 수 있습니다.
- 일단 냉각되면 플라스틱은 금형의 모양을 유지하고 단단해집니다.
-
성형된 부품 제거하기:
- 진공이 해제되고 성형된 플라스틱 부품이 금형에서 제거됩니다.플래시라고 하는 여분의 재료를 잘라내어 최종 제품을 완성합니다.
- 부품은 용도에 따라 도장, 드릴링 또는 조립과 같은 추가 마감 공정을 거칠 수 있습니다.
-
진공 열성형의 장점:
- 비용 효율성:다른 성형 방식에 비해 툴링 비용이 낮아 시제품 제작 및 소량 생산에 이상적입니다.
- 디자인 유연성:복잡한 모양과 복잡한 디테일을 구현할 수 있습니다.
- 재료 효율성:남은 재료는 종종 재활용할 수 있으므로 낭비를 최소화합니다.
- 속도:사출 성형에 비해 생산 주기가 더 빠릅니다.
-
애플리케이션:
- 진공 열성형은 포장(예: 블리스터 팩, 트레이), 자동차(예: 인테리어 패널), 의료(예: 장비 하우징), 소비재(예: 장난감, 디스플레이) 등 다양한 산업에서 사용됩니다.
이러한 단계를 따르면 진공 열성형은 정밀한 모양과 디테일을 갖춘 고품질 플라스틱 부품을 생산할 수 있는 다양하고 효율적인 방법을 제공합니다.
요약 표:
단계 | 설명 |
---|---|
재료 준비 | 두께, 유연성, 내구성을 기준으로 열가소성 시트를 선택합니다.단단히 고정합니다. |
가열하기 | 유연해질 때까지 균일하게 가열합니다.온도는 플라스틱 종류에 따라 다릅니다. |
금형 위에 배치하기 | 정확한 모양을 위해 가열된 시트를 금형(목재, 알루미늄 또는 복합재) 위에 정렬합니다. |
진공 압력 | 흡입력을 가하여 플라스틱을 금형 주위로 단단히 끌어당겨 섬세한 디테일과 매끄러운 표면을 보장합니다. |
냉각 | 진공 압력으로 플라스틱을 식히고 굳히세요.선풍기나 물 스프레이로 속도를 높입니다. |
부품 제거하기 | 진공을 해제하고, 여분의 재료를 다듬고, 마감 공정(예: 페인팅, 드릴링)을 수행합니다. |
장점 | 비용 효율적, 설계 유연성, 재료 효율성, 빠른 생산 주기. |
애플리케이션 | 포장, 자동차, 의료 및 소비재 산업. |
진공 열성형 진공 열성형이 어떻게 생산을 간소화할 수 있는지 알아보세요. 지금 바로 문의하세요 전문가에게 문의하세요!