스퍼터링 공정은 기판에 박막을 증착하는 데 사용되는 물리적 기상 증착(PVD) 기술입니다. 여기에는 일반적으로 아르곤과 같은 불활성 가스에서 나오는 고에너지 이온이 표적 물질에 충격을 가해 원자가 표적 표면에서 방출되는 과정이 포함됩니다. 방출된 원자는 진공을 통해 이동하여 기판에 증착되어 얇고 균일한 필름을 형성합니다. 이 공정은 정밀도가 매우 높으며 우수한 접착력과 균일성을 지닌 고품질의 내구성 있는 필름을 생산할 수 있어 반도체, 광학, 코팅 등의 산업 분야에서 널리 사용됩니다.
설명된 핵심 사항:
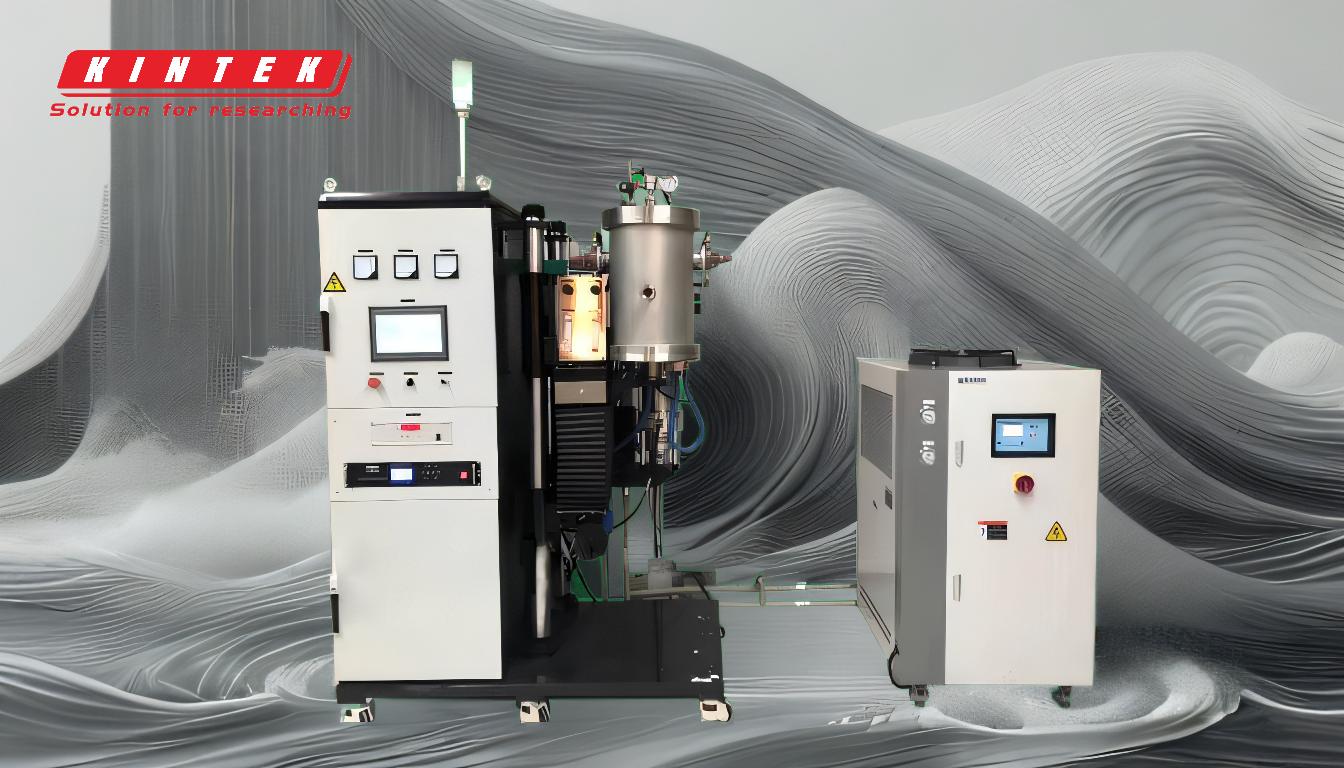
-
이온 폭격:
- 스퍼터링 공정은 일반적으로 아르곤과 같은 불활성 가스를 사용하여 플라즈마 생성으로 시작됩니다. 이 가스는 이온화되어 양전하를 띤 이온을 생성합니다.
- 그런 다음 이러한 이온은 음전하를 띠는 대상 물질을 향해 가속되어 이온을 대상 표면으로 이동시키는 강한 전기장을 생성합니다.
- 이러한 고에너지 이온이 표적 표면에 충돌하면 운동 에너지가 표적 원자에 전달되어 표적 원자가 표면에서 방출됩니다.
-
표적 원자의 방출:
- 이온이 표적 표면에 부딪치면 표적 물질에서 원자를 제거하기에 충분한 에너지를 전달합니다. 이 과정을 스퍼터링이라고 합니다.
- 방출된 원자는 중성이며 진공 챔버를 통해 기판을 향해 이동합니다.
- 이온 에너지와 충격 각도에 따라 스퍼터링 효율과 속도가 결정됩니다.
-
기판에 증착:
- 방출된 원자는 진공을 통해 이동하여 기판에 증착된 후 응축되어 얇은 필름을 형성합니다.
- 기판은 증착된 필름의 두께와 균일성을 제어하기 위해 타겟으로부터 다양한 각도와 거리에 위치할 수 있습니다.
- 필름의 접착력과 품질은 증착된 원자의 에너지, 기판의 청결도, 진공 조건과 같은 요인에 따라 달라집니다.
-
마그네트론 스퍼터링:
- 마그네트론 스퍼터링에서는 가스의 이온화를 강화하고 플라즈마 밀도를 높이기 위해 자기장이 사용됩니다.
- 자기장은 타겟 표면 근처에 전자를 가두어 전자와 가스 원자 사이의 충돌 가능성을 높이고, 결과적으로 이온 밀도를 증가시킵니다.
- 그 결과 스퍼터링 공정이 보다 효율적으로 이루어지고 증착 속도가 향상되고 필름 품질이 향상됩니다.
-
스퍼터링의 응용:
- 스퍼터링 공정은 반도체용 박막 생산, 광학 코팅, 보호 코팅 등 광범위한 응용 분야에 사용됩니다.
- 특히 금속, 합금, 세라믹 등 다양한 재료를 높은 정밀도와 균일성으로 증착하는 능력이 높이 평가됩니다.
- 이 공정은 내마모성과 내구성을 향상시키기 위해 절삭 공구에 사용되는 하드 코팅 생산에도 사용됩니다.
-
스퍼터링의 장점:
- 스퍼터링은 우수한 필름 균일성, 높은 접착력, 복잡한 재료를 증착하는 능력 등을 포함하여 다른 박막 증착 기술에 비해 여러 가지 장점을 제공합니다.
- 이 공정은 상대적으로 낮은 온도에서 수행될 수 있으므로 온도에 민감한 기판에 적합합니다.
- 스퍼터링은 또한 확장성이 뛰어나 소규모 실험실 연구와 대규모 산업 생산 모두에 적합합니다.
-
과제 및 고려 사항:
- 스퍼터링의 주요 과제 중 하나는 고진공이 필요하다는 점이며, 이로 인해 장비의 복잡성과 비용이 증가할 수 있습니다.
- 특히 후막의 경우 프로세스가 다른 증착 기술에 비해 상대적으로 느릴 수도 있습니다.
- 원하는 필름 특성을 얻으려면 가스 압력, 전력, 기판 온도 등 공정 매개변수를 주의 깊게 제어해야 합니다.
요약하면, 스퍼터링 공정은 전자공학에서 광학 코팅에 이르기까지 다양한 응용 분야에서 박막을 증착하는 다양하고 정밀한 방법입니다. 탁월한 접착력을 갖춘 고품질의 균일한 필름을 생산하는 능력은 현대 제조 및 연구에서 귀중한 도구입니다.
요약표:
주요 측면 | 세부 |
---|---|
프로세스 | 고에너지 이온을 사용하여 표적 원자를 방출하는 물리 기상 증착(PVD)입니다. |
주요 단계 | 이온 충격, 표적 원자의 방출 및 기판에의 증착. |
응용 | 반도체, 광학 코팅, 보호 코팅, 하드 코팅. |
장점 | 높은 도막 균일성, 우수한 접착력, 저온 가공성. |
도전과제 | 고진공이 필요하고 두꺼운 필름의 경우 속도가 느려질 수 있으며 정밀한 제어가 필요합니다. |
스퍼터링이 제조 공정을 어떻게 향상시킬 수 있는지 알아보십시오. 지금 전문가에게 문의하세요 !