볼 밀은 다양한 산업 분야에서 재료를 분쇄하고 혼합하는 데 널리 사용됩니다.효율성을 개선하면 상당한 비용 절감, 제품 품질 향상, 에너지 소비 감소로 이어질 수 있습니다.주요 전략에는 운영 매개변수 최적화, 적절한 장비 유지보수, 첨단 기술 사용이 포함됩니다.회전 속도, 연삭 매체, 재료 이송 속도, 라이너 설계와 같은 요소에 집중함으로써 볼 밀의 성능을 향상시킬 수 있습니다.또한 최신 제어 시스템과 모니터링 도구를 도입하면 효율성을 더욱 개선하고 가동 중단 시간을 줄일 수 있습니다.
핵심 사항을 설명합니다:
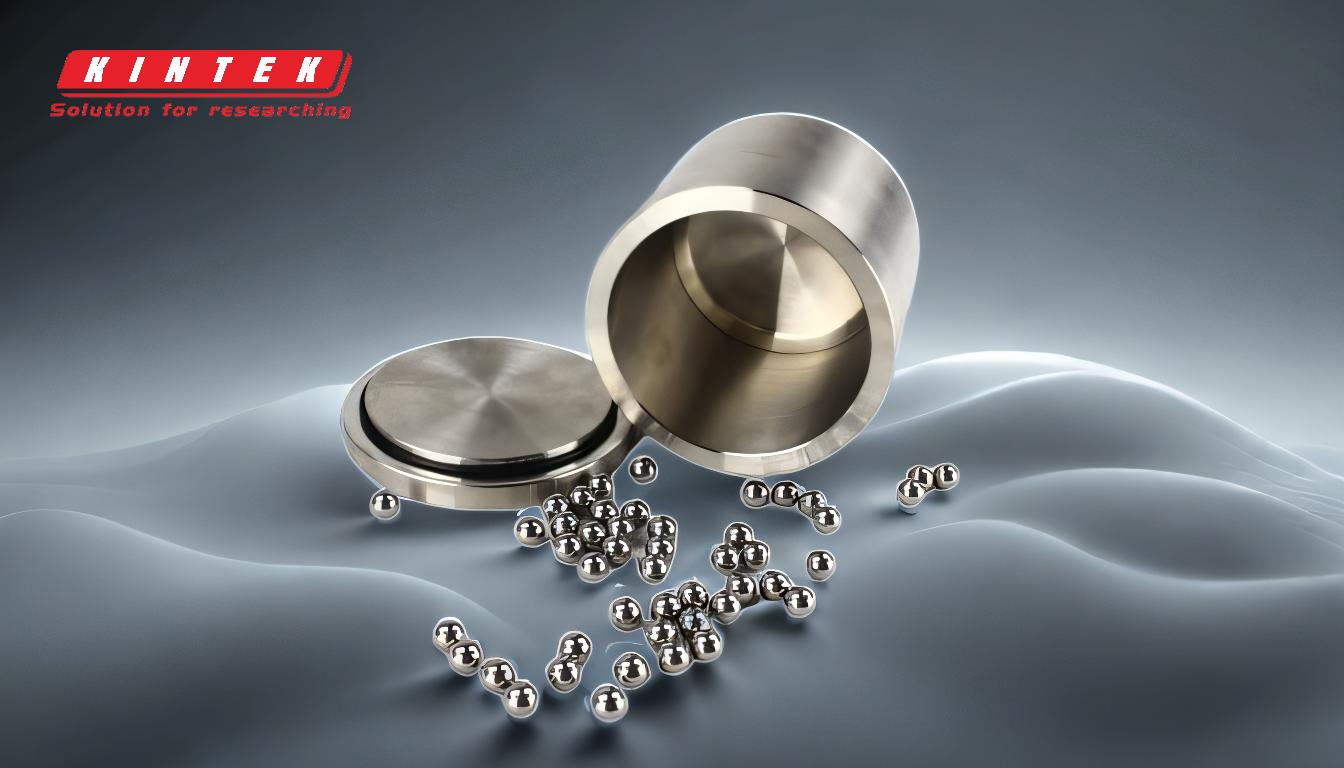
-
회전 속도 최적화:
- 볼 밀의 회전 속도는 효율성에 영향을 미치는 중요한 요소입니다.속도가 너무 낮으면 분쇄 매체가 효과적으로 캐스케이드되지 않아 분쇄가 불충분해집니다.반대로 속도가 너무 빠르면 분쇄 매체가 원심분리되어 분쇄 효율이 떨어질 수 있습니다.
- 임계 속도:최적의 속도는 일반적으로 분쇄 매체가 원심분리를 시작하는 속도인 임계 속도의 65~75%입니다.이 범위 내에서 작동하면 매체가 효과적으로 계단식 및 텀블링되어 분쇄 효율을 극대화할 수 있습니다.
-
적절한 분쇄 매체 선택:
- 분쇄 매체의 종류, 크기, 밀도는 분쇄 공정에 큰 영향을 미칩니다.큰 분쇄 매체는 거친 분쇄에 더 효과적이며, 작은 분쇄 매체는 미세 분쇄에 더 좋습니다.
- 재료:강철이나 세라믹과 같은 고밀도 재료가 일반적으로 사용됩니다.선택은 연마되는 재료와 원하는 미세도에 따라 달라집니다.
- 크기 분포:다양한 크기를 혼합하면 굵고 미세한 입자가 모두 효과적으로 분쇄되어 분쇄 효율이 향상됩니다.
-
재료 공급 속도 제어:
- 볼 밀에 재료가 공급되는 속도는 효율성에 영향을 미칩니다.밀에 과부하가 걸리면 비효율적인 연삭과 마모 증가로 이어질 수 있고, 과소부하는 과도한 에너지 소비를 초래할 수 있습니다.
- 최적의 이송 속도:일관되고 최적의 이송 속도를 유지하면 공장이 최고 효율로 작동할 수 있습니다.이는 밀의 부하에 따라 이송 속도를 조정하는 자동화된 이송 시스템을 통해 달성할 수 있습니다.
-
라이너 설계 개선:
- 볼 밀 내부의 라이너는 쉘을 마모로부터 보호하고 분쇄 매체를 들어올리는 데 도움을 줍니다.라이너의 디자인은 분쇄 매체의 움직임에 영향을 주어 분쇄 효율에 영향을 줄 수 있습니다.
- 라이너 프로파일:라이너의 모양과 재질은 미디어의 리프팅 작용을 극대화할 수 있도록 선택해야 합니다.최신 라이너는 연삭 매체의 궤적을 최적화하여 연삭 효율을 개선하도록 설계되었습니다.
- 재질:고무 또는 복합 소재와 같은 내마모성 소재로 제작된 라이너는 유지보수 가동 중단 시간을 줄이고 효율성을 향상시킬 수 있습니다.
-
적절한 볼 충전 유지:
- 분쇄기 내 분쇄 매체(볼)의 양과 분포는 효율적인 분쇄를 위해 매우 중요합니다.볼 충전량이 부족하면 연삭 품질이 떨어지고, 과도하게 충전되면 에너지 낭비가 발생할 수 있습니다.
- 볼 충전 수준:볼 충전 수준을 정기적으로 점검하고 유지하여 권장 범위 내에 있는지 확인하세요.주기적으로 새 볼을 추가하여 마모를 보완할 수 있습니다.
- 볼 크기 분포:볼 사이즈의 균형 잡힌 조합으로 거친 입자와 미세한 입자를 모두 효과적으로 분쇄할 수 있습니다.
-
고급 제어 시스템 사용:
- 최신 제어 시스템은 볼 밀의 작동 매개 변수를 실시간으로 모니터링하고 조정하여 최적의 성능을 보장합니다.
- 자동화:자동화된 시스템은 실시간 데이터를 기반으로 이송 속도, 회전 속도 및 기타 매개 변수를 조정하여 효율성을 개선하고 인적 오류를 줄일 수 있습니다.
- 모니터링:고급 센서와 모니터링 도구는 공장의 성능에 대한 귀중한 데이터를 제공하여 운영자가 정보에 입각한 의사 결정을 내리고 잠재적인 문제를 예방할 수 있도록 지원합니다.
-
에너지 소비량 감소:
- 에너지 효율은 볼 밀 성능을 개선하는 데 있어 핵심적인 고려 사항입니다.에너지 소비를 줄이면 운영 비용이 낮아질 뿐만 아니라 환경에 미치는 영향도 최소화할 수 있습니다.
- 가변 속도 드라이브:가변 속도 드라이브를 사용하면 밀이 다양한 연삭 작업에 맞는 최적의 속도로 작동하여 에너지 소비를 줄일 수 있습니다.
- 에너지 회수 시스템:에너지 회수 시스템을 구현하면 손실될 수 있는 에너지를 회수하고 재사용하여 효율성을 더욱 향상시킬 수 있습니다.
-
정기적인 유지보수 및 점검:
- 볼 밀을 최적의 상태로 유지하려면 정기적인 유지보수 및 점검이 필수적입니다.유지보수를 소홀히 하면 마모가 증가하고 효율성이 떨어지며 가동 중단으로 인한 비용이 발생할 수 있습니다.
- 예약 유지보수:정기적인 유지보수 프로그램을 구현하여 라이너 및 연삭 매체와 같은 마모된 부품을 정기적으로 검사하고 교체합니다.
- 상태 모니터링:상태 모니터링 도구를 사용하여 마모 또는 오작동의 조기 징후를 감지하여 적시에 개입하고 주요 문제를 예방할 수 있습니다.
-
재료 속성 최적화:
- 경도, 수분 함량, 입자 크기 분포 등 분쇄되는 재료의 특성은 볼 밀의 효율에 영향을 미칠 수 있습니다.
- 수분 제어:과도한 수분은 막힘과 분쇄 효율 저하로 이어질 수 있습니다.재료를 적절히 건조하거나 전처리하면 최적의 수분 수준을 유지하는 데 도움이 될 수 있습니다.
- 입자 크기:재료를 볼 밀에 공급하기 전에 더 작은 크기로 사전 분쇄하면 분쇄 효율을 높이고 에너지 소비를 줄일 수 있습니다.
-
고급 연삭 기술 채택:
- 고압 연삭 롤(HPGR) 또는 교반식 밀과 같은 새로운 연삭 기술을 볼 밀과 함께 사용하여 전반적인 효율성을 향상시킬 수 있습니다.
- 하이브리드 시스템:다양한 연삭 기술을 결합하면 연삭 공정을 최적화하여 에너지 소비를 줄이고 제품 품질을 개선할 수 있습니다.
- 혁신적인 디자인:수직 롤러 밀 또는 수평 볼 밀과 같은 혁신적인 밀 설계를 탐색하면 효율성과 성능을 개선할 수 있는 새로운 방법을 찾을 수 있습니다.
이러한 핵심 영역에 집중함으로써 볼 밀의 효율성을 크게 개선하여 성능 향상, 에너지 소비 감소, 운영 비용 절감으로 이어질 수 있습니다.
요약 표:
주요 전략 | 세부 정보 |
---|---|
회전 속도 최적화 | 효과적인 캐스케이딩 및 텀블링을 위해 임계 속도의 65~75%에서 작동합니다. |
분쇄 매체 선택 | 고밀도 재료(강철/세라믹)와 혼합 크기를 사용하여 더 나은 연삭을 위해 사용합니다. |
재료 이송 속도 제어 | 과부하 또는 과소 부하를 방지하기 위해 일관된 이송 속도를 유지하세요. |
라이너 디자인 개선 | 내마모성 소재와 최적의 프로파일을 사용하여 미디어 이동성을 향상하세요. |
볼 충전 유지 | 볼 충전 수준과 크기 분포를 정기적으로 점검하고 조정하세요. |
고급 제어 시스템 사용 | 실시간 조정 및 효율성을 위해 운영을 자동화하고 모니터링하세요. |
에너지 소비량 감소 | 가변 속도 드라이브 및 에너지 회수 시스템을 구현하세요. |
정기 유지보수 | 점검 일정을 예약하고 상태 모니터링을 사용하여 다운타임을 방지하세요. |
재료 특성 최적화 | 분쇄 효율을 높이기 위해 수분을 제어하고 재료를 미리 분쇄합니다. |
고급 기술 채택 | 볼 밀과 HPGR 또는 교반 밀을 결합하여 하이브리드 효율을 높일 수 있습니다. |
볼 밀의 효율성을 최적화할 준비가 되셨나요? 지금 바로 문의하세요 에 문의하여 전문가의 안내와 솔루션을 받으세요!