볼 밀의 효율은 회전 속도, 분쇄 매체의 크기와 유형, 분쇄할 재료의 크기와 유형, 밀의 충진 비율 등 다양한 요인의 영향을 받습니다. 밀 챔버 내 재료의 체류 시간, 볼의 크기, 밀도 및 개수, 연삭 재료의 경도, 이송 속도 및 실린더의 회전 속도와 같은 다른 요인도 중요한 역할을 합니다. 또한 드럼 직경, 드럼 직경과 길이의 비율, 공급 재료의 물리적-화학적 특성, 아머 표면 모양, 분쇄 미세도, 분쇄된 제품의 적시 제거도 생산성을 최적화하는 데 중요합니다.
핵심 포인트 설명:
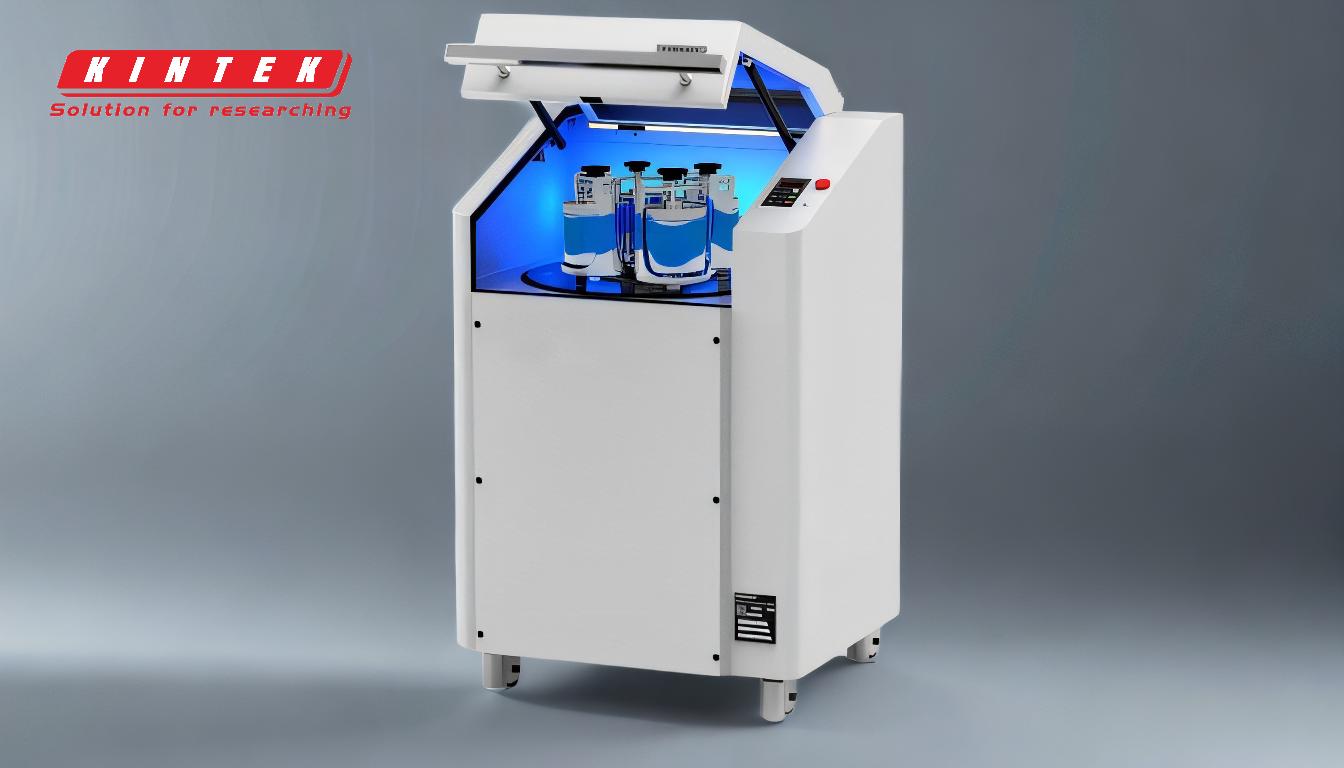
-
회전 속도
- 볼 밀의 회전 속도는 연삭 매체의 움직임을 결정하기 때문에 매우 중요합니다. 속도가 너무 낮으면 볼이 충분히 높이 들어올려지지 않아 상당한 충격이 발생하여 연삭 효율이 떨어집니다. 반대로 속도가 너무 빠르면 볼이 원심분리되어 밀 벽에 달라붙어 재료를 효과적으로 분쇄하지 못할 수 있습니다. 임계 속도라고도 하는 최적의 속도는 일반적으로 밀의 임계 속도의 약 65~75%입니다.
-
연삭 매체의 크기와 유형
- 분쇄기에 사용되는 볼 또는 분쇄 매체의 크기와 유형은 분쇄 효율에 큰 영향을 미칩니다. 큰 볼은 거친 재료를 분해하는 데 더 효과적이며, 작은 볼은 미세한 분쇄에 더 좋습니다. 분쇄 매체(예: 강철, 세라믹)의 재질도 분쇄 공정에 영향을 미치며, 일반적으로 더 단단한 재료는 분쇄 효율이 더 좋지만 분쇄기에 더 많은 마모를 유발할 수 있습니다.
-
연삭할 재료의 크기 및 유형
- 경도, 크기, 수분 함량 등 분쇄되는 재료의 특성은 분쇄 공정에 영향을 미칩니다. 단단한 재료는 분쇄에 더 많은 에너지가 필요하고 수분 함량이 높은 재료는 막힘과 효율 저하로 이어질 수 있습니다. 공급 재료의 초기 입자 크기도 분쇄 효율에 영향을 미치며, 일반적으로 미세한 공급 재료는 원하는 입도에 도달하는 데 더 적은 에너지가 필요합니다.
-
분쇄기의 충진 비율
- 충진 비율, 즉 분쇄 매체로 채워진 분쇄기 부피의 비율은 중요한 요소입니다. 최적의 충진 비율은 밀에 과부하가 걸리지 않고 재료를 효과적으로 분쇄할 수 있는 충분한 분쇄 매체를 보장하며, 이는 효율성을 떨어뜨릴 수 있습니다. 일반적으로 대부분의 볼 밀에서는 약 30~40%의 충진 비율이 최적으로 간주됩니다.
-
밀 챔버 내 재료의 체류 시간
- 재료가 밀 챔버에 머무는 시간, 즉 체류 시간은 연삭 정도에 영향을 미칩니다. 체류 시간이 길면 일반적으로 더 미세한 연삭이 가능하지만 에너지가 낭비되는 과연삭으로 이어질 수도 있습니다. 체류 시간은 이송 속도와 밀의 설계를 조정하여 제어할 수 있습니다.
-
용기의 이송 속도 및 레벨
- 분쇄기에 재료가 공급되는 속도와 분쇄기 용기의 재료 수준은 분쇄 공정에 영향을 미칩니다. 일관되고 적절한 이송 속도는 일정한 분쇄 조건을 보장하는 반면, 이송 속도가 일정하지 않으면 분쇄 효율의 변동이 발생할 수 있습니다. 분쇄 매체가 재료와 효과적으로 상호 작용할 수 있도록 용기의 재료 수준을 유지해야 합니다.
-
드럼 직경 및 길이 대 직경 비율
- 분쇄기 드럼의 치수, 특히 직경과 길이 대 직경(L:D) 비율은 연삭 효율에 영향을 미칩니다. 드럼 직경이 클수록 충격력이 커지고, L:D 비율은 분쇄기 내 분쇄 매체와 재료의 분포에 영향을 미칩니다. 최적의 L:D 비율은 일반적으로 1.56에서 1.64 사이입니다.
-
공급 재료의 물리-화학적 특성
- 경도, 마모성 및 화학 성분과 같은 공급 재료의 물리적 및 화학적 특성은 연삭 공정에 큰 영향을 미칠 수 있습니다. 연마성이 강한 재료는 분쇄 매체와 분쇄기 라이닝에 더 많은 마모를 유발하여 시간이 지남에 따라 효율을 떨어뜨릴 수 있습니다.
-
아머 표면 모양
- 분쇄기 내부 라이닝 또는 아머의 모양과 디자인은 분쇄 매체와 분쇄되는 재료의 움직임에 영향을 줄 수 있습니다. 잘 설계된 아머 표면은 분쇄 매체의 혼합과 충격을 더 잘 촉진하여 분쇄 작용을 향상시킬 수 있습니다.
-
분쇄 미세도 및 연삭된 제품의 적시 제거
- 연삭된 제품의 원하는 입도는 연삭 공정에 영향을 미치며, 일반적으로 더 미세한 제품은 더 많은 에너지와 시간을 필요로 합니다. 또한 분쇄기에서 분쇄된 제품을 적시에 제거하는 것은 과분쇄를 방지하고 효율적인 작동을 유지하는 데 매우 중요합니다. 그레이트 배출 또는 오버플로 배출과 같은 적절한 배출 메커니즘은 최적의 분쇄 조건을 유지하는 데 필수적입니다.
요약 표:
요인 | 효율성에 미치는 영향 |
---|---|
회전 속도 | 연삭 매체 동작을 결정하며, 최적 속도는 임계 속도의 65~75%입니다. |
연삭재의 크기 및 유형 | 거친 연삭에는 큰 볼, 미세한 연삭에는 작은 볼, 재료는 마모와 효율에 영향을 줍니다. |
연삭할 재료 | 경도, 크기 및 수분 함량은 에너지 요구량과 막힘 위험에 영향을 미칩니다. |
충진 비율 | 최적의 비율(30-40%)로 과부하 없이 효과적인 연삭을 보장합니다. |
체류 시간 | 시간이 길수록 더 미세하게 분쇄되지만 과분쇄의 위험이 있으며, 이송 속도로 제어됩니다. |
이송 속도 및 레벨 | 일관된 이송으로 안정적인 분쇄를 유지하며, 용기 높이가 매체와 재료의 접촉을 보장합니다. |
드럼 치수 | 직경이 클수록 충격력이 증가하며, 최적의 L:D 비율은 1.56-1.64입니다. |
재료 특성 | 마모성과 경도는 마모와 에너지 소비에 영향을 미칩니다. |
아머 표면 형상 | 미디어와 재료의 상호 작용을 개선하여 연삭 작용을 향상시킵니다. |
밀링 미세도 및 배출 | 제품이 미세할수록 더 많은 에너지가 필요하므로 적시에 제거하면 과도한 연삭을 방지할 수 있습니다. |
볼 밀 효율을 최적화할 준비가 되셨나요? 지금 바로 전문가에게 문의하세요. 맞춤형 솔루션을 찾아보세요!