압축 성형은 고무, 플라스틱 또는 금속과 같은 원재료를 열과 압력을 사용하여 원하는 형태로 성형하는 제조 공정입니다.이 공정은 미리 측정된 재료를 금형 캐비티에 넣는 것으로 시작됩니다.그런 다음 금형을 닫고 압력을 가하여 재료를 압축하여 재료가 흐르고 캐비티를 채우도록 합니다.열은 종종 재료를 부드럽게 하여 성형하기 쉽고 생산 속도를 높이는 데 사용됩니다.몰드 플래시라고 하는 여분의 재료는 특수 홈을 통해 배출됩니다.이 방법은 자동차 제조와 같은 산업에서 선바이저나 기어 노브와 같은 내부 부품을 제작하는 데 널리 사용됩니다.그러나 재료를 정확하게 측정하고 적절한 배치를 보장하여 흐름선, 기포 또는 미충진 부품과 같은 결함을 방지하는 등의 과제를 해결해야 합니다.
핵심 사항을 설명합니다:
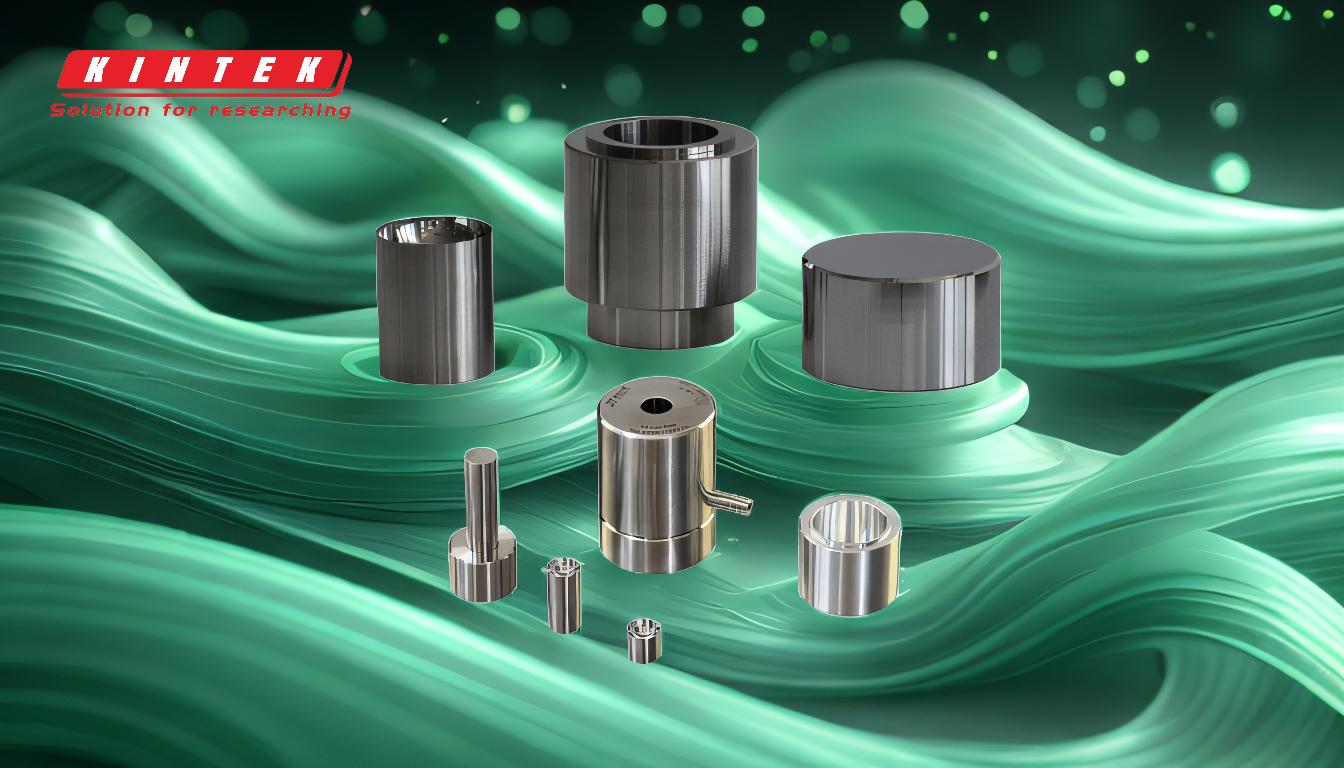
-
금형 및 재료 준비:
- 재료 선택:원하는 제품에 따라 고무, 플라스틱, 금속 등 적절한 원재료를 선택합니다.
- 금형 디자인:금형이 올바른 캐비티 모양으로 설계되었는지, 여분의 재료(금형 플래시)가 빠져나갈 수 있는 홈이 있는지 확인합니다.
- 재료 측정:재료를 정확하게 자르거나 무게를 측정하여 각 캐비티에 알맞은 양이 들어가도록 합니다.재료가 너무 적으면 결함이 발생할 수 있고, 너무 많으면 과도한 플래시가 발생할 수 있습니다.
-
충전 삽입하기:
- 배치:미리 측정한 재료를 바닥 몰드 캐비티 중앙에 놓습니다.균일한 분포를 보장하고 결함을 방지하려면 올바른 배치가 중요합니다.
- 재료 모양:모양이 좋고 가지가 없는 고무 스톡 또는 기타 재료를 사용하여 금형 내부의 원활한 흐름을 촉진합니다.
-
몰드 닫기:
- 압력 적용:상단 몰드를 닫고 유압 프레스 또는 유사한 장비를 사용하여 압력을 가합니다.압력을 가하면 재료가 흐르면서 캐비티를 채웁니다.
- 온도 제어:금형을 일정한 온도로 유지하여 재료를 부드럽게 만들어 성형이 용이하고 생산 공정이 빨라집니다.
-
부품 성형:
- 재료 흐름:압력과 열을 받으면 재료가 흐르면서 금형 캐비티를 완전히 채웁니다.여분의 재료는 특수 홈을 통해 몰드 플래시로 배출됩니다.
- 경화 시간:재료가 금형 내에서 경화되고 굳을 수 있도록 충분한 시간을 허용합니다.경화 시간은 재료 유형과 최종 제품의 원하는 특성에 따라 다릅니다.
-
파트 제거:
- 금형 열기:재료가 경화되면 새로 형성된 파트가 손상되지 않도록 조심스럽게 몰드를 엽니다.
- 플래시 트리밍:홈에서 흘러나온 여분의 재료(몰드 플래시)를 제거합니다.이 단계에서는 추가적인 트리밍 또는 마감 공정이 필요할 수 있습니다.
-
과제 및 솔루션:
- 재료 측정:정확한 측정이 중요합니다.정확한 계량 또는 절단 도구를 사용하여 정확한 양의 재료가 사용되도록 하세요.
- 결함 예방:적절한 배치와 적절한 압력은 흐름선, 기포 또는 미충진 부품과 같은 결함을 방지하는 데 도움이 됩니다.과도한 재료는 제거하기 어려운 무거운 플래시를 유발할 수 있습니다.
- 프로세스 최적화:압력, 온도, 경화 시간을 정기적으로 모니터링하고 조정하여 공정을 최적화하고 제품 품질을 개선합니다.
-
애플리케이션:
- 자동차 산업:압축 성형은 선바이저, 기어 노브, 트림 커버와 같은 내장 부품을 제조하는 데 이상적입니다.이 공정은 효율적이고 비용 효율적이어서 재료 낭비와 인건비를 절감할 수 있습니다.
- 기타 산업:이 방법은 단순한 플라스틱 부품부터 복잡한 고무 부품까지 다양한 제품을 생산하기 위해 다른 여러 산업 분야에서도 사용됩니다.
이러한 단계를 따르고 문제를 해결하면 압축 성형은 폐기물을 최소화하면서 고품질 부품을 생산하는 데 매우 효과적인 방법이 될 수 있습니다.
요약 표:
주요 단계 | 설명 |
---|---|
소재 선택 | 제품 요구 사항에 따라 고무, 플라스틱 또는 금속을 선택합니다. |
몰드 디자인 | 여분의 재료(몰드 플래시)를 위한 적절한 캐비티와 홈이 있는 금형을 설계합니다. |
재료 측정 | 재료의 무게를 정확하게 측정하거나 절단하여 결함이나 과도한 플래시를 방지합니다. |
충전물 삽입하기 | 재료를 몰드 중앙에 배치하여 고르게 분포되도록 합니다. |
몰드 닫기 | 압력과 열을 가하여 재료를 부드럽게 하고 모양을 만듭니다. |
부품 성형 | 재료가 금형 내에서 흐르고 경화되도록 합니다. |
파트 제거 | 몰드를 열고 여분의 플래시를 다듬어 깔끔하게 마무리합니다. |
애플리케이션 | 자동차 및 산업 제조 분야에서 널리 사용됩니다. |
압축 성형으로 제조 공정을 최적화할 준비가 되셨나요? 지금 바로 전문가에게 문의 에 문의하여 시작하세요!