볼 밀에서 달성되는 입자 크기는 재료의 초기 입자 크기, 분쇄 매체(볼)의 크기와 유형, 분쇄 시간, 회전 속도 및 충전 비율과 같은 작동 매개변수 등 여러 요인에 따라 달라집니다.일반적으로 볼 밀은 입자 크기를 1~20μm 범위로 줄이는 데 사용되며, 볼이 작고 분쇄 시간이 길수록 입자가 더 미세해집니다.최종 입자 크기는 분쇄 주기, 체류 시간 및 분쇄기의 특정 작동 조건에 의해 영향을 받습니다.
핵심 포인트 설명:
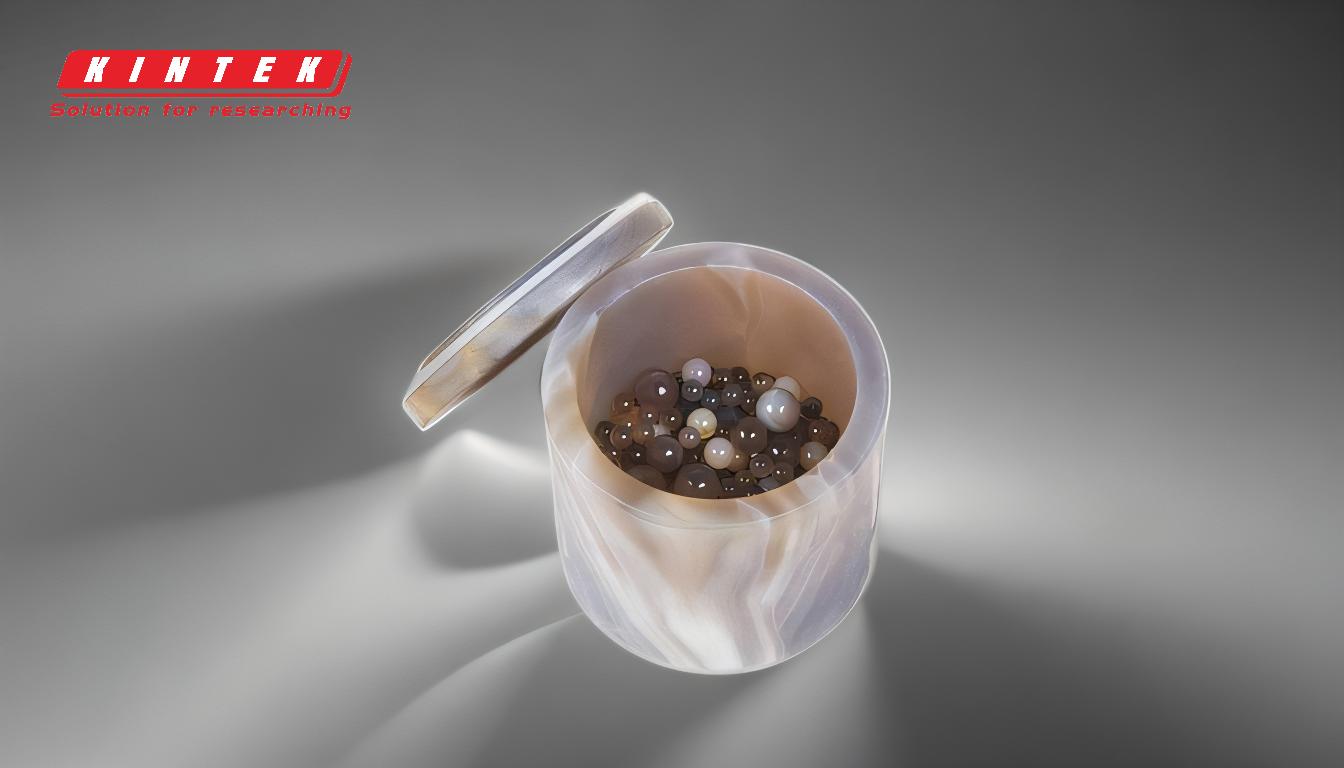
-
볼 밀의 일반적인 입자 크기 범위:
- 볼 밀은 일반적으로 다음과 같은 범위의 입자 크기를 달성하는 데 사용됩니다. 1-20 μm 특히 세라믹 실험실과 광석 분쇄 공정에서 사용됩니다.
- 분쇄되는 재료의 초기 평균 입자 크기(d50)는 최종 입자 크기를 결정하는 데 중요한 역할을 합니다.
-
입자 크기에 영향을 미치는 요인:
- 분쇄 매체(볼): 볼이 작을수록 더 미세한 입자를 만드는 데 더 효과적입니다.볼의 크기, 밀도, 개수는 분쇄 효율에 직접적인 영향을 미칩니다.
- 연삭 시간: 연삭 시간이 길수록 재료가 더 많은 충돌과 마모를 겪기 때문에 일반적으로 입자 크기가 작아집니다.
- 체류 시간: 재료가 밀 챔버에 머무는 시간은 크기 감소 정도에 영향을 미칩니다.체류 시간이 길수록 더 철저하게 연삭할 수 있습니다.
- 회전 속도: 밀이 회전하는 속도는 연삭 매체와 재료에 전달되는 에너지에 영향을 미칩니다.속도가 높을수록 연삭 효율이 향상될 수 있지만 과도한 마모나 과열을 방지하기 위해 최적화해야 합니다.
- 충진 비율: 분쇄 매체(볼)로 채워진 분쇄기 부피의 비율은 분쇄 성능에 영향을 미칩니다.최적의 충진 비율은 분쇄기에 과부하를 주지 않고 효율적인 연삭을 보장합니다.
-
작동 매개변수:
- 드럼 치수: 드럼의 직경과 길이, 드럼 직경과 길이의 비율(최적 L:D 비율은 1.56-1.64)이 분쇄 효율에 영향을 줍니다.
- 이송 속도 및 레벨: 분쇄기에 재료가 공급되는 속도와 용기의 재료 레벨은 연삭 공정에 영향을 미칠 수 있습니다.일관된 이송 속도는 최적의 연삭 조건을 유지하는 데 도움이 됩니다.
- 재료 특성: 분쇄되는 재료의 경도와 물리-화학적 특성은 분쇄 효율과 최종 입자 크기를 결정하는 데 중요한 역할을 합니다.
-
특정 응용 분야를 위한 최적화:
- 산업 응용 분야에서는 원하는 입자 크기 분포를 달성하기 위해 볼 밀 매개변수를 최적화하는 것이 중요합니다.여기에는 적절한 볼 크기 선택, 회전 속도 조정, 충전 비율 제어 등이 포함됩니다.
- 세라믹 애플리케이션의 경우 특정 입자 크기 범위의 시작 분말을 완전히 혼합한 상태를 달성하는 것이 목표인 경우가 많습니다.
-
실용적인 고려 사항:
- 연삭 사이클: 분쇄 사이클 수와 분쇄기 내부 체류 시간에 따라 크기 감소 정도가 결정됩니다.원하는 미세도를 얻으려면 여러 사이클이 필요할 수 있습니다.
- 분쇄된 제품을 적시에 제거합니다: 분쇄기에서 분쇄물을 효율적으로 제거하면 과분쇄를 방지하고 일관된 입자 크기 분포를 보장할 수 있습니다.
이러한 요소를 신중하게 제어함으로써 작업자는 산업용 광석 분쇄 또는 세라믹 분말 제조 등 볼 밀링 공정에서 원하는 입자 크기를 달성할 수 있습니다.
요약 표:
요인 | 입자 크기에 미치는 영향 |
---|---|
분쇄 매체(볼) | 볼이 작을수록 입자가 미세해지며 크기, 밀도, 개수가 분쇄 효율에 영향을 미칩니다. |
분쇄 시간 | 분쇄 시간이 길어지면 충돌과 마모가 증가하여 입자가 더 작아집니다. |
회전 속도 | 속도가 높을수록 연삭 효율이 향상되지만 마모나 과열을 방지하기 위해 최적화해야 합니다. |
충진 비율 | 최적의 충진 비율로 분쇄기에 과부하가 걸리지 않고 효율적인 분쇄를 보장합니다. |
드럼 치수 | 직경, 길이 및 L:D 비율은 연삭 효율에 영향을 미칩니다. |
재료 속성 | 경도 및 물리화학적 특성은 분쇄 효율과 최종 입자 크기에 영향을 미칩니다. |
정밀한 입자 크기를 위해 볼 밀링 공정을 최적화하세요. 지금 바로 전문가에게 문의하세요 !