투 플레이트 몰드는 단순성과 비용 효율성으로 인해 사출 성형에 널리 사용됩니다.그러나 특히 다중 캐비티 디자인에서는 몇 가지 단점이 있습니다.주요 과제 중 하나는 여러 캐비티에 걸쳐 용융된 플라스틱의 흐름 균형을 맞추는 것으로, 이로 인해 최종 제품에 고르지 않은 충진 및 결함이 발생할 수 있습니다.또한 2판 몰드에서 파팅 라인과 게이트의 정렬은 설계 및 제조 공정을 복잡하게 만들 수 있습니다.이러한 제한 사항은 생산의 효율성, 품질 및 비용에 영향을 미칠 수 있으므로 특정 애플리케이션에 대한 적합성을 신중하게 평가하는 것이 필수적입니다.
핵심 사항을 설명합니다:
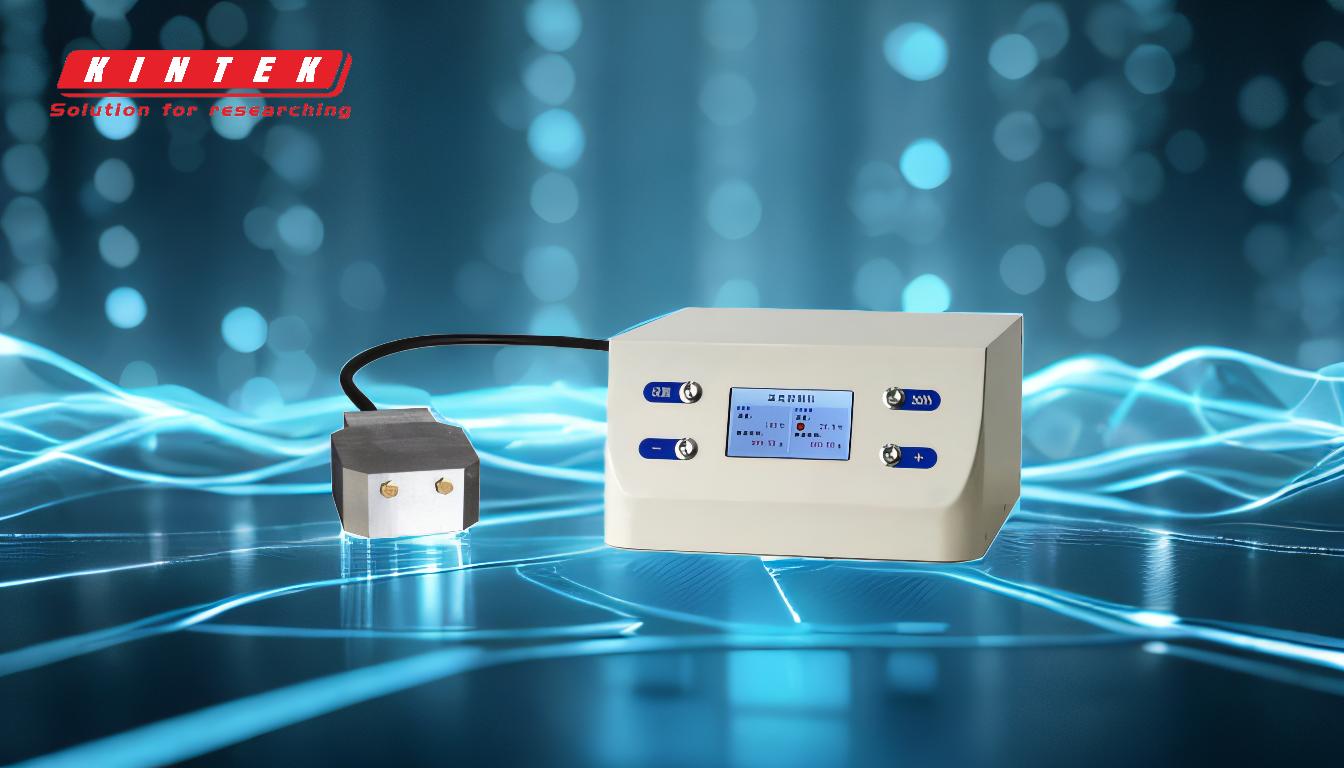
-
용융 플라스틱 흐름의 균형을 맞추기 위한 과제:
- 다중 캐비티 2판 금형에서는 용융된 플라스틱을 각 캐비티에 균일하게 분배하는 것이 어렵습니다.
- 흐름이 고르지 않으면 숏샷, 뒤틀림 또는 일관되지 않은 부품 치수와 같은 결함이 발생할 수 있습니다.
- 이 문제는 캐비티가 게이트에서 다양한 거리에 위치한 복잡한 설계에서 더욱 악화됩니다.
-
게이트와 파팅 라인의 정렬:
- 2판 몰드의 파팅 라인은 게이트와 정렬되어야 하므로 설계 유연성이 제한됩니다.
- 이러한 정렬은 특히 복잡한 부품이나 다중 캐비티 설정의 경우 금형 설계를 복잡하게 만들 수 있습니다.
- 또한 파팅 라인에서 플래시 형성 또는 기타 결함의 위험이 증가할 수 있습니다.
-
제한된 설계 유연성:
- 2판 금형은 3판 금형이나 핫 러너 시스템에 비해 활용도가 떨어집니다.
- 복잡한 게이팅이 필요한 부품이나 특정 미적 요구 사항이 있는 부품에는 적합하지 않습니다.
- 투 플레이트 몰드의 단순성 때문에 사용자 지정 옵션이 줄어드는 대가를 치르는 경우가 많습니다.
-
더 높은 결함 위험:
- 흐름 밸런싱과 게이트 정렬의 어려움으로 인해 2판 금형은 결함이 발생하기 쉽습니다.
- 일반적인 문제로는 용접 라인, 에어 트랩, 일관되지 않은 부품 품질 등이 있습니다.
- 이러한 결함은 불량률과 생산 비용을 증가시킬 수 있습니다.
-
더 긴 사이클 시간:
- 2판 몰드의 한계로 인해 냉각 및 사이클 시간이 길어질 수 있습니다.
- 특히 고르지 않은 냉각이 발생할 수 있는 다중 캐비티 금형의 경우 더욱 그렇습니다.
- 사이클 시간이 길어지면 전반적인 생산 효율성이 떨어지고 운영 비용이 증가합니다.
-
더 높은 유지보수 요구 사항:
- 유량 밸런싱과 게이트 정렬의 복잡성으로 인해 금형의 마모가 증가할 수 있습니다.
- 일관된 성능을 보장하려면 정기적인 유지보수가 필요하므로 총소유비용이 증가합니다.
-
모든 애플리케이션에 적합하지 않음:
- 2판 몰드는 간단한 게이팅 요구 사항이 있는 간단한 부품에 가장 적합합니다.
- 복잡한 부품이나 고정밀 애플리케이션의 경우 다른 금형 설계(예: 3판 금형 또는 핫 러너 시스템)가 더 적합할 수 있습니다.
제조업체는 이러한 단점을 이해함으로써 2판 금형이 특정 생산 요구 사항에 적합한 선택인지에 대해 정보에 입각한 결정을 내릴 수 있습니다.투 플레이트 몰드는 단순성과 비용 절감 효과를 제공하지만, 프로젝트의 요구 사항과 비교하여 그 한계를 신중하게 검토해야 합니다.
요약 표:
단점 | 영향 |
---|---|
흐름 밸런싱 문제 | 고르지 않은 충전, 짧은 샷, 뒤틀림 또는 일관되지 않은 치수와 같은 결함. |
파팅 라인 정렬 | 설계 유연성 제한, 플래시 형성 위험 증가. |
제한된 설계 유연성 | 복잡한 부품이나 특정 미적 요구 사항에 대한 활용도가 떨어집니다. |
더 높은 결함 위험 | 용접 라인, 에어 트랩, 일관되지 않은 부품 품질로 인해 불량률이 높아집니다. |
더 긴 사이클 시간 | 고르지 않은 냉각은 생산 효율성 저하로 이어집니다. |
더 많은 유지보수 필요성 | 마모와 파손이 증가하여 정기적인 유지보수가 필요합니다. |
모든 애플리케이션에 적합하지 않음 | 단순한 부품에 적합하며 복잡한 디자인에는 대체 금형이 필요할 수 있습니다. |
프로젝트에 적합한 금형을 선택하는 데 도움이 필요하신가요? 지금 바로 전문가에게 문의하세요. 맞춤형 솔루션에 대해 문의하세요!