분말 야금은 금속 분말로 부품을 생산하는 다목적 제조 공정입니다.이 공정은 금속 분말의 특성, 최종 부품의 요구 사항, 공정에 사용되는 특정 기술 등 여러 가지 요소의 영향을 받습니다.주요 고려 사항으로는 분말의 유량, 밀도, 압축성, 강도는 물론 내식성, 경도, 인장 강도, 충격 인성, 피로 강도 등 금속의 기계적 특성이 있습니다.또한 기존 방식, 사출 성형, 등압 프레스, 적층 제조 등 공정의 선택도 최종 제품의 특성을 결정하는 데 중요한 역할을 합니다.분말 야금에서 중요한 단계인 소결은 분말 입자를 완전히 녹이지 않고 결합하기 위해 부품을 가열하여 최종 부품의 구조적 무결성을 보장합니다.
핵심 사항을 설명합니다:
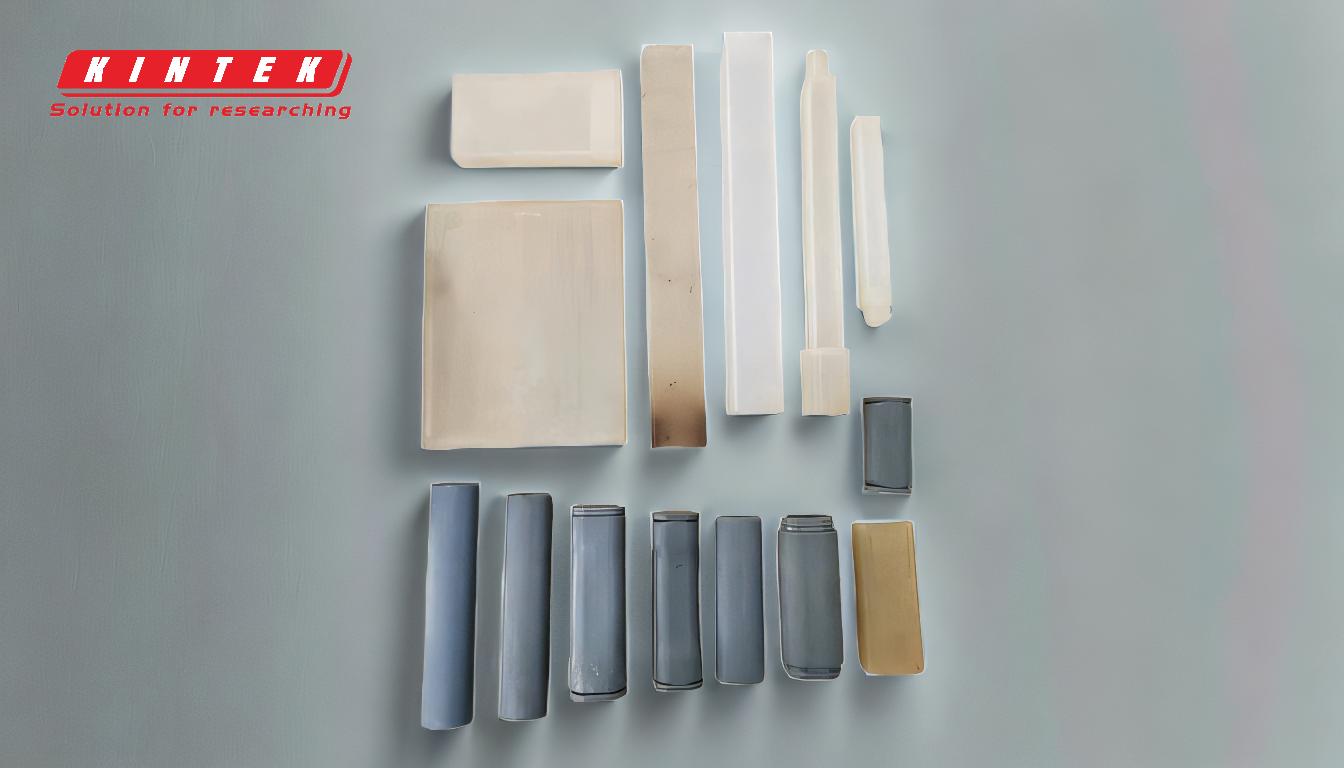
-
파우더 속성:
- 유속:파우더가 자유롭게 흐르는 능력은 금형과 금형을 균일하게 채우는 데 매우 중요합니다.우수한 유동 특성을 가진 파우더는 일관된 부품 밀도와 모양을 보장합니다.
- 밀도:파우더의 밀도는 최종 부품의 밀도와 기계적 특성에 영향을 미칩니다.일반적으로 밀도가 높은 파우더는 더 튼튼한 부품으로 이어집니다.
- 압축성:압력을 가했을 때 분말이 얼마나 잘 압축되는지를 나타냅니다.최소한의 다공성으로 고밀도 부품을 만들려면 압축성이 높을수록 바람직합니다.
- 강도:파우더 입자의 고유한 강도는 최종 부품의 강도와 내구성에 영향을 미칩니다.
-
금속 선택 기준:
- 내식성:내식성이 높은 금속은 해양 또는 화학 분야와 같이 열악한 환경에 노출되는 부품에 선택됩니다.
- 경도:경도는 기어나 베어링과 같이 내마모성이 필요한 부품에 매우 중요한 요소입니다.
- 인장 강도:이 속성은 높은 응력이나 하중을 견뎌야 하는 부품에 중요합니다.
- 충격 인성:갑작스러운 충격이나 충격을 받을 수 있는 부품에는 충격 인성이 우수한 금속을 선택합니다.
- 피로 강도:이는 자동차 또는 항공우주 부품과 같이 주기적으로 하중을 받는 부품에 매우 중요합니다.
-
공정 변형:
- 기존 방법:여기에는 단순 부품에서 중간 정도의 복잡한 부품을 생산하는 데 널리 사용되는 프레스 및 소결이 포함됩니다.
- 사출 성형:금속 사출 성형(MIM)을 사용하면 복잡한 형상의 복잡한 고정밀 부품을 생산할 수 있습니다.
- 등방성 프레싱:열간 등방성 프레스(HIP)는 항공 우주 및 의료 분야에서 자주 사용되는 고밀도 및 균일한 특성을 가진 부품을 생산하는 데 사용됩니다.
- 적층 제조:재료 낭비를 최소화하면서 고도로 복잡한 맞춤형 부품을 생산할 수 있는 최신 기술입니다.
-
소결 공정:
- 온도 제어:소결은 1차 금속의 녹는점보다 약간 낮은 온도에서 수행되어 분말 입자가 녹지 않고 서로 결합되도록 합니다.
- 본딩 메커니즘:열로 인해 입자가 서로 확산되어 우수한 기계적 특성을 가진 고체 부품이 생성됩니다.
- 최종 속성:소결 공정은 최종 부품의 밀도, 강도 및 치수 정확도에 큰 영향을 미칩니다.
-
분말 야금 기술:
- 금속 사출 성형(MIM):플라스틱 사출 성형의 유연성과 금속 부품의 강도 및 무결성을 결합합니다.
- 열간 등방성 프레스(HIP):다공성을 제거하고 부품의 기계적 특성을 개선하는 데 사용됩니다.
- 적층 제조:복잡한 형상과 맞춤형 부품을 고정밀로 생산할 수 있습니다.
- 스파크 플라즈마 소결(SPS):전기 펄스를 사용하여 분말을 가열하여 조밀하고 고강도 부품을 만드는 급속 소결 기술입니다.
요약하면 분말 야금은 금속 분말의 특성, 최종 부품의 기계적 요구 사항 및 사용되는 특정 기술의 영향을 받는 다각적인 공정입니다.고품질의 내구성 있는 부품을 생산하기 위해 올바른 재료와 공정을 선택하려면 이러한 요소를 이해하는 것이 필수적입니다.
요약 표:
측면 | 주요 세부 정보 |
---|---|
파우더 특성 | 유량, 밀도, 압축성, 강도는 부품 품질에 영향을 미칩니다. |
금속 선택 기준 | 내식성, 경도, 인장 강도, 충격 인성, 피로 강도. |
다양한 공정 | 기존, 사출 성형, 등방성 프레스, 적층 제조. |
소결 공정 | 온도 제어, 결합 메커니즘 및 최종 특성. |
고급 기술 | 금속 사출 성형, 열간 등방성 프레스, 적층 제조, SPS. |
분말 야금이 제조 공정을 개선하는 방법을 알아보세요. 지금 바로 문의하세요 전문가에게 문의하세요!