소결은 분말로 된 재료를 압축하고 가열하여 재료를 완전히 녹이지 않고 단단한 저다공성 구조를 형성하는 제조 공정입니다.이 방법은 세라믹, 금속 및 유리 생산에 널리 사용됩니다.이 공정에는 일반적으로 분말 준비, 압축, 입자 결합을 위한 가열, 재료 고형화를 위한 냉각 등의 단계가 포함됩니다.소결은 높은 강도와 내구성을 갖춘 복잡한 형상을 제작할 수 있는 능력으로 자동차, 항공우주, 전자 등의 산업에서 필수적인 기술로 평가받고 있습니다.
핵심 포인트 설명:
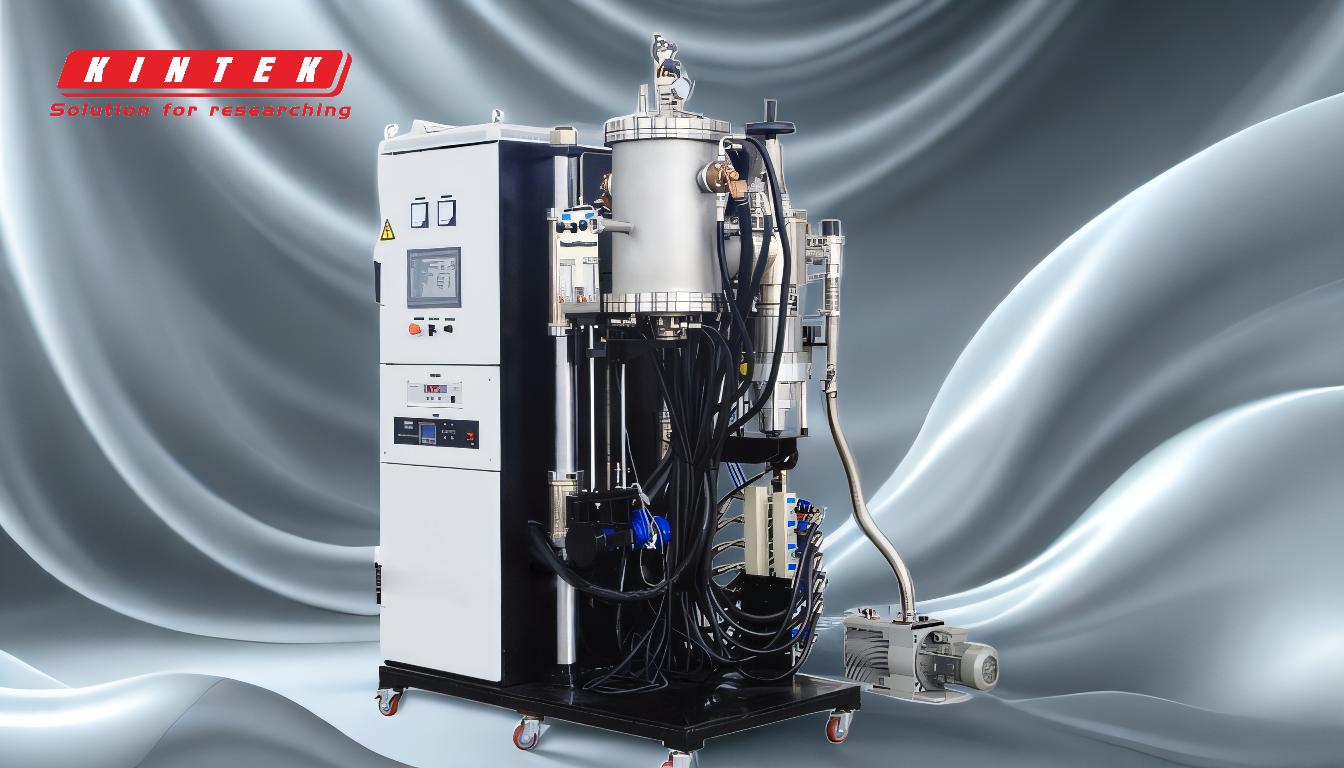
-
분말 준비:
- 이 공정은 분말 형태의 원료를 준비하는 것으로 시작됩니다.이러한 분말은 금속, 세라믹 또는 이 둘의 혼합물일 수 있으며, 결합력을 높이기 위해 결합제 또는 바인더와 같은 첨가제와 결합하는 경우가 많습니다.
- 예시:금속 소결에서는 철광석의 분말 철을 코크스와 혼합하고, 세라믹에서는 알루미나 또는 지르코니아 같은 특정 분말을 사용합니다.
-
압축:
- 분말화된 재료를 고압으로 원하는 모양으로 압축합니다.이 단계에서는 입자가 조밀하게 밀집되어 모양을 유지하는 '녹색 몸체'를 형성합니다.
- 필요한 형태를 얻기 위해 금형, 다이 또는 프레스 장비와 같은 도구가 사용됩니다.예를 들어 세라믹 제조에서는 보정된 분말을 눌러 일관된 모양을 만듭니다.
-
가열(소결):
- 압축된 재료는 일반적으로 소결로와 같은 통제된 환경에서 녹는점 바로 아래의 온도까지 가열됩니다.이 단계에서는 바인더나 윤활제와 같은 휘발성 성분을 제거하고 입자가 확산을 통해 결합할 수 있도록 합니다.
- 가열하는 동안 재료는 금속에 마르텐사이트 또는 결정 구조가 형성되거나 세라믹에 산화물이 환원되는 등 물리적 및 화학적 변화를 겪습니다.
- 예시:금속 소결에서는 용광로가 재료를 가열하여 입자 결합을 활성화하고, 세라믹에서는 고온으로 휘발성 성분을 제거하고 1차 재료를 융합합니다.
-
냉각 및 응고:
- 소결 후 재료는 서서히 냉각되어 균일하고 조밀한 구조로 응고됩니다.이 단계를 통해 최종 제품의 강도, 내구성 등 원하는 기계적 특성을 확보할 수 있습니다.
- 냉각 속도를 제어하여 재료의 성능에 영향을 미치는 특정 미세 구조를 달성할 수 있습니다.
-
후처리:
- 애플리케이션에 따라 소결 부품은 가공, 조립 또는 표면 처리와 같은 추가 단계를 거칠 수 있습니다.
- 예시:세라믹 제조에서 소결된 부품은 정밀한 치수를 얻기 위해 다이아몬드 공구 또는 초음파로 가공한 다음 조립을 위해 금속화 및 납땜을 하는 경우가 많습니다.
-
적용 분야 및 장점:
- 소결은 자동차 부품, 절삭 공구, 베어링, 전자 기판 등 다양한 제품을 생산하는 데 사용됩니다.
- 이 공정은 복잡한 형상을 만들 수 있고, 재료 활용도가 높으며, 대량 생산을 위한 비용 효율성이라는 장점을 제공합니다.
-
소결의 변형:
- 액상 소결(LPS):입자 결합 및 치밀화를 가속화하기 위해 소량의 액상을 도입합니다.
- 고체 소결:입자는 녹지 않고 확산과 입자 성장에 의존하여 결합합니다.
- 예시:금속 소결에서는 초경합금을 결합하는 데 LPS를 사용할 수 있으며, 세라믹에는 고체 소결이 일반적입니다.
이러한 단계를 통해 소결은 분말 재료를 최소한의 폐기물로 강력하고 내구성 있는 부품으로 변환하여 현대 제조의 초석이 됩니다.
요약 표:
단계 | 설명 | 예시 |
---|---|---|
분말 준비 | 원재료는 분말 형태로 준비되며 종종 첨가제가 첨가됩니다. | 금속 소결: 코크스와 혼합된 철 분말; 세라믹: 알루미나 또는 지르코니아. |
압축 | 분말을 고압으로 압축하여 '녹색 몸체'를 형성합니다. | 세라믹 제조: 보정된 분말을 모양에 맞게 압축합니다. |
가열(소결) | 재료를 녹는점 이하로 가열하여 확산을 통해 입자를 결합합니다. | 금속 소결: 용광로가 결합을 활성화하고 세라믹: 휘발성 물질을 제거합니다. |
냉각 | 점진적인 냉각은 재료를 조밀하고 통일된 구조로 고형화합니다. | 냉각 속도를 제어하여 특정 미세 구조를 구현합니다. |
후처리 | 최종 제품을 위한 가공 또는 표면 처리와 같은 추가 단계. | 세라믹: 다이아몬드 공구로 가공, 금속화 및 납땜. |
응용 분야 | 자동차, 항공우주, 전자 제품 등에 사용됩니다. | 절삭 공구, 베어링, 전자 기판. |
변형 | 액상 소결(LPS) 및 고체 소결. | 초경합금용 LPS, 세라믹용 고체 소결. |
소결로 제조 공정을 혁신하는 방법을 알아보세요. 지금 바로 전문가에게 문의하세요 !