열분해는 석유 산업에서 열을 가하여 큰 탄화수소 분자를 더 작고 가치 있는 분자로 분해하는 데 사용되는 공정입니다. 이 공정은 휘발유, 경유 및 기타 석유화학제품과 같은 가벼운 분획물을 생산하는 데 매우 중요합니다. 열분해 조건은 온도, 압력, 체류 시간, 공급 원료의 종류 등 여러 가지 요소의 영향을 받습니다. 이러한 조건을 이해하는 것은 공정을 최적화하고 원하는 제품 수율을 달성하는 데 필수적입니다. 아래에서는 열분해에 영향을 미치는 주요 요인과 이러한 요인이 어떻게 상호 작용하여 원하는 결과를 만들어내는지 살펴봅니다.
핵심 포인트 설명
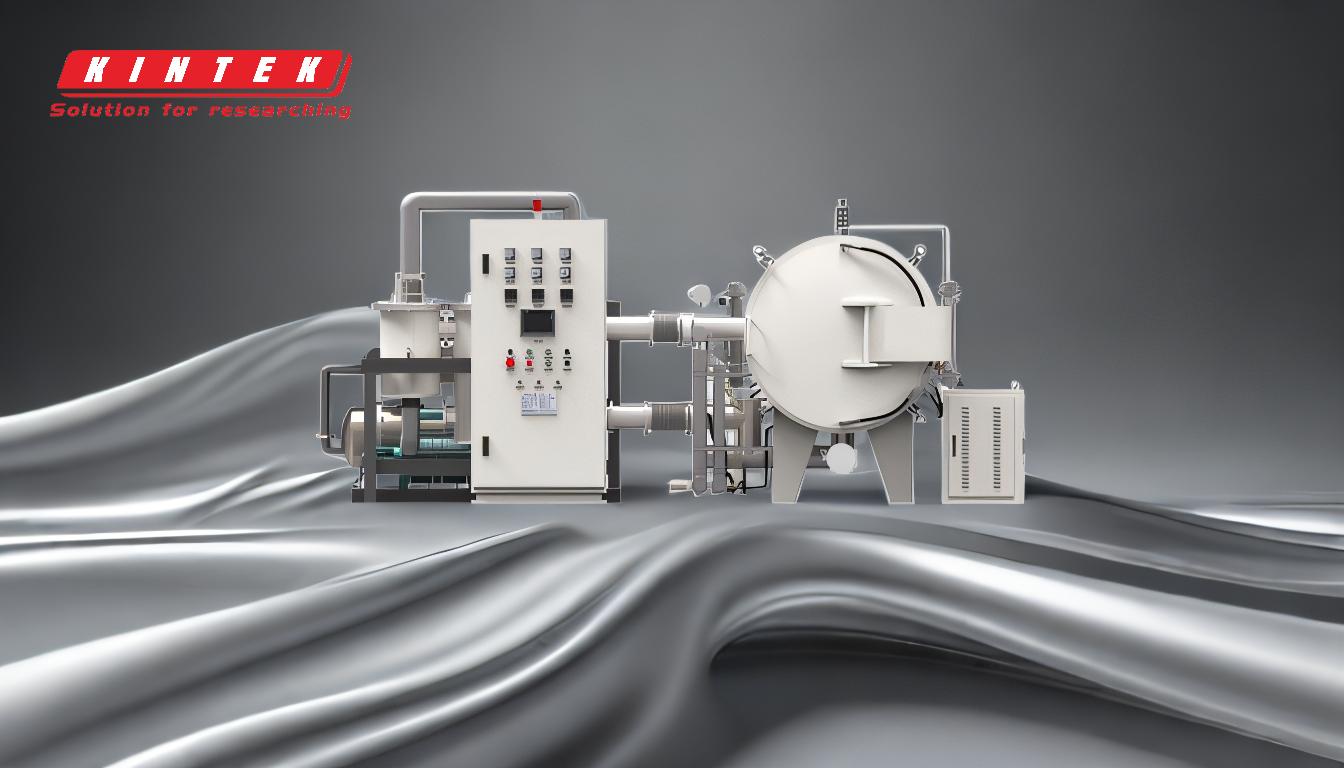
-
온도:
- 역할: 온도는 열분해에서 가장 중요한 요소 중 하나입니다. 온도가 높을수록 큰 탄화수소 분자의 화학 결합을 끊는 데 필요한 에너지가 제공됩니다.
- 최적 범위: 일반적으로 열분해는 450°C~750°C의 온도에서 발생합니다. 정확한 온도는 공급 원료의 종류와 원하는 제품에 따라 다릅니다.
- 영향: 일반적으로 온도가 높을수록 균열 속도가 빨라져 더 가벼운 탄화수소가 생산됩니다. 그러나 지나치게 높은 온도는 코킹(고체 탄소 침전물 형성)과 같은 원치 않는 부반응을 일으킬 수 있습니다.
-
압력:
- 역할: 압력은 탄화수소의 상과 분해 반응 속도에 영향을 미칩니다. 압력이 낮을수록 기체 생성물 형성에 유리하고 압력이 높을수록 액체 생성물이 더 많이 생성될 수 있습니다.
- 최적 범위: 열분해는 일반적으로 1~10기압의 낮은 압력에서 중간 정도의 압력에서 수행되는 경우가 많습니다. 압력의 선택은 원하는 제품 슬레이트와 사용되는 특정 크래킹 공정에 따라 달라집니다.
- 충격: 낮은 압력은 더 가벼운 탄화수소의 형성을 촉진할 수 있지만 코킹의 위험을 증가시킬 수도 있습니다. 압력이 높으면 코킹을 줄일 수 있지만 더 가벼운 제품의 수율이 감소할 수 있습니다.
-
체류 시간:
- 역할: 체류 시간은 원료가 크래킹 조건에 노출되는 시간을 의미합니다. 크랙의 정도와 제품의 분포를 제어하는 데 매우 중요합니다.
- 최적 범위: 체류 시간은 공정에 따라 몇 초에서 몇 분까지 매우 다양할 수 있습니다. 일반적으로 스팀 크래킹과 같은 공정에서는 체류 시간이 짧고, 지연 코킹에서는 체류 시간이 길어질 수 있습니다.
- 영향: 체류 시간이 길면 더 광범위한 크래킹이 가능하므로 더 가벼운 제품의 수율을 높일 수 있습니다. 그러나 체류 시간이 지나치게 길면 과도한 크래킹이 발생하여 원치 않는 부산물이 생성되고 코킹이 증가할 수 있습니다.
-
공급 원료 구성:
- 역할: 탄화수소 공급 원료의 유형은 크래킹 공정에 큰 영향을 미칩니다. 공급 원료마다 분자 구조가 다르기 때문에 크래킹 거동에 영향을 미칩니다.
- 공급 원료의 종류: 일반적인 공급 원료에는 나프타, 가스 오일 및 잔류물이 포함됩니다. 나프타와 같이 가벼운 원료는 더 쉽게 분해되고 더 많은 양의 가벼운 제품을 생산하는 반면, 잔류물과 같이 무거운 원료는 더 가혹한 조건이 필요하고 더 많은 부산물을 생성합니다.
- 영향: 공급 원료의 선택은 최적의 크래킹에 필요한 온도, 압력 및 체류 시간에 영향을 미칩니다. 공급 원료가 무거울수록 더 높은 온도와 더 긴 체류 시간이 필요할 수 있지만 코킹의 위험이 증가하고 더 복잡한 제품 슬레이트가 생성될 수 있습니다.
-
촉매(해당되는 경우):
- 역할: 전통적인 열분해는 촉매를 사용하지 않지만, 촉매 분해와 같은 일부 최신 공정에서는 촉매를 사용하여 분해 반응을 향상시킵니다.
- 영향: 촉매는 분해에 필요한 활성화 에너지를 낮춰 더 낮은 온도와 압력에서 공정을 진행할 수 있게 해줍니다. 이를 통해 크래킹 공정의 선택성을 개선하여 원하는 제품의 수율을 높이고 원치 않는 부산물을 줄일 수 있습니다.
-
반응기 설계:
- 역할: 열분해에 사용되는 반응기의 설계는 공정의 효율성과 효과에 영향을 미칠 수 있습니다. 반응기 설계는 열 전달, 혼합 및 체류 시간 분포에 영향을 미칩니다.
- 반응기의 종류: 일반적인 반응기 유형에는 관형 반응기, 유동층 반응기, 지연 코킹 드럼이 있습니다. 각 유형은 열 전달, 체류 시간 제어 및 작동 용이성 측면에서 장단점이 있습니다.
- 영향: 반응기 설계의 선택은 반응기 내의 온도 및 압력 프로파일에 영향을 미쳐 균열의 정도와 제품의 분포에 영향을 미칠 수 있습니다. 최적의 크래킹 조건을 달성하고 원치 않는 부반응을 최소화하려면 적절한 반응기 설계가 필수적입니다.
-
담금질:
- 역할: 담금질은 더 이상의 균열 반응을 막기 위해 균열된 제품을 빠르게 냉각하는 것입니다. 이는 최종 제품 유통을 제어하는 데 매우 중요합니다.
- 방법: 담금질은 물, 증기 또는 기타 냉각 매체를 사용하여 수행할 수 있습니다. 담금질 방법과 속도는 특정 공정과 원하는 제품 슬레이트에 따라 다릅니다.
- 영향: 효과적인 담금질은 과도한 균열과 원치 않는 부산물의 형성을 방지하여 원하는 제품 분포를 보존하는 데 도움이 됩니다. 또한 다운스트림 장비에서 코킹의 위험을 줄이는 데 도움이 됩니다.
요약하면 열분해 조건은 온도, 압력, 체류 시간, 공급 원료 구성 및 반응기 설계의 조합에 의해 결정됩니다. 이러한 각 요소는 크래킹 공정의 효율성과 최종 제품의 품질을 결정하는 데 중요한 역할을 합니다. 이러한 조건을 신중하게 제어함으로써 운영자는 원치 않는 부산물과 코킹과 같은 운영 문제를 최소화하면서 원하는 경질 탄화수소 혼합물을 생산하도록 크래킹 공정을 최적화할 수 있습니다.
요약 표:
요인 | 역할 | 최적 범위 | 영향 |
---|---|---|---|
온도 | 탄화수소 결합을 끊는 에너지 제공 | 450°C ~ 750°C | 온도가 높을수록 균열이 증가하지만 코킹이 발생할 수 있습니다. |
압력 | 크래킹 반응의 위상 및 속도에 영향을 미칩니다. | 1 ~ 10기압 | 압력이 낮을수록 가벼운 탄화수소에 유리하지만 코킹 위험이 증가할 수 있습니다. |
체류 시간 | 크랙의 정도 및 제품 분포 제어 | 초 ~ 분 | 시간이 길수록 수율은 높아지지만 과도한 균열이 발생할 위험이 있습니다. |
공급 원료 | 분자 구조에 따라 크래킹 거동에 영향을 미칩니다. | 나프타, 가스유, 잔류물 | 가벼운 공급 원료는 더 쉽게 분해되며, 무거운 공급 원료는 더 가혹한 조건이 필요합니다. |
반응기 설계 | 열 전달, 혼합 및 체류 시간 분포에 영향을 미칩니다. | 관형, 유동층, 지연 코킹 드럼 | 효율성 및 제품 분배에 영향 |
담금질 | 제품을 빠르게 냉각하여 추가 균열을 방지합니다. | 물, 증기 또는 기타 냉각 매체 | 제품 유통을 보존하고 코킹 위험 감소 |
전문가의 안내를 통해 열 크래킹 공정을 최적화하세요. 지금 문의하세요 !