열성형은 특히 소량 생산 시 사출 성형에 대한 비용 효율적인 대안입니다.경제성이 뛰어난 주된 이유는 툴링 비용이 현저히 낮기 때문입니다.열성형 금형은 일반적으로 다음과 같은 저렴한 재료로 제작됩니다. 알루미나 세라믹 사출 성형에 필요한 경화강 금형에 비해 제조가 더 쉽고 저렴합니다.또한 열성형 금형의 설계 및 생산 공정이 간단하기 때문에 초기 투자와 리드 타임이 모두 줄어들어 특정 애플리케이션에 더 경제적인 선택이 될 수 있습니다.
핵심 포인트 설명:
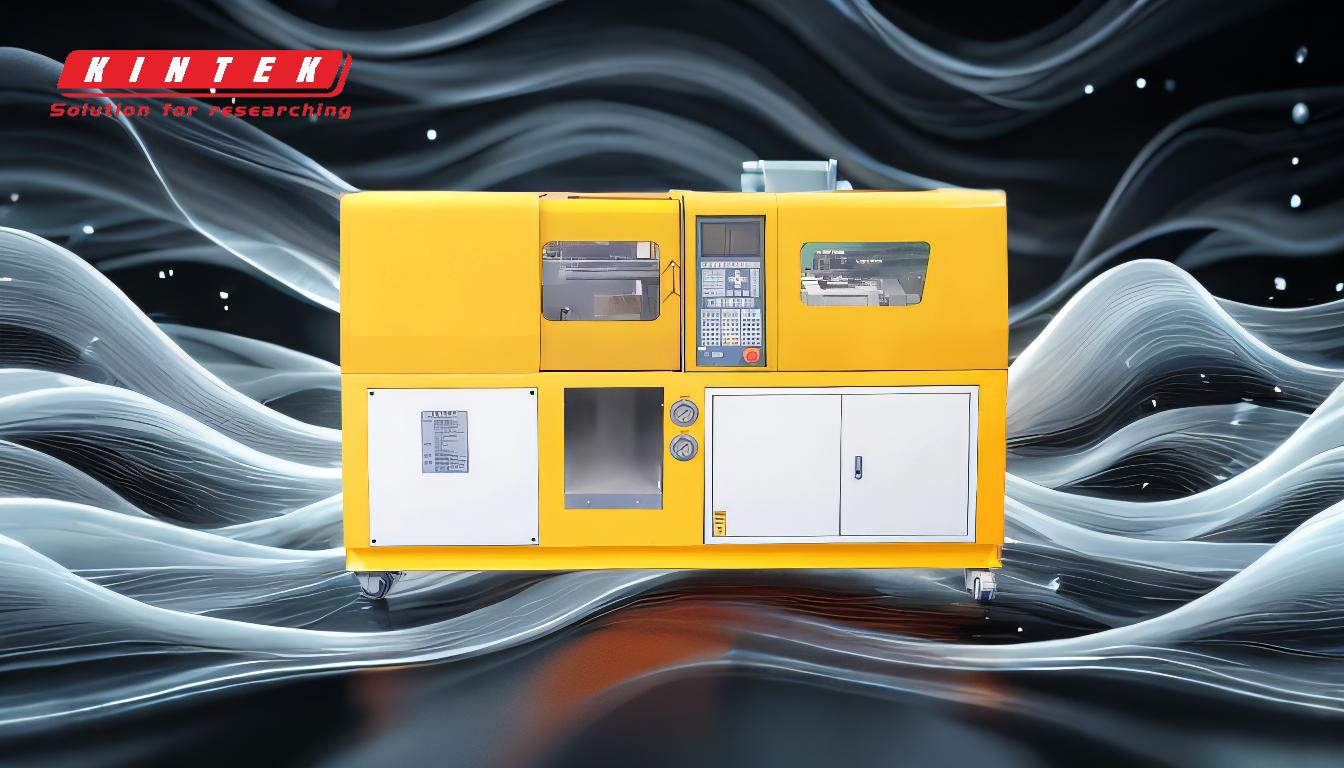
-
툴링 비용 절감:
- 재료비:열성형 금형은 사출 성형에 사용되는 경화강보다 가격이 저렴한 알루미늄으로 제작되는 경우가 많습니다.알루미늄은 가공하기 쉽고 생산에 필요한 시간과 노동력이 적어 비용을 더욱 절감할 수 있습니다.
- 디자인 복잡성:열성형 금형은 일반적으로 사출 성형 금형에 비해 설계가 더 간단합니다.이러한 단순성은 설계 및 제조 비용 절감으로 이어집니다.
-
초기 투자 비용 절감:
- 금형 생산 시간:열성형 금형 제작에 필요한 시간은 사출 성형 금형보다 훨씬 짧습니다.이렇게 빠른 처리 시간은 특히 마감 기한이 촉박한 프로젝트의 경우 비용 절감으로 이어질 수 있습니다.
- 설정 비용:열성형 초기 설정은 덜 복잡하고 비용이 적게 듭니다.여기에는 기계 비용이 포함되며, 일반적으로 사출 성형기에 비해 열성형 장비의 가격이 더 저렴합니다.
-
소량 생산에 경제성:
- 볼륨 유연성:열성형 성형은 특히 소량 생산에 비용 효율적입니다.툴링에 대한 초기 투자 비용이 낮기 때문에 대량 생산이 필요하지 않은 회사에서 실행 가능한 옵션입니다.
- 프로토타이핑:프로토타이핑 또는 단기 생산의 경우 열성형 성형이 더 경제적인 솔루션을 제공합니다.빠르고 저렴하게 금형을 제작할 수 있으므로 설계를 더 빠르게 반복하고 테스트할 수 있습니다.
-
재료 효율성:
- 폐기물 감소:열성형은 특히 대형 부품의 경우 재료 효율성이 더 높을 수 있습니다.이 공정은 사출 성형에 비해 폐자재 발생이 적어 원자재 비용을 절감할 수 있습니다.
- 더 얇은 벽:열성형 부품은 종종 더 얇은 벽으로 제작할 수 있으므로 강도나 기능의 저하 없이 재료 사용량을 줄일 수 있습니다.
-
운영 비용:
- 에너지 소비량:열성형은 일반적으로 사출 성형에 비해 에너지 소비가 적습니다.에너지 소비량이 적기 때문에 특히 대규모 작업에서 전반적인 비용 절감에 기여합니다.
- 유지보수:열성형 장비의 유지보수 비용은 일반적으로 더 낮습니다.기계가 단순하고 금형의 마모가 적기 때문에 시간이 지남에 따라 유지보수 비용이 절감됩니다.
요약하면, 열성형은 특히 소량 생산, 시제품 제작 및 재료 효율성과 초기 투자 감소가 중요한 응용 분야에서 사출 성형보다 더 경제적인 대안을 제공합니다.낮은 툴링 비용, 더 간단한 설계, 더 빠른 생산 시간으로 인해 많은 제조업체가 열성형 성형을 비용 효율적인 선택으로 여기고 있습니다.
요약 표:
측면 | 열성형 | 사출 성형 |
---|---|---|
툴링 비용 | 낮음(알루미늄 몰드) | 더 높음(경화 강철 금형) |
초기 투자 비용 | 감소(더 간단한 설정, 더 저렴한 기계) | 높음(복잡한 설정, 고가의 기계) |
생산 시간 | 더 빠름(금형 제작 시간 단축) | 느림(더 긴 금형 제작 시간) |
대량 생산 적합성 | 소량 생산 및 프로토타입 제작에 이상적 | 대량 생산에 적합 |
재료 효율성 | 높음(폐기물이 적고 벽이 얇음) | 낮음(폐기물 증가, 벽 두께 증가) |
운영 비용 | 낮음(에너지 소비 감소, 유지보수 감소) | 높음(에너지 소비 증가, 유지보수 증가) |
비용 효율적인 열성형 솔루션에 관심이 있으신가요? 지금 바로 문의하세요. 에 문의하여 자세히 알아보세요!