CVD(화학 기상 증착)와 PVD(물리 기상 증착)는 절삭 공구에 널리 사용되는 두 가지 코팅 기술로, 각각 고유한 특성과 용도를 가지고 있습니다.두 방법 모두 기판에 얇고 내구성 있는 층을 증착하여 공구 성능을 향상시키는 것을 목표로 하지만 공정, 코팅 특성 및 특정 가공 작업에 대한 적합성에서 큰 차이가 있습니다.PVD는 고체 재료를 기화하여 기판에 증착하는 방식으로, 더 얇고 매끄러운 코팅과 날카로운 모서리로 정밀 마감 작업에 이상적입니다.반면 CVD는 화학적으로 반응하여 더 두껍고 거친 코팅을 형성하는 기체 전구체를 사용하여 우수한 열 차단 특성과 내마모성을 제공하므로 황삭 및 연속 절단 작업에 더 적합합니다.이러한 차이점을 이해하는 것은 가공 요구 사항과 가공되는 재료에 따라 적합한 코팅 방법을 선택하는 데 매우 중요합니다.
핵심 사항을 설명합니다:
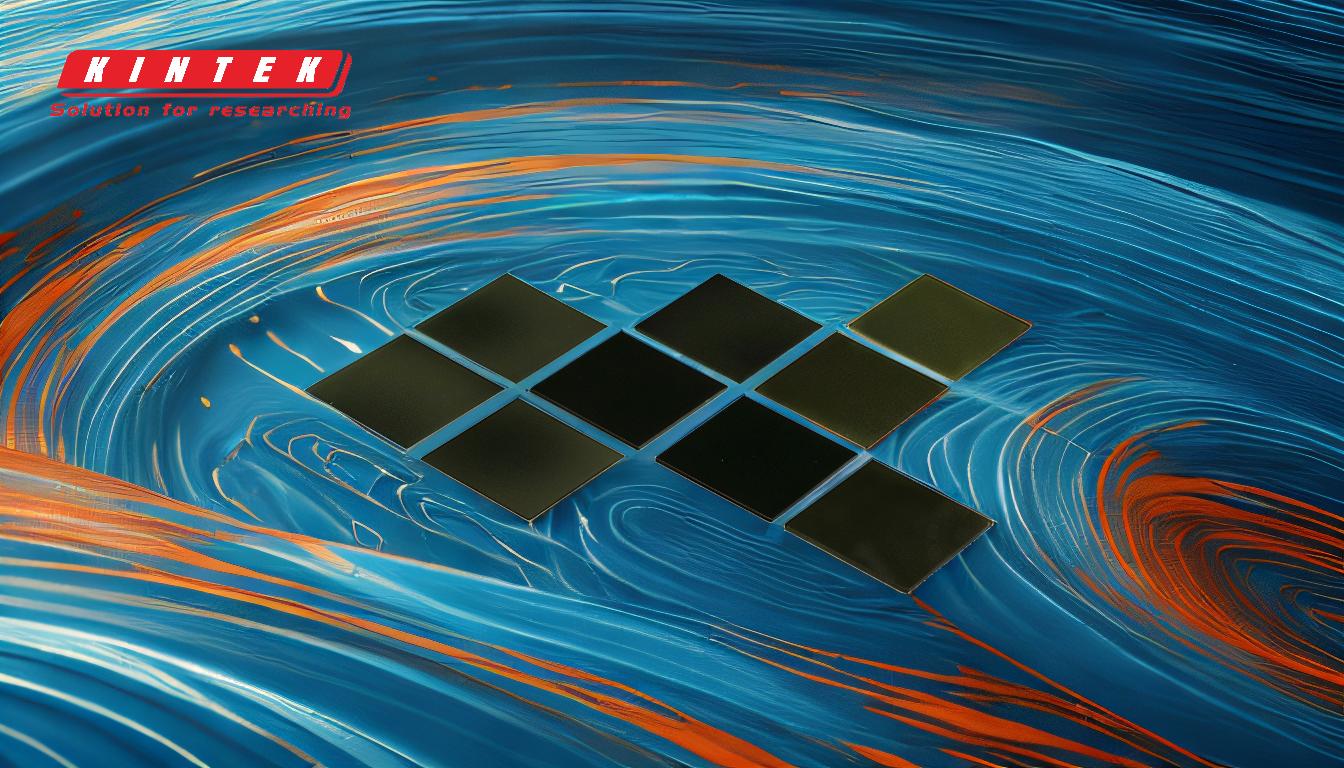
-
프로세스 차이점:
-
PVD:
- 아크 방전 또는 스퍼터링과 같은 물리적 방법을 사용하여 고체 물질(타겟)을 기화시킵니다.
- 기화된 원자는 기판에 응축되어 얇고 매끄러운 코팅을 형성합니다.
- 비교적 낮은 온도(250°C ~ 450°C)에서 작동하므로 열에 민감한 소재에 적합합니다.
-
CVD:
- 고온(450°C~1050°C)에서 화학적으로 반응하는 기체 전구체를 사용하여 고체 코팅을 증착합니다.
- 화학 반응은 PVD에 비해 더 두껍고 거친 코팅을 생성합니다.
- 더 높은 온도가 필요하므로 열에 민감한 기판에는 사용이 제한될 수 있습니다.
-
PVD:
-
코팅 속성:
-
PVD:
- 표면이 매끄러운 얇은 코팅(3~5μm)을 생성하여 절삭날이 더 날카로워집니다.
- 냉각 중에 압축 응력을 형성하여 내구성과 균열에 대한 저항력을 향상시킵니다.
- 공구 모서리에 잦은 충격이 발생하는 밀링과 같은 중단 절삭 공정에 이상적입니다.
-
CVD:
- 거친 표면으로 더 두꺼운 코팅(10~20μm)을 생성하여 더 나은 단열 및 내마모성을 제공합니다.
- 공구가 지속적인 열과 마찰에 노출되는 선삭과 같은 연속 절삭 작업에 적합합니다.
-
PVD:
-
가공 분야 적용 분야:
-
PVD:
- 밀링, 드릴링, 나사 가공 등 정밀하고 날카로운 모서리가 필요한 마감 작업에 가장 적합합니다.
- 일반적으로 스테인리스 스틸, 티타늄 및 열처리 합금과 같은 소재 가공에 사용됩니다.
-
CVD:
- 선삭 및 보링과 같은 황삭 및 고강도 절삭 작업에 더욱 효과적입니다.
- 주철, 탄소강 및 고온 합금과 같은 소재 가공에 선호됩니다.
-
PVD:
-
환경 및 운영 고려 사항:
-
PVD:
- 화학 반응을 일으키거나 유해한 부산물을 생성하지 않아 환경 친화적입니다.
- 처리 온도가 낮아 에너지 소비를 줄이고 기판 왜곡을 최소화합니다.
-
CVD:
- 오염 물질을 생성할 수 있는 화학 반응을 수반하므로 적절한 폐기물 관리가 필요합니다.
- 온도가 높으면 기판이 변형되어 특정 재료에 사용이 제한될 수 있습니다.
-
PVD:
-
장점과 한계:
-
PVD:
- 장점:얇고 선명한 코팅, 낮은 처리 온도, 환경 친화적.
- 한계:코팅 두께가 제한적이며 열 차단 효과가 떨어집니다.
-
CVD:
- 장점:더 두껍고 내구성이 뛰어난 코팅, 뛰어난 내열성 및 내마모성.
- 한계:더 높은 가공 온도, 잠재적인 환경 영향.
-
PVD:
이러한 주요 차이점을 이해함으로써 구매자와 엔지니어는 특정 가공 요구 사항, 재료 특성 및 원하는 결과에 따라 PVD 또는 CVD 코팅 절삭 공구를 사용할지 여부에 대해 정보에 입각한 결정을 내릴 수 있습니다.
요약 표:
측면 | PVD | CVD |
---|---|---|
프로세스 | 고체 물질 기화, 저온(250°C-450°C) | 기체 전구체 사용, 고온(450°C-1050°C) |
코팅 두께 | 얇음(3~5μm), 매끄러운 표면 | 두꺼운(10~20μm), 거친 표면 |
코팅 특성 | 날카로운 모서리, 압축 응력, 내구성 | 우수한 열 차단, 내마모성 |
응용 분야 | 마감 작업(밀링, 드릴링, 스레딩) | 황삭 및 고강도 절삭(선삭, 보링) |
재료 | 스테인리스 스틸, 티타늄, 열처리 합금 | 주철, 탄소강, 고온 합금 |
환경 영향 | 환경 친화적, 유해한 부산물 없음 | 잠재적 오염 물질, 폐기물 관리 필요 |
장점 | 선명한 코팅, 낮은 가공 온도, 친환경적 | 내구성 있는 코팅, 우수한 내열성 및 내마모성 |
제한 사항 | 제한된 두께, 열 차단 효과 저하 | 높은 가공 온도, 기판 변형 가능성 |
절삭 공구에 적합한 코팅을 선택하는 데 도움이 필요하신가요? 지금 바로 전문가에게 문의하세요. !