브레이징 용접은 모재 자체를 녹이지 않고 필러 금속을 녹여 두 개 이상의 모재를 접합하는 다용도 접합 공정입니다.이 방법은 왜곡을 최소화하면서 튼튼하고 내구성 있는 접합부를 만들 수 있기 때문에 다양한 산업 분야에서 널리 사용됩니다.접합되는 재료, 원하는 접합 특성 및 특정 적용 요건에 따라 다양한 유형의 브레이징 용접 기술이 사용됩니다.이 글에서는 다양한 유형의 브레이징 용접을 고유한 특성, 장점 및 적용 분야에 초점을 맞춰 살펴봅니다.
핵심 포인트 설명:
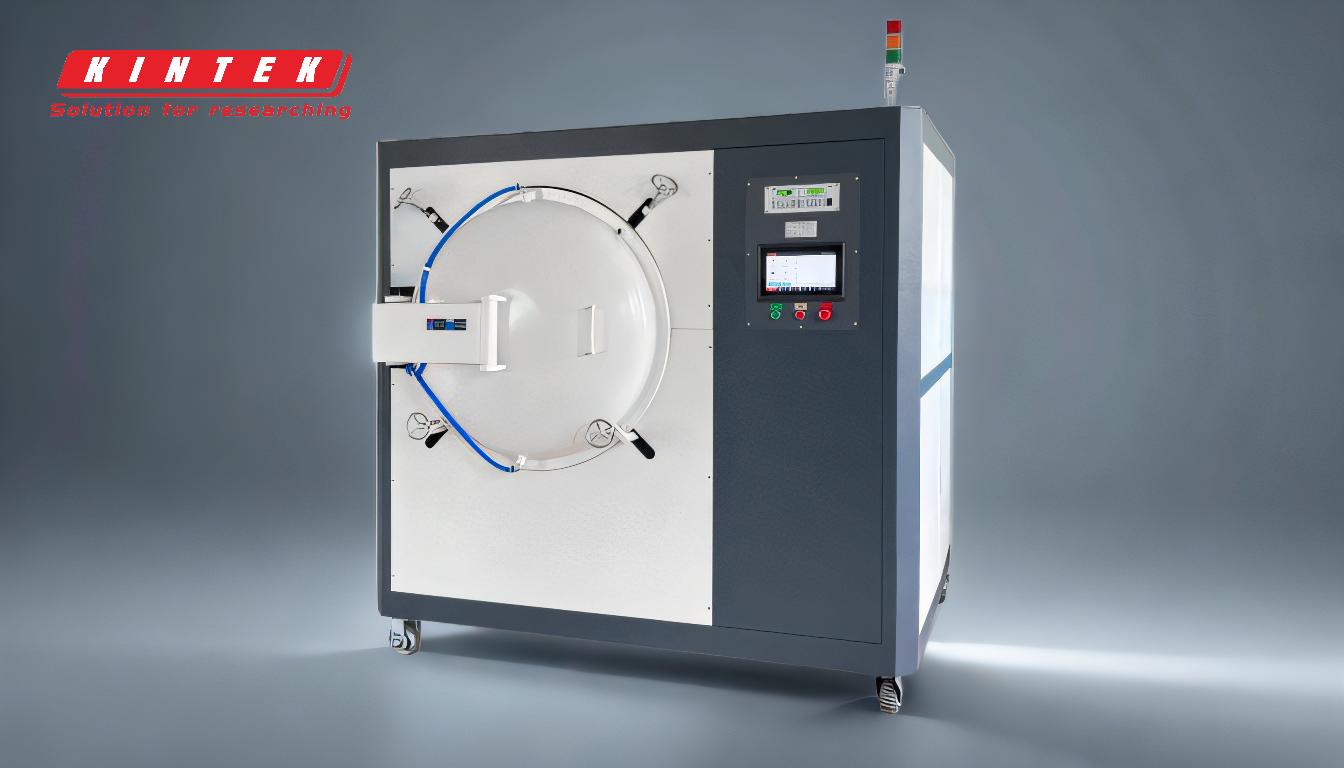
-
TIG 브레이징:
- 프로세스:TIG(텅스텐 불활성 가스) 브레이징은 텅스텐 전극을 사용하여 공작물을 가열하는 전기 아크를 생성합니다.이 공정은 기존 용접에 비해 낮은 암페어에서 작동하므로 특히 주철과 같은 재료로 작업할 때 기본 재료의 용융을 방지하는 데 도움이 됩니다.
- 차폐 가스:아르곤 가스는 대기 오염으로부터 납땜 영역을 보호하는 데 사용되므로 플럭스가 필요하지 않습니다.따라서 공정이 더 깨끗해지고 납땜 후 세척 요구 사항이 줄어듭니다.
- 애플리케이션:TIG 브레이징은 얇은 재료의 접합, 주철 부품 수리 및 정밀한 열 제어가 필요한 응용 분야에 특히 유용합니다.
-
산소 연료 브레이징:
- 프로세스:이 방법은 아세틸렌과 같은 연료 가스를 산소와 함께 연소시켜 생성된 불꽃을 사용하여 모재를 가열하고 필러 금속을 용융시킵니다.불꽃은 집중된 열원을 제공하므로 국소 가열이 가능합니다.
- 플럭스 요구 사항:TIG 브레이징과 달리 산소 연료 브레이징은 일반적으로 산화를 방지하고 필러 금속의 흐름을 원활하게 하기 위해 플럭스를 사용해야 합니다.플럭스는 가열하기 전에 접합 부위에 도포해야 합니다.
- 적용 분야:산소 연료 브레이징은 일반적으로 구리 파이프, HVAC 시스템 및 강력하고 누출 방지 조인트가 필요한 기타 애플리케이션의 접합에 사용됩니다.
-
용광로 브레이징:
- 프로세스:퍼니스 브레이징은 조립된 부품과 필러 금속을 퍼니스에 넣고 전체 어셈블리를 브레이징 온도까지 가열하는 작업입니다.퍼니스는 균일한 가열을 제공하며, 이는 일관된 조인트 품질을 달성하는 데 필수적입니다.
- 분위기 제어:불활성 가스 또는 진공 상태를 사용하여 산화를 방지하기 위해 용광로 분위기를 제어할 수 있습니다.따라서 플럭스가 필요하지 않으며 깨끗하고 고품질의 조인트를 얻을 수 있습니다.
- 애플리케이션:용광로 브레이징은 높은 정밀도와 반복성이 요구되는 자동차 부품, 항공우주 부품, 전자 어셈블리 등 부품의 대량 생산에 이상적입니다.
-
인덕션 브레이징:
- 프로세스:인덕션 브레이징은 전자기 유도를 사용하여 공작물 내에서 열을 발생시킵니다.유도 코일을 접합부 근처에 배치하고 코일을 통해 교류 전류를 통과시켜 공작물에 와전류를 유도하여 열을 발생시킵니다.
- 장점:이 방법은 빠른 가열과 열 적용을 정밀하게 제어할 수 있어 고속 생산 및 국소 가열에 적합합니다.
- 응용 분야:유도 납땜은 전기 산업에서 구리 및 알루미늄 부품을 결합하는 데 일반적으로 사용되며, 의료 기기 및 보석류 생산에도 사용됩니다.
-
딥 브레이징:
- 프로세스:딥 브레이징에서는 조립된 부품을 용융 소금 용액 또는 용융 필러 금속 용액에 담급니다.용해조에서 나오는 열이 용가재를 녹여 모세관 작용에 의해 접합부로 흘러들어갑니다.
- 플럭스 사용량:용융 소금 욕조를 사용하면 소금이 열원 및 플럭스 역할을 모두 수행하므로 추가 플럭스 적용이 필요하지 않습니다.
- 응용 분야:딥 브레이징은 특히 항공우주 및 자동차 산업에서 알루미늄 및 기타 비철 금속을 접합하는 데 자주 사용됩니다.
-
저항 브레이징:
- 프로세스:저항 납땜은 접합 부위에 전류를 통과시켜 재료의 전기 저항으로 인해 열을 발생시키는 방식입니다.이 열은 필러 금속을 녹여 접합부로 흐르게 합니다.
- 장점:이 방법을 사용하면 열 적용을 정밀하게 제어할 수 있으며 작고 섬세한 부품을 결합하는 데 적합합니다.
- 응용 분야:저항 브레이징은 전자 산업에서 커넥터, 단자 및 기타 소형 부품을 결합하는 데 일반적으로 사용됩니다.
-
레이저 브레이징:
- 프로세스:레이저 브레이징은 집중된 레이저 빔을 사용하여 접합 부위를 가열하고 필러 금속을 녹입니다.레이저는 고도로 집중된 열원을 제공하므로 브레이징 공정을 정밀하게 제어할 수 있습니다.
- 장점:레이저 브레이징은 높은 정밀도, 최소한의 열 영향 영역, 이종 재료를 접합할 수 있는 기능을 제공합니다.
- 응용 분야:이 방법은 자동차 산업에서 차체 패널을 결합하는 데 사용되며, 의료 및 전자 산업에서 작고 복잡한 부품을 결합하는 데 사용됩니다.
브레이징 용접의 각 유형에는 고유한 장점이 있으며 특정 용도에 적합합니다.브레이징 방법의 선택은 접합되는 재료, 필요한 접합 특성, 생산량 및 특정 애플리케이션 요구 사항과 같은 요인에 따라 달라집니다.다양한 유형의 브레이징 용접을 이해하면 다양한 산업 분야에서 고품질의 내구성 있는 접합을 달성하는 데 가장 적합한 방법을 선택할 수 있습니다.
요약 표:
브레이징 유형 | 주요 특성 | 애플리케이션 |
---|---|---|
TIG 브레이징 | 아르곤 가스 사용, 플럭스 필요 없음 | 얇은 재료, 주철 수리 |
산소 연료 브레이징 | 플럭스, 국소 가열 필요 | 구리 파이프, HVAC 시스템 |
용광로 브레이징 | 균일한 가열, 제어된 분위기 | 자동차, 항공우주, 전자 |
인덕션 브레이징 | 빠른 가열, 정밀한 제어 | 전기, 의료 기기, 보석류 |
딥 브레이징 | 용융 염 또는 필러 금속 용해조 사용 | 알루미늄, 항공우주, 자동차 |
저항 브레이징 | 전류 가열 조인트 | 전자, 커넥터, 단자 |
레이저 브레이징 | 고정밀, 최소한의 열 영향 영역 | 자동차 차체 패널, 의료 기기 |
프로젝트에 적합한 납땜 방법을 선택하는 데 도움이 필요하신가요? 지금 바로 전문가에게 문의하세요. 전문가에게 문의하세요!