PVD(물리적 기상 증착)와 CVD(화학적 기상 증착)는 기판에 박막 코팅을 적용하는 데 널리 사용되는 두 가지 기술입니다. 두 방법 모두 표면 특성을 향상시키는 것을 목표로 하지만 메커니즘, 작동 조건 및 결과적인 코팅 특성이 크게 다릅니다. PVD는 일반적으로 진공 조건에서 고체 소스에서 기판으로 재료를 물리적으로 전달하는 반면, CVD는 코팅을 형성하기 위해 기체 전구체와 기판 사이의 화학 반응에 의존합니다. 이러한 차이는 코팅 두께, 균일성, 온도 요구 사항 및 재료 호환성과 같은 요소에 영향을 미칩니다.
설명된 핵심 사항:
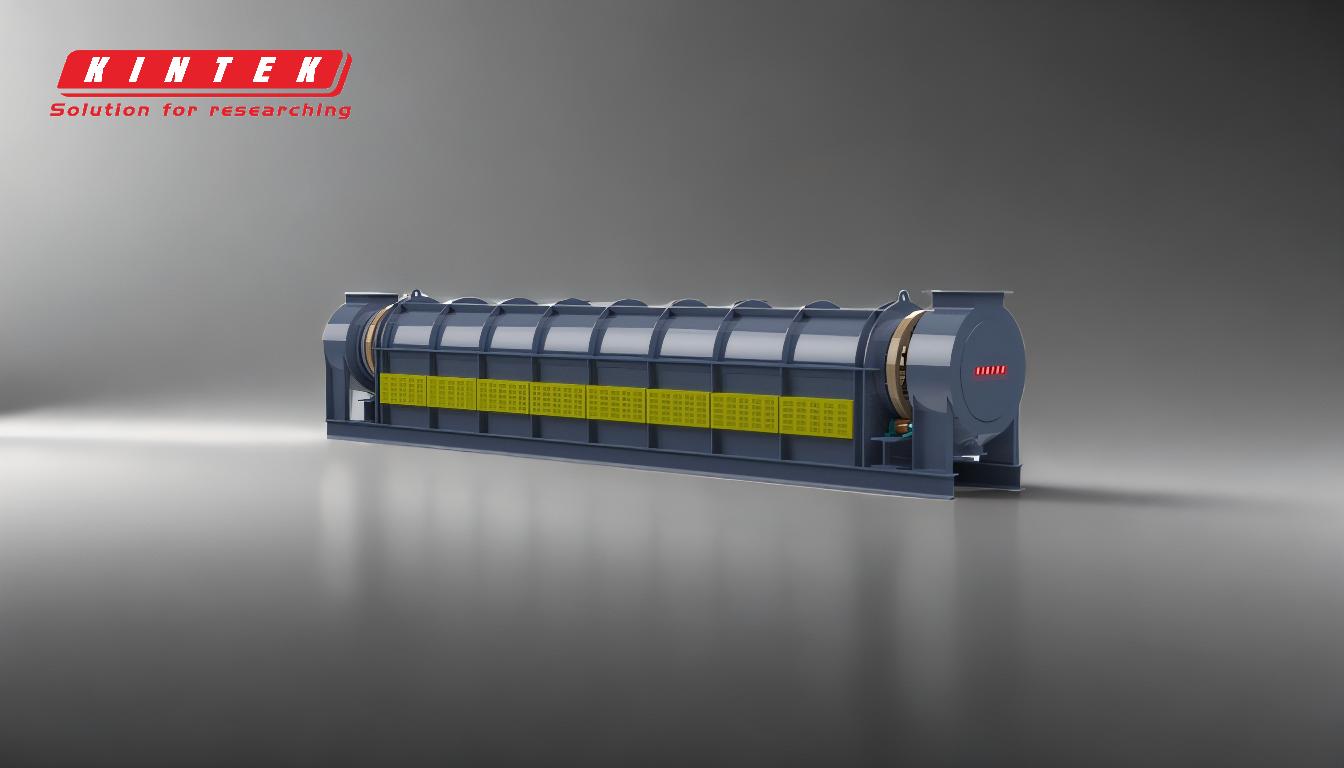
-
증착 메커니즘:
- PVD: PVD는 재료가 고체 타겟에서 물리적으로 기화되어 기판에 증착되는 가시선 공정입니다. 이 공정에는 타겟 물질과 기판 사이의 화학 반응이 포함되지 않습니다. 대신 원자나 분자가 타겟에서 방출되어 기판 표면에 응축됩니다.
- CVD: CVD는 기체 전구체와 기판 사이의 화학 반응을 포함합니다. 가스는 기판 표면에서 반응하여 고체 코팅을 형성합니다. 이 공정은 다방향으로 진행됩니다. 즉, 코팅이 복잡한 기하학적 구조와 숨겨진 영역을 덮을 수 있다는 의미입니다.
-
작동 온도:
- PVD: PVD는 일반적으로 250°C~500°C 범위의 낮은 온도에서 작동합니다. 이는 고온을 견딜 수 없는 기판에 적합합니다.
- CVD: CVD에는 훨씬 더 높은 온도가 필요하며, 종종 450°C에서 1050°C 사이입니다. 코팅을 형성하는 화학 반응을 촉진하려면 고온이 필요합니다. 그러나 이로 인해 온도에 민감한 재료의 사용이 제한됩니다.
-
코팅 두께 및 균일성:
- PVD: PVD 코팅은 일반적으로 공정의 가시선 특성으로 인해 더 얇고(3~5μm) 균일성이 떨어집니다. 그러나 적용 속도가 더 빠르고 초경질 필름을 얻을 수 있습니다.
- CVD: CVD 코팅은 화학 반응을 통해 더 두꺼워지고(10~20μm) 더 균일해지며 복잡한 형상도 더 잘 덮을 수 있습니다. 이 공정은 더 느리지만 더 조밀한 코팅을 생성합니다.
-
재료 호환성:
- PVD: PVD는 금속, 합금, 세라믹 등 다양한 재료를 증착할 수 있습니다. 이러한 다양성으로 인해 다양한 응용 분야에 적합합니다.
- CVD: CVD는 관련된 화학 반응의 특성으로 인해 일반적으로 세라믹과 폴리머로 제한됩니다. 재료 호환성 측면에서 다용도가 떨어집니다.
-
응력 및 표면 특성:
- PVD: PVD 코팅은 종종 압축 응력을 나타내므로 코팅의 내구성과 접착력을 향상시킬 수 있습니다. 이 과정을 통해 표면도 더욱 부드러워집니다.
- CVD: CVD 코팅은 높은 가공 온도로 인해 인장 응력이 발생하여 미세한 균열이 발생할 수 있습니다. 코팅은 밀도가 더 높지만 부드러움을 얻으려면 후처리가 필요할 수 있습니다.
-
응용:
- PVD: PVD는 절삭 공구, 장식 마감재, 내마모성 표면 등 얇고 단단한 코팅이 필요한 용도에 일반적으로 사용됩니다.
- CVD: CVD는 반도체 제조, 보호 코팅, 고온 부품 등 두껍고 균일한 코팅이 필요한 응용 분야에 선호됩니다.
이러한 주요 차이점을 이해함으로써 구매자와 엔지니어는 재료 호환성, 코팅 두께 및 작동 조건과 같은 특정 요구 사항에 따라 적절한 증착 기술을 선택할 수 있습니다.
요약표:
측면 | PVD | CVD |
---|---|---|
증착 메커니즘 | 고체 소스(가시선)에서 물질을 물리적으로 전달합니다. | 기체 전구체와 기판 사이의 화학 반응. |
작동 온도 | 250°C ~ 500°C(낮은 온도). | 450°C ~ 1050°C(더 높은 온도). |
코팅 두께 | 더 얇아지고(3~5μm) 균일성이 떨어집니다. | 더 두껍고(10~20μm) 더 균일합니다. |
재료 호환성 | 금속, 합금, 세라믹(다용도). | 세라믹 및 폴리머(다용성이 제한됨) |
응력과 표면 | 압축 응력, 매끄러운 표면. | 인장 응력, 밀도가 높은 코팅에는 후처리가 필요할 수 있습니다. |
응용 | 절단 도구, 장식 마감재, 내마모성 표면. | 반도체 제조, 보호 코팅, 고온 부품. |
PVD와 CVD 중에서 선택하는 데 도움이 필요하십니까? 지금 전문가에게 문의하세요 맞춤형 조언을 위해!