사출 금형에 사용되는 플레이트의 수는 금형의 설계와 복잡성에 따라 달라집니다.일반적으로 몰드는 2판 또는 3판 몰드로 설계됩니다.2판 몰드는 더 간단하며 코어용과 캐비티용의 두 개의 메인 플레이트로 구성됩니다.이 몰드는 일반적으로 간단한 부품에 사용되며 설정 시간이 짧습니다.반면 3판 몰드는 추가 플레이트가 포함되어 있어 더 복잡한 부품 설계와 자동화된 부품 배출이 가능합니다.2판 금형과 3판 금형 중 어떤 것을 선택할지는 부품 형상, 생산 요구 사항, 비용 고려 사항에 따라 달라집니다.
핵심 사항을 설명합니다:
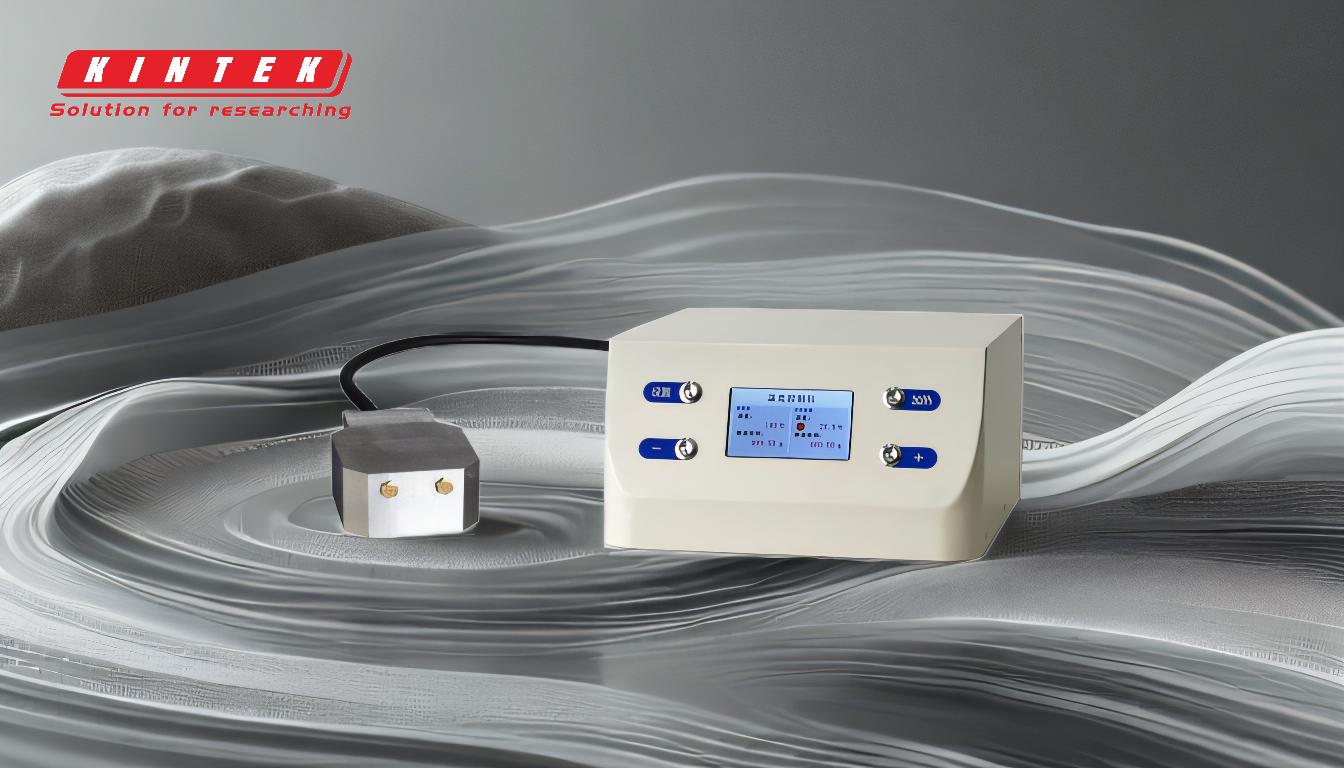
-
투 플레이트 몰드:
- 구조:코어용과 캐비티용 두 개의 메인 플레이트로 구성되어 있습니다.
- 사용법:간단한 형상을 가진 단순한 부품에 이상적입니다.
-
장점:
- 설계 및 제조가 더 쉬움.
- 부품 수가 적어 비용 절감.
- 더 빠른 설정과 더 짧은 생산 주기.
- 단점:복잡한 부품 설계 또는 자동화된 배출 시스템을 위한 유연성 제한.
-
3판 금형:
- 구조:추가 플레이트가 포함되어 있어 3 플레이트 시스템입니다.
- 사용법:다중 게이팅 또는 자동 배출이 필요한 복잡한 부품에 적합합니다.
-
장점:
- 부품 설계의 유연성 향상.
- 여러 게이팅 포인트를 허용하여 부품 품질을 개선합니다.
- 자동화된 부품 배출을 지원하여 수작업을 줄입니다.
-
단점:
- 더 복잡한 설계 및 제조 공정.
- 추가 구성 요소로 인한 비용 증가.
- 설정 시간 및 생산 주기가 더 길어집니다.
-
선택에 영향을 미치는 요인:
- 부품 복잡성:복잡한 형상이나 여러 피처가 있는 복잡한 부품에는 3판 금형이 필요할 수 있습니다.
- 생산량:대량 생산에는 2판 금형의 효율성이 유리할 수 있지만, 소량 또는 맞춤형 부품에는 3판 금형의 유연성이 필요할 수 있습니다.
- 비용 고려 사항:일반적으로 2판 몰드가 더 비용 효율적이지만, 3판 몰드의 추가 기능으로 인해 특정 애플리케이션의 경우 더 높은 비용이 발생할 수 있습니다.
- 사이클 시간:2판 금형은 일반적으로 사이클 시간이 짧아 고속 생산에 더 적합합니다.
-
실용적인 고려 사항:
- 툴링 및 유지보수:3판 금형에는 보다 정교한 툴링과 유지보수가 필요하므로 장기적인 운영 비용에 영향을 미칠 수 있습니다.
- 재료 흐름:몰드 플레이트의 디자인은 용융 플라스틱의 흐름에 영향을 미쳐 부품 품질과 일관성에 영향을 미칩니다.
- 이젝션 메커니즘:3판 금형에는 자동화된 배출 시스템이 포함되는 경우가 많으며, 이는 생산 효율성을 향상시킬 수 있지만 금형의 복잡성을 증가시킵니다.
이러한 핵심 사항을 이해하면 구매자는 프로젝트의 특정 요구 사항에 따라 2판 금형 또는 3판 금형을 선택할지 여부를 정보에 입각하여 결정할 수 있습니다.
요약 표:
기능 | 2판 몰드 | 3판 몰드 |
---|---|---|
구조 | 2개의 메인 플레이트(코어 및 캐비티) | 플레이트 3개(추가 플레이트 포함) |
사용법 | 단순한 설계의 간단한 부품 | 다중 게이팅이 있는 복잡한 부품 |
장점 | 더 쉬운 설계, 더 낮은 비용, 더 빠른 설정 | 유연성 향상, 자동 배출 |
단점 | 복잡한 디자인에 대한 제한된 유연성 | 더 높은 비용, 더 긴 설정 시간 |
이상적인 대상 | 대용량, 단순한 지오메트리 | 소량, 복잡한 형상 |
프로젝트에 어떤 금형이 적합한지 아직 잘 모르시겠어요? 지금 바로 전문가에게 문의하세요. 전문가에게 문의하세요!