PVD(물리적 기상 증착)와 CVD(화학 기상 증착)는 다양한 산업에서 사용되는 대표적인 박막 증착 기술로, 각각 고유한 특징과 장점, 한계가 있습니다. PVD는 증착 또는 스퍼터링과 같은 물리적 공정에 의존하여 일반적으로 낮은 온도(250°C~500°C)의 진공 조건에서 박막을 증착합니다. 압축 응력이 있는 얇고 매우 단단한 코팅(3~5μm)을 생성하므로 중단 절삭(예: 밀링)과 같은 애플리케이션에 이상적입니다. 반면 CVD는 고온(800~1000°C)에서 화학 반응을 통해 균일성과 밀도가 뛰어난 두꺼운 코팅(10~20μm)을 증착하므로 연속 절삭 공정(예: 선삭)에 적합합니다. PVD는 금속, 합금, 세라믹을 포함한 광범위한 재료를 증착할 수 있는 반면, CVD는 일반적으로 세라믹과 폴리머로 제한됩니다. PVD 코팅은 적용 속도가 빠르지만 밀도가 낮고 균일하지 않은 반면, CVD 코팅은 밀도가 높고 균일하지만 처리 시간이 더 오래 걸립니다.
핵심 사항 설명:
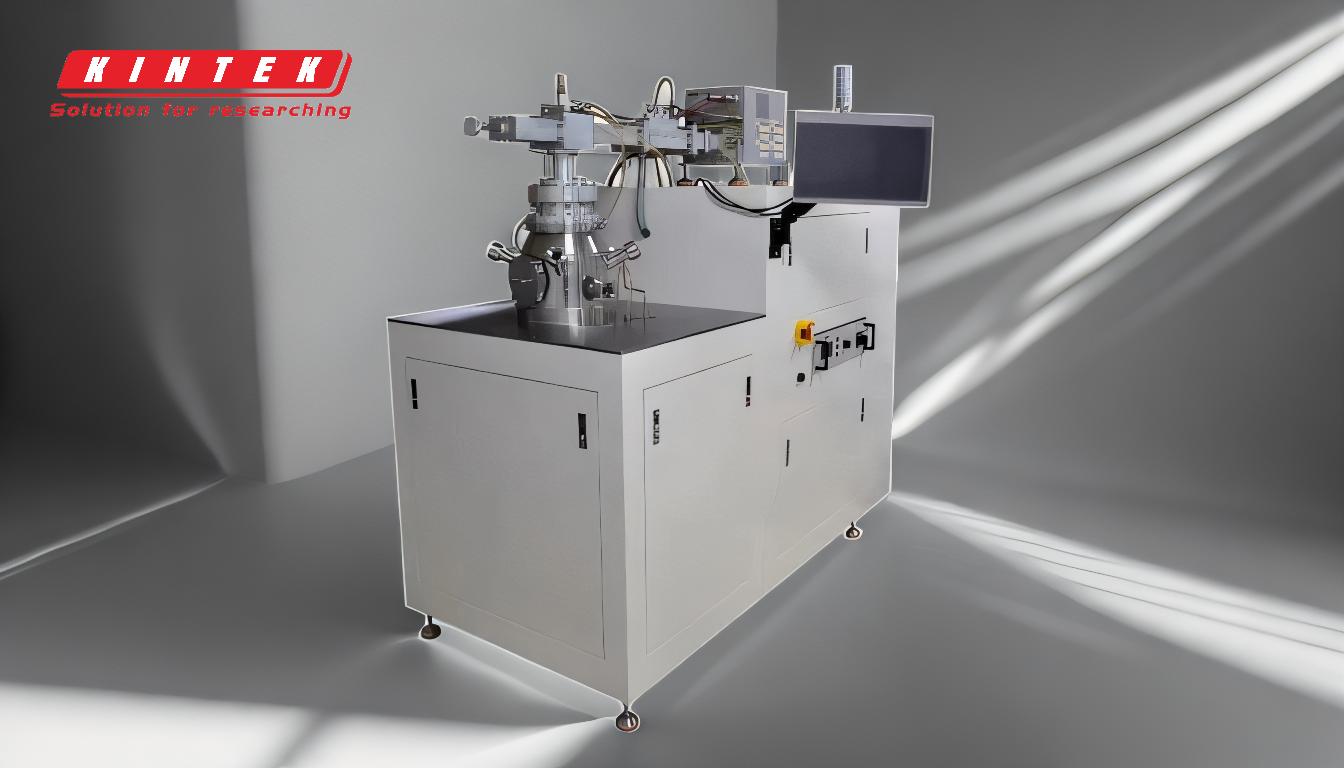
-
증착 프로세스:
- PVD: 진공 환경에서 증발 또는 스퍼터링과 같은 물리적 공정을 사용합니다. 재료는 고체 대상에서 증발되어 기판에 응축됩니다.
- CVD: 기체 전구체와 관련된 화학 반응에 의존합니다. 전구체 가스가 기판 표면에서 반응하여 코팅을 형성합니다.
-
온도 범위:
- PVD: 비교적 낮은 온도(250°C~500°C)에서 작동하므로 온도에 민감한 기질에 적합합니다.
- CVD: 고온(800~1000°C)에서 사용해야 하므로 이러한 열을 견디지 못하는 소재에는 사용이 제한됩니다.
-
코팅 두께:
- PVD: 압축 응력으로 더 얇은 코팅(3~5μm)을 생성하여 정밀한 응용 분야에 이상적입니다.
- CVD: 더 두꺼운 코팅(10~20μm)을 더 균일하게 증착하여 견고하고 내마모성이 강한 층이 필요한 응용 분야에 적합합니다.
-
재료 호환성:
- PVD: 금속, 합금, 세라믹 등 다양한 재료를 보관할 수 있습니다.
- CVD: 공정의 화학적 특성으로 인해 주로 세라믹과 폴리머로 제한됩니다.
-
코팅 속성:
- PVD: 코팅의 밀도가 낮고 균일하지 않지만 도포 속도가 빠릅니다. 내구성이 뛰어나며 더 높은 온도에도 견딜 수 있습니다.
- CVD: 코팅은 밀도가 높고 균일하며 접착력이 뛰어납니다. 하지만 도포하는 데 시간이 오래 걸리고 중단된 절단 공정에는 적합하지 않습니다.
-
애플리케이션:
- PVD: 중단된 절삭 공정(예: 밀링) 및 얇고 단단한 코팅이 필요한 응용 분야에 가장 적합합니다.
- CVD: 연속 절삭 공정(예: 선삭) 및 두꺼운 내마모성 코팅이 필요한 애플리케이션에 이상적입니다.
-
스트레스와 접착력:
- PVD: 냉각 중 압축 응력을 형성하여 코팅 접착력과 내구성을 향상시킵니다.
- CVD: 일반적으로 인장 응력이 발생하여 접착력에 영향을 줄 수 있지만 고온 공정으로 완화됩니다.
-
처리 속도:
- PVD: 증착 속도가 빨라 대량 생산에 더 효율적입니다.
- CVD: 화학 반응 과정으로 인해 증착 속도는 느리지만 코팅 품질이 우수합니다.
-
환경적 고려 사항:
- PVD: 진공 상태에서 작동하여 환경 오염을 줄이고 더 깨끗하게 청소할 수 있습니다.
- CVD: 화학 반응을 수반하며 종종 휘발성 전구체를 취급해야 하므로 환경 및 안전 문제가 발생할 수 있습니다.
-
비용 및 복잡성:
- PVD: 일반적으로 낮은 온도 요구 사항과 빠른 처리 시간으로 인해 비용이 저렴하고 구현이 더 간단합니다.
- CVD: 고온 장비, 더 긴 처리 시간, 화학 반응의 정밀한 제어 필요성으로 인해 더 비싸고 복잡합니다.
이러한 주요 차이점을 이해함으로써 장비 및 소모품 구매자는 특정 응용 분야 요구 사항에 가장 적합한 코팅 기술에 대해 정보에 입각한 결정을 내릴 수 있습니다. PVD는 정밀도, 내구성 및 온도에 민감한 애플리케이션에 이상적이며, CVD는 고온 공정에 두껍고 균일하며 내마모성이 뛰어난 코팅을 제공하는 데 탁월합니다.
요약 표:
측면 | PVD | CVD |
---|---|---|
증착 프로세스 | 진공 환경에서의 물리적 공정(증착/스퍼터링). | 기판의 기체 전구체와의 화학 반응. |
온도 범위 | 250°C~500°C, 온도에 민감한 소재에 적합합니다. | 800~1000°C, 내열성 소재로 제한됩니다. |
코팅 두께 | 압축 응력이 있는 얇은 코팅(3~5μm). | 균일성이 뛰어난 두꺼운 코팅(10~20μm). |
재료 호환성 | 금속, 합금, 세라믹. | 주로 세라믹과 폴리머입니다. |
코팅 속성 | 밀도가 낮고 균일하지 않지만 적용 속도가 빠릅니다. | 밀도가 높고 균일하지만 적용 속도가 느립니다. |
애플리케이션 | 중단된 절단(예: 밀링), 정밀 애플리케이션. | 연속 절삭(예: 선삭), 내마모성 애플리케이션. |
스트레스와 접착력 | 압축 응력은 접착력과 내구성을 향상시킵니다. | 고온 공정으로 인장 응력이 완화되었습니다. |
처리 속도 | 증착 속도가 빨라 대량 생산에 이상적입니다. | 증착 속도는 느리지만 코팅 품질은 우수합니다. |
환경 영향 | 진공 작동으로 더욱 깔끔한 공정. | 휘발성 전구체를 포함하므로 환경 및 안전 문제가 발생할 수 있습니다. |
비용 및 복잡성 | 비용이 저렴하고 구현이 간단합니다. | 고온 장비와 공정으로 인해 비용이 더 많이 들고 복잡합니다. |
애플리케이션에 맞는 PVD와 CVD 중 하나를 선택하는 데 도움이 필요하신가요? 지금 바로 전문가에게 문의하세요 를 통해 맞춤형 조언을 받으세요!