질화는 내마모성 및 표면 경도와 같은 재료 특성을 향상시키는 데 상당한 이점을 제공하지만 몇 가지 단점도 있습니다.여기에는 공정 제어, 환경 문제 및 경제적 요인과 관련된 문제가 포함됩니다.예를 들어 플라즈마 질화는 과열과 불안정한 아크를 방지하기 위해 세심한 표면 준비와 세심한 전력 분배 관리가 필요합니다.반면 액체 질화는 무독성 대체제가 개발되었음에도 불구하고 독성이 있는 시안화염을 사용하기 때문에 제한에 직면해 있습니다.또한 플라즈마 질화 장비와 관련된 높은 초기 비용과 전력/면적 관계로 인한 배치 처리의 제한으로 인해 도입이 더욱 복잡해집니다.
핵심 포인트 설명:
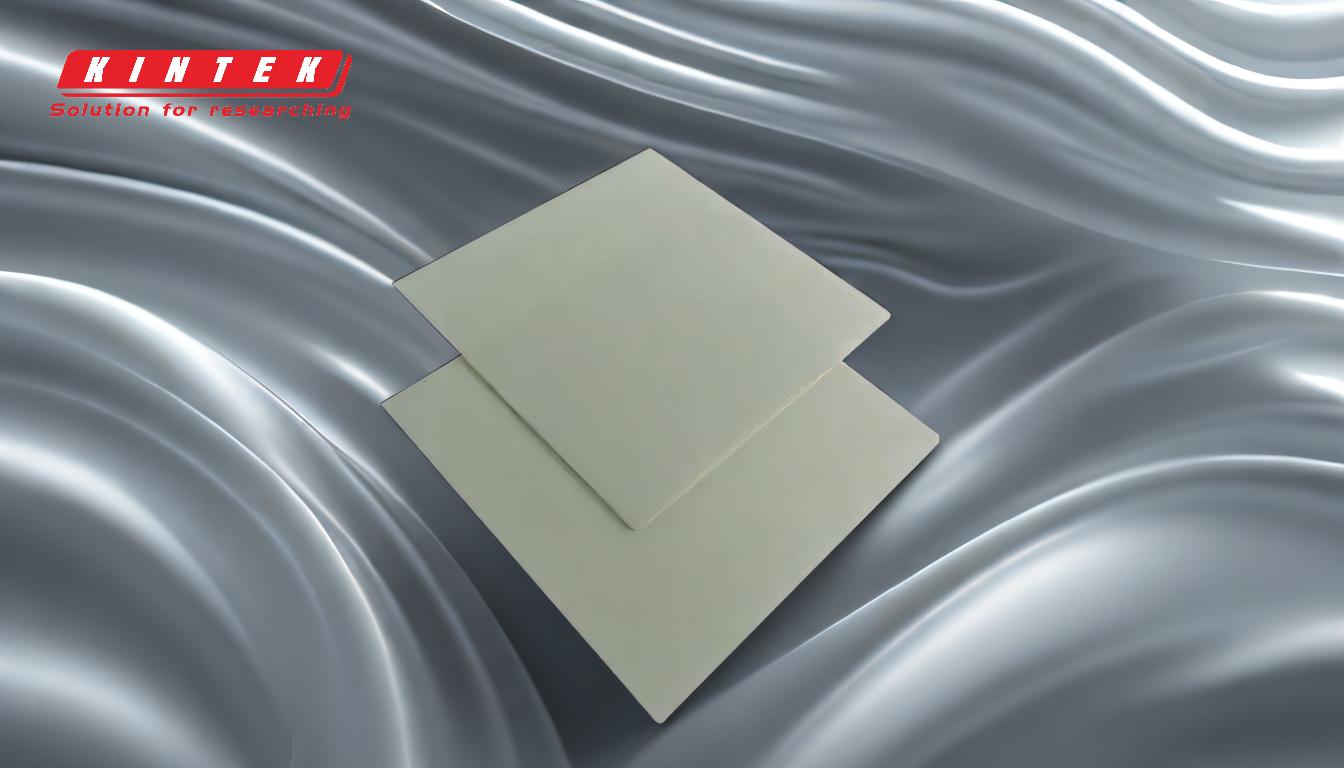
-
플라즈마 질화의 표면 청결 및 안정성:
- 중요한 표면 준비:플라즈마 질화의 효과는 부품 표면의 청결도에 따라 크게 달라집니다.오염이 있으면 가열 주기 동안 불안정한 아크가 형성되어 질화 층의 품질이 저하될 수 있습니다.
- 과열 방지:부품은 공정 중 과열을 방지하기 위해 정밀한 수리 및 준비가 필요하며, 이는 재료의 성능 저하 또는 고장으로 이어질 수 있습니다.
-
배치 처리 제한 사항:
- 권력/지역 관계:플라즈마 질화에서는 전력/면적 관계로 인해 비슷한 크기의 부품을 한 번에 처리할 수 없습니다.이러한 제한으로 인해 여러 번 실행하거나 특수 설정해야 하므로 생산 시간과 비용이 모두 증가합니다.
-
경제적 고려 사항:
- 높은 초기 비용:플라즈마 질화를 위한 설정에는 장비와 기술에 대한 상당한 초기 투자가 필요합니다.이러한 높은 비용은 소규모 사업장이나 예산이 제한된 사업장에는 장벽이 될 수 있습니다.
-
액체 질화의 환경 및 건강 문제:
- 독성 시안화염 사용:기존의 액체 질화 공정은 시안화염을 사용하므로 작업자의 건강에 심각한 위험을 초래하고 폐기물 처리 시 환경 문제를 야기합니다.
- 규제 제한:이러한 건강 및 환경 위험으로 인해 시안화염의 사용이 점점 더 제한되고 있으며, 업계에서는 무독성 대안으로 나아가고 있지만 아직 기존 방법의 효과에는 미치지 못할 수 있습니다.
-
얇은 질화 층:
- 레이어 두께:액체 질화는 일반적으로 비교적 얇은 질화 층(0.01~0.02mm)을 생성하므로, 더 깊은 케이스 경화가 필요한 응용 분야에는 충분하지 않을 수 있습니다.
요약하면, 질화 공정은 재료 특성을 크게 향상시키지만 신중한 고려가 필요한 일련의 과제를 수반합니다.여기에는 가공의 기술적 한계, 경제적 장벽, 환경 및 건강 문제, 특히 액체 질화와 관련된 문제가 포함됩니다.이러한 단점을 이해하는 것은 업계에서 질화 기술의 도입과 실행에 대해 정보에 입각한 결정을 내리는 데 매우 중요합니다.
요약 표:
단점 | 설명 |
---|---|
표면 청결 및 안정성 | 플라즈마 질화는 불안정한 아크와 과열을 방지하기 위해 세심한 표면 준비가 필요합니다. |
배치 처리의 한계 | 전력/면적 관계로 인해 일괄 처리가 제한되어 시간과 비용이 증가합니다. |
높은 초기 비용 | 플라즈마 질화 장비에는 상당한 초기 투자가 필요합니다. |
환경 및 건강 문제 | 액체 질화는 독성 시안화염을 사용하므로 건강 및 폐기 문제가 발생할 수 있습니다. |
얇은 질화 층 | 액체 질화는 얇은 층(0.01~0.02mm)을 생성하므로 일부 애플리케이션의 경우 깊이가 제한됩니다. |
질화 처리의 어려움을 해결하는 데 도움이 필요하신가요? 지금 바로 전문가에게 문의하세요. 맞춤형 솔루션에 대해 문의하세요!