냉간 등방성 프레스(CIP)는 일반적으로 고무나 플라스틱으로 만들어진 유연한 금형에 담긴 분말 재료에 균일한 정수압을 가하는 제조 공정입니다.이 압력은 금형을 통해 전달되어 분말을 원하는 모양으로 압축합니다.CIP는 내화 재료, 초경합금, 세라믹 절연체, 식품 가공 등 다양한 산업 분야에서 널리 사용됩니다.이 공정은 기존의 단축 프레스 방식으로는 달성하기 어려운 크고 복잡한 형상을 만드는 데 특히 유용합니다.균일한 압력으로 압축된 재료 전체에 일관된 밀도와 강도를 보장하므로 높은 정밀도와 내구성이 필요한 애플리케이션에 이상적입니다.
핵심 포인트 설명:
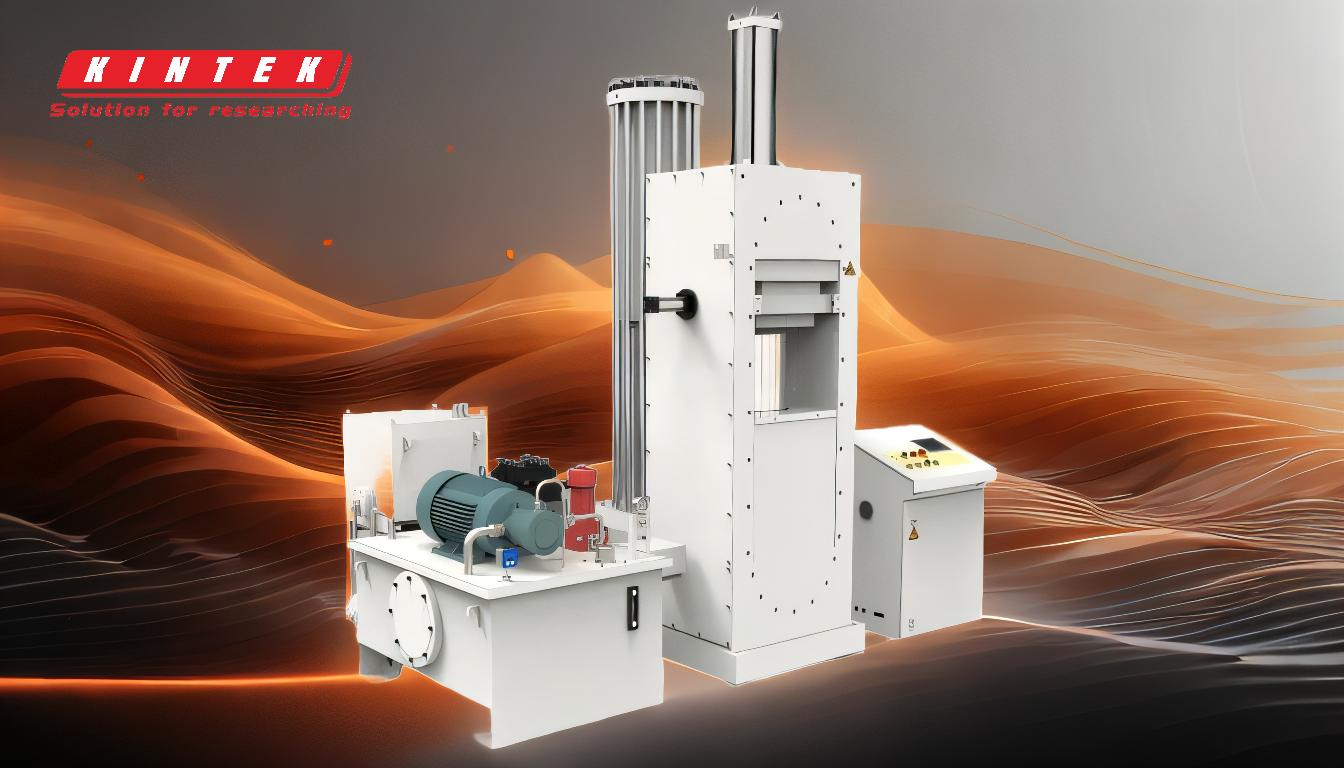
-
냉간 등방성 프레스(CIP)의 정의:
- 냉간 등방성 압착은 유연한 금형 안에 들어있는 분말 재료에 균일한 정수압을 가하는 분말 성형 기술입니다.압력이 금형을 통해 전달되어 분말을 단단한 모양으로 압축합니다.이 공정은 일반적으로 열을 사용하지 않고 실온 또는 그보다 약간 높은 온도에서 수행되기 때문에 '콜드'라고 합니다.
-
CIP 작동 방식:
- CIP 공정에서는 분말 재료를 유연한 몰드 안에 넣은 다음 고압 챔버에 삽입합니다.액체 매체(주로 오일-물 혼합물)가 챔버로 펌핑되어 모든 방향에서 균일하게 가압됩니다.이렇게 하면 정수압이 발생하여 파우더가 조밀하고 균일한 모양으로 압축됩니다.챔버의 압력은 최대 100,000psi에 달할 수 있어 철저한 압축을 보장합니다.
-
CIP의 적용 분야:
-
CIP는 다양한 산업 분야에서 다음과 같은 다양한 부품을 생산하는 데 사용됩니다:
- 내화 재료:노즐, 블록, 도가니 등.
- 초경합금:내마모성 공구 및 금속 성형 분야에 사용됩니다.
- 등방성 흑연:모든 방향에서 균일한 특성이 필요한 응용 분야에 적합합니다.
- 세라믹 절연체:전기 및 전자 애플리케이션에 사용됩니다.
- 식품 가공:온도 상승 없이 식품을 압축하는 데 적합합니다.
- 인공 뼈 및 의료용 임플란트:균일한 밀도와 강도가 중요한 경우.
- 플라스틱 튜브 및 막대:산업 및 소비자 애플리케이션용.
-
CIP는 다양한 산업 분야에서 다음과 같은 다양한 부품을 생산하는 데 사용됩니다:
-
CIP의 장점:
- 균일한 밀도:정수압으로 파우더가 균일하게 압축되어 제품 전체에 걸쳐 밀도와 강도가 일정합니다.
- 복잡한 모양:CIP는 기존 프레스 방식으로는 달성하기 어려운 크고 복잡한 모양을 제작하는 데 이상적입니다.
- 다목적성:이 공정은 금속, 세라믹, 플라스틱 등 다양한 재료에 사용할 수 있습니다.
- 최소한의 온도 상승:이 공정은 실온 또는 그 근처에서 수행되므로 열에 민감한 재료에 적합합니다.
-
다른 프레스 방법과의 비교:
- 한 방향 또는 두 방향에서 압력을 가하는 단축 프레스와 달리 CIP는 모든 방향에서 균일하게 압력을 가합니다.따라서 밀도가 더 균일해지고 단축 프레스에서 발생할 수 있는 밀도 구배의 위험이 없습니다.CIP는 단축 프레스에 비해 너무 크거나 복잡한 부품에 특히 유용합니다.
-
CIP에 적합한 재료:
-
CIP는 다음을 포함한 다양한 재료에 적합합니다:
- 내화성 재료:알루미나, 지르코니아, 실리콘 카바이드 등.
- 금속:텅스텐 및 몰리브덴과 같은 고융점 금속 포함.
- 세라믹:절연체, 필터 및 기타 산업용 애플리케이션에 사용됩니다.
- 플라스틱 및 수지:튜브, 막대 및 기타 구성품을 성형하는 데 사용됩니다.
- 식품 제품:분말을 고체 형태로 압축하는 데 사용됩니다.
-
CIP는 다음을 포함한 다양한 재료에 적합합니다:
-
CIP의 한계:
- 정밀도:CIP는 크거나 복잡한 형상을 제작하는 데 탁월하지만 열간 등방성 프레스(HIP) 또는 기계 가공과 같은 다른 방법과 같은 수준의 정밀도를 달성하지 못할 수 있습니다.
- 비용:CIP에 필요한 장비와 금형은 비용이 많이 들기 때문에 소규모 생산에는 적합하지 않을 수 있습니다.
- 재료 제한:일부 재료는 저온 등압 하에서 잘 압축되지 않을 수 있으며 추가 가공 단계가 필요할 수 있습니다.
-
CIP의 미래 트렌드:
- 첨단 재료:새로운 재료가 개발됨에 따라, 특히 균일한 밀도와 강도가 필요한 재료의 경우 CIP가 공정에서 핵심적인 역할을 할 가능성이 높습니다.
- 자동화:자동화 및 제어 시스템의 발전으로 CIP 프로세스의 효율성과 정밀도가 향상될 것으로 예상됩니다.
- 지속 가능성:재활용 금속 및 생분해성 플라스틱과 같은 지속 가능한 소재에 CIP를 사용하는 것에 대한 관심이 높아지고 있습니다.
요약하면, 냉간 등방성 프레스는 분말을 균일하고 조밀한 모양으로 압축하는 다목적의 효과적인 방법입니다.복잡한 모양을 생산하고 다양한 재료로 작업할 수 있어 다양한 산업 분야에서 유용한 도구입니다.이 공정에 사용되는 장비에 대한 자세한 내용은 다음을 참조하세요. 등방성 프레스 주제.
요약 표:
주요 측면 | 세부 정보 |
---|---|
정의 | 상온에서 균일한 정수압을 이용한 분말 성형 기술입니다. |
공정 | 유연한 몰드에 담긴 분말을 액체 매체를 사용하여 균일하게 가압합니다. |
응용 분야 | 내화 재료, 초경합금, 세라믹 절연체, 식품 가공, 의료용 임플란트. |
장점 | 균일한 밀도, 복잡한 모양, 다용도성, 최소한의 온도 상승. |
적합한 재료 | 금속, 세라믹, 플라스틱, 식품, 내화성 재료. |
제한 사항 | 낮은 정밀도, 높은 비용, 재료별 한계. |
미래 트렌드 | 첨단 소재, 자동화, 지속 가능성. |
저온 등방성 프레스로 제조 공정을 혁신하는 방법을 알아보세요. 지금 바로 전문가에게 문의하세요 !