분말 야금(PM)은 금속과 세라믹을 포함한 다양한 재료로 부품을 생산할 수 있는 다목적 제조 방법입니다.하지만 여러 가지 요인으로 인해 주로 소형 부품 생산에 제한을 받습니다.가장 큰 한계는 일반적으로 약 1,500톤에 달하는 업계에서 사용되는 프레스의 크기로, 부품의 평면 면적이 약 40~50평방인치로 제한된다는 점입니다.또한 PM은 복잡한 형상을 제작할 수 있지만 주조나 단조와 같은 다른 방식에 비해 더 까다롭습니다.또한 PM 부품은 주조 또는 단조 부품의 강도와 연성이 부족한 경우가 많기 때문에 더 높은 기계적 성능이 필요한 대형 부품의 경우 단점이 될 수 있습니다.이러한 한계에도 불구하고 PM은 용융, 봉쇄 또는 변형이 어려운 소재에 적합한 옵션으로 심정 드릴링 공구와 같은 특정 응용 분야에 적합합니다.
핵심 사항 설명:
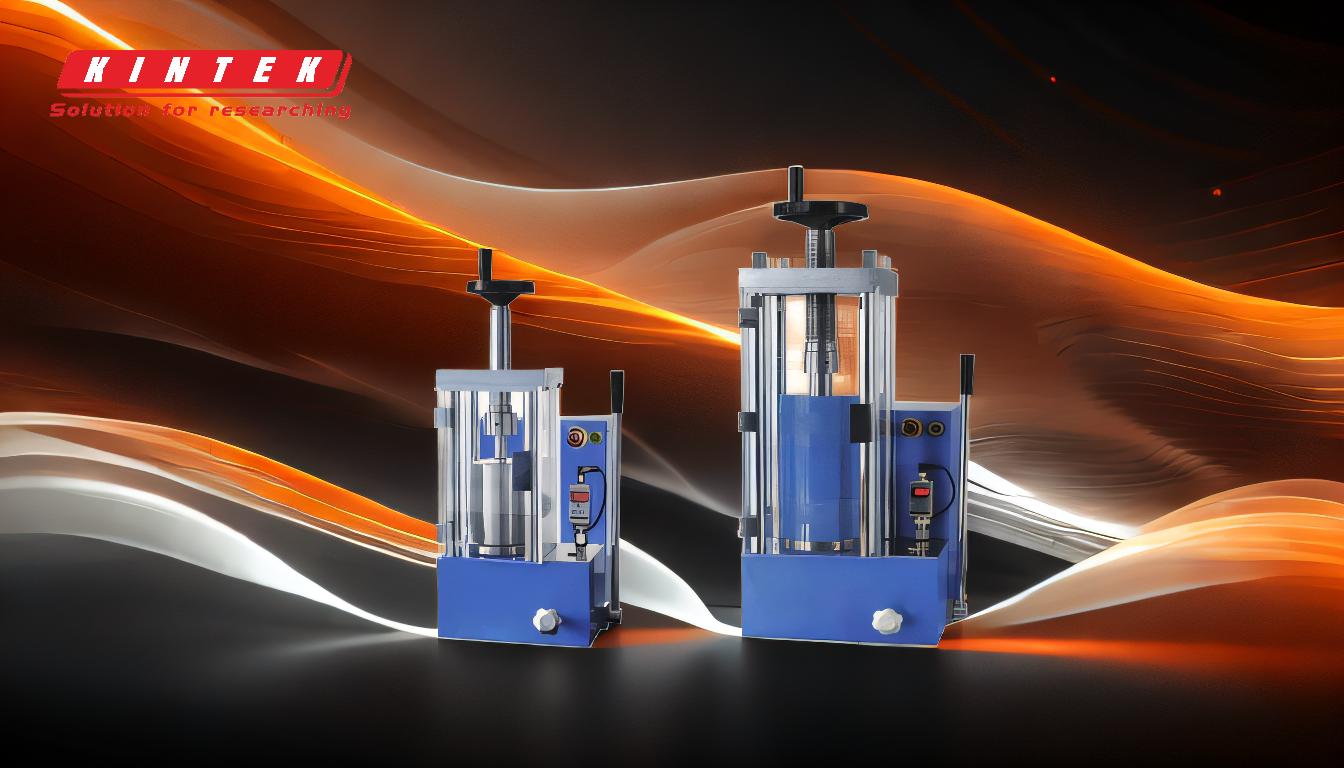
-
언론사 크기 제한:
- 분말 야금에 사용되는 가장 큰 프레스는 약 1,500톤으로, 부품의 실제 크기는 약 40~50평방인치의 평면 영역으로 제한됩니다.
- 이러한 제약은 압축 공정에서 균일한 압력 분포가 필요하기 때문인데, 이는 부품이 커질수록 점점 더 어려워집니다.
- 더 큰 부품을 생산하려면 더 큰 프레스가 필요하지만 이러한 장비는 업계에서 일반적으로 사용할 수 없습니다.
-
복잡한 형상의 도전 과제:
- 분말 야금은 복잡한 형상을 만들 수 있지만 주조나 단조와 같은 다른 제조 방법에 비해 더 까다롭습니다.
- 숙련된 제조업체는 이러한 문제를 일부 극복할 수 있지만, 이 공정은 본질적으로 분말 분포와 압축을 정밀하게 제어해야 하며, 복잡성과 크기가 증가함에 따라 더욱 어려워집니다.
-
기계적 특성:
- PM 부품은 일반적으로 주조 또는 단조로 생산된 부품과 동일한 수준의 강도와 연성을 얻지 못합니다.
- 이는 분말을 압축하고 소결하는 PM 공정의 특성으로 인해 잠재적인 다공성과 입자 간 결합이 약해지기 때문입니다.
- 더 높은 기계적 성능이 필요한 대형 부품의 경우 이러한 한계로 인해 기존 방식에 비해 PM은 적합하지 않습니다.
-
소재의 다양성:
- 분말 야금은 한계에도 불구하고 금속과 세라믹을 포함하여 처리할 수 있는 재료가 매우 다양합니다.
- 따라서 기존 방법으로는 녹이거나 포함하거나 변형하기 어려운 재료에 PM은 매력적인 옵션입니다.
-
특수 애플리케이션:
- 대형 부품의 경우 금속 또는 세라믹 분말과 바인더의 혼합물을 금형에 채우는 침투 주조와 같은 대체 방법이 사용됩니다.
- 이 접근 방식은 심정 시추용 다결정 다이아몬드 복합재(PDC) 드릴 비트 제조와 같은 특수 애플리케이션에 사용되며, 크기 제한에도 불구하고 PM의 고유한 장점을 활용할 수 있습니다.
요약하면, 대형 부품 생산에서 분말 야금의 한계는 주로 프레스 크기 제약, 복잡한 형상의 문제, 다른 방식에 비해 상대적으로 낮은 기계적 특성으로 인해 발생합니다.그러나 재료 가공의 다양성과 특수 응용 분야에 대한 적합성으로 인해 운영 한계 내에서 가치 있는 제조 기술입니다.
요약 표:
키 제한 | 설명 |
---|---|
프레스 크기 제약 | 가장 큰 프레스는 최대 1,500톤으로, 부품 크기가 40~50평방인치로 제한됩니다. |
복잡한 형상 | 주조나 단조에 비해 제작이 더 까다롭습니다. |
기계적 특성 | 주조 또는 단조 부품보다 강도와 연성이 낮습니다. |
다양한 소재 활용성 | 금속과 세라믹을 처리할 수 있어 녹거나 변형하기 어려운 재료에 이상적입니다. |
특수 애플리케이션 | 크기 제한에도 불구하고 PDC 비트와 같은 깊은 유정 시추 공구에 사용됩니다. |
분말 야금이 귀사의 특수한 요구를 어떻게 충족시킬 수 있는지 알아보세요. 지금 바로 문의하세요 !