압축 성형과 사출 성형은 플라스틱 및 복합 재료를 성형하는 데 널리 사용되는 두 가지 제조 공정입니다.두 방법 모두 효과적이지만 공정 역학, 재료 적합성 및 생산 효율성 측면에서 큰 차이가 있습니다.압축 성형은 예열된 재료를 가열된 금형에 넣고 압력을 가하여 모양을 만드는 방식으로, 비교적 단순한 대형 부품에 이상적입니다.반면 사출 성형은 용융된 재료를 고압으로 금형에 주입하여 복잡한 설계와 대량 생산이 가능합니다.주요 차이점은 부품의 복잡성, 생산 속도 및 재료 취급에 있습니다.
핵심 사항을 설명합니다:
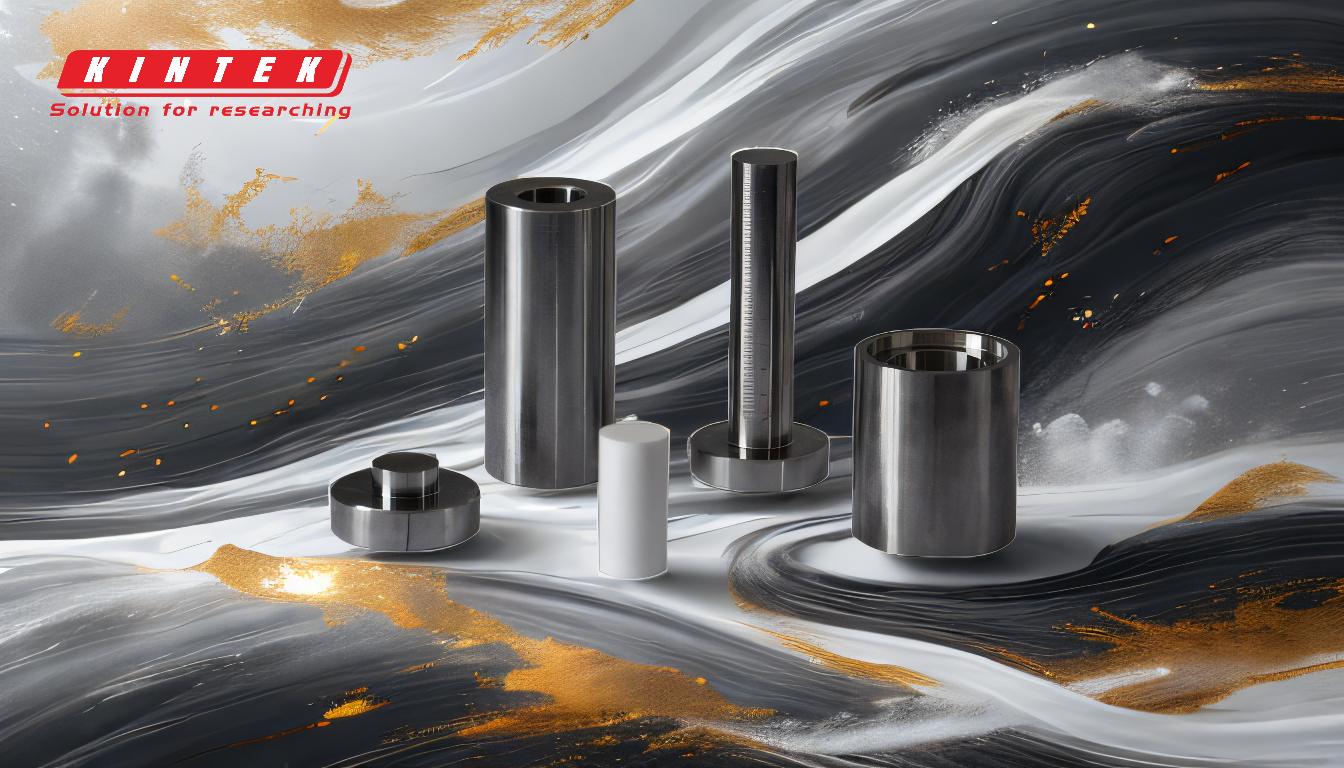
-
프로세스 역학:
- 압축 성형:이 공정에서는 예열된 재료(주로 열경화성 폴리머 또는 복합재)를 열린 금형 캐비티에 넣습니다.그런 다음 금형을 닫고 압력을 가하여 재료가 금형의 모양에 맞도록 합니다.재료는 열과 압력으로 경화되어 원하는 부품으로 굳어집니다.
- 사출 성형:이 공정에는 재료(일반적으로 열가소성 플라스틱)가 녹을 때까지 가열하는 과정이 포함됩니다.그런 다음 용융된 재료를 고압으로 밀폐된 금형에 주입합니다.재료가 냉각되고 굳으면 금형이 열리고 부품이 배출됩니다.이 방법을 사용하면 재료 흐름을 보다 정밀하게 제어할 수 있으며 복잡한 형상에 적합합니다.
-
부품의 복잡성:
- 압축 성형:덜 복잡한 디테일이 있는 크고 단순한 부품에 가장 적합합니다.이 공정은 재료 흐름과 압력 분포의 제한으로 인해 복잡한 모양이나 미세한 특징을 가진 부품을 생산하는 데는 덜 효과적입니다.
- 사출 성형:복잡한 형상, 얇은 벽, 미세한 디테일이 있는 부품 생산에 이상적입니다.고압 사출을 통해 용융된 재료가 가장 복잡한 금형 캐비티까지 채울 수 있어 매우 섬세하고 정밀한 부품을 제작할 수 있습니다.
-
생산 속도 및 효율성:
- 압축 성형:일반적으로 사출 성형에 비해 속도가 느리며, 특히 대형 부품의 경우 더욱 그렇습니다.이 공정에는 예열된 재료를 금형에 넣고 압력을 가하는 등 수동 또는 반자동 단계가 포함되므로 사이클 시간이 늘어날 수 있습니다.
- 사출 성형:특히 대량 생산 시 더 빠른 생산 속도를 제공합니다.이 공정은 시간당 수천 개의 부품을 생산할 수 있는 기계로 고도로 자동화되어 있습니다.따라서 사출 성형은 대규모 생산에 더욱 효율적입니다.
-
재료 적합성:
- 압축 성형:주로 경화 후 재용융할 수 없는 열경화성 소재에 주로 사용됩니다.특정 복합재 및 고무 소재에도 적합합니다.이 공정은 사출 성형에 비해 재료 옵션의 다양성이 떨어집니다.
- 사출 성형:재용융 및 재사용이 가능한 다양한 열가소성 소재와 호환됩니다.이러한 다용도성 덕분에 사출 성형은 소비재부터 자동차 부품에 이르기까지 광범위한 응용 분야에 적합합니다.
-
툴링 및 장비 비용:
- 압축 성형:일반적으로 사출 성형에 비해 툴링과 장비가 덜 필요합니다.압축 성형에 사용되는 금형은 종종 더 간단하고 생산 비용이 적게 들기 때문에 중저가 생산량에 더 경제적인 선택입니다.
- 사출 성형:복잡한 금형과 특수 기계가 필요하기 때문에 초기 비용이 더 많이 듭니다.그러나 생산 속도와 효율성이 높아지면 특히 대량 생산의 경우 시간이 지남에 따라 이러한 비용을 상쇄할 수 있습니다.
요약하면, 압축 성형과 사출 성형 중 어떤 것을 선택할지는 부품의 복잡성, 생산량, 재료 유형, 예산 제약 등 프로젝트의 구체적인 요구 사항에 따라 달라집니다.압축 성형은 생산량이 적은 크고 단순한 부품에 더 적합하며, 사출 성형은 복잡하고 세밀한 부품을 빠른 속도와 대량으로 생산하는 데 탁월합니다.
요약 표:
측면 | 압축 성형 | 사출 성형 |
---|---|---|
공정 역학 | 예열된 재료를 개방형 몰드에 넣고 열과 압력으로 경화시킵니다. | 용융된 재료를 고압으로 밀폐된 금형에 주입합니다. |
부품의 복잡성 | 디테일이 복잡하지 않은 크고 단순한 부품에 적합합니다. | 복잡한 형상, 얇은 벽, 미세한 디테일에 이상적입니다. |
생산 속도 | 느린 수동 또는 반자동 단계는 사이클 시간을 증가시킵니다. | 더 빠르고, 고도로 자동화되어 대량 생산에 적합합니다. |
재료 적합성 | 주로 열경화성 소재, 제한된 소재 다양성. | 광범위한 열가소성 소재, 다양한 응용 분야. |
툴링 및 장비 | 저렴한 툴링 및 장비로 중소규모 생산량에 경제적입니다. | 초기 비용은 높지만 대량 생산 시에는 효율성이 이를 상쇄합니다. |
프로젝트에 적합한 성형 공정을 선택하는 데 도움이 필요하신가요? 지금 바로 전문가에게 문의하세요. !