디바인딩은 분말 야금 및 기술 세라믹과 같은 제조 공정에서 소결 전에 부품에서 결합제나 유기 물질을 제거하는 중요한 단계입니다.처음에 재료를 성형하고 압축하는 데 필요한 이러한 바인더는 최종 제품에 남아있으면 해로운 영향을 미칩니다.디바인딩은 소결 과정에서 뒤틀림, 균열, 오염 등의 결함을 일으킬 수 있는 불순물이 없는지 확인합니다.이 공정에는 재료 손상을 방지하기 위해 온도, 압력, 대기를 정밀하게 제어하는 과정이 포함됩니다.바인더를 제거함으로써 소결을 위한 부품을 준비하여 더 강력하고 내구성이 뛰어난 최종 제품을 만들고 용광로 막힘이나 표면 오염과 같은 문제를 방지합니다.
핵심 사항 설명:
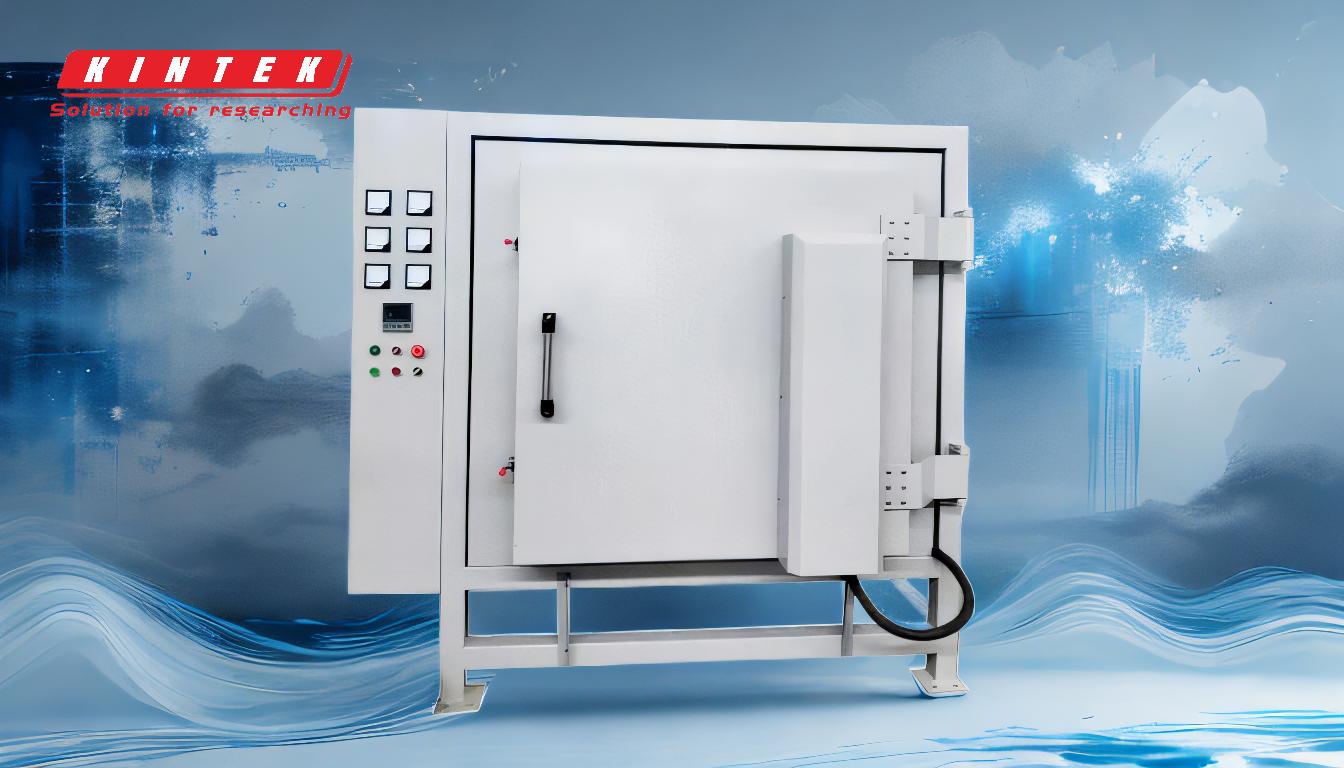
-
디바인딩의 목적:
- 디바인딩은 부품의 성형 및 압축 과정에서 사용되는 결합제 또는 유기 물질을 제거합니다.
- 이러한 바인더는 초기에는 필요하지만 소결 과정에서 최종 제품의 무결성을 방해할 수 있으므로 바람직하지 않습니다.
-
제조 과정에서의 중요성:
- 부품에 뒤틀림, 균열, 기포 등의 결함을 유발할 수 있는 불순물이 없는지 확인합니다.
- 소결로와 최종 제품 모두에 영향을 줄 수 있는 소결로의 오염을 방지합니다.
-
프로세스 세부 정보:
- 디바인딩은 일반적으로 실온에서 시작하여 약 600°C에서 완료됩니다.
- 재료 손상을 방지하기 위해 온도 프로파일, 압력, 가스 분위기, 어닐링 시간을 세심하게 제어해야 합니다.
-
최종 제품에 미치는 영향:
- 최종 제품에 기공이나 약점을 만들 수 있는 바인더를 제거합니다.
- 소결을 위해 부품을 준비하여 더 강력하고 내구성 있는 결과물을 보장합니다.
-
효율성 및 실질적인 이점:
- 제조 공정이 느려질 수 있는 퍼니스 막힘을 방지합니다.
- 디바인딩 없이 소결할 때보다 전체 공정이 더 빠르고 효율적입니다.
-
응용 분야:
- 분말 야금 및 기술 세라믹 제조에 일반적으로 사용됩니다.
- 정밀도와 내구성이 요구되는 산업에서 결함 없는 고품질 부품을 생산하는 데 필수적입니다.
제조업체는 이러한 핵심 사항을 이해함으로써 디바인딩 공정을 최적화하여 생산 워크플로우에서 더 나은 결과를 얻을 수 있습니다.
요약 표:
측면 | 세부 정보 |
---|---|
목적 | 결합제 또는 유기 물질을 제거하여 재료 무결성을 보장합니다. |
중요성 | 뒤틀림, 균열, 용광로 오염과 같은 결함을 방지합니다. |
공정 | 제어된 온도(최대 600°C), 압력 및 가스 분위기. |
영향 | 소결할 부품을 준비하여 더 강력하고 내구성 있는 제품을 만듭니다. |
효율성 | 용광로 막힘을 방지하고 제조 공정 속도를 높입니다. |
애플리케이션 | 분말 야금, 기술 세라믹, 정밀 제조. |
더 나은 결과를 위해 디바인딩 공정을 최적화하세요. 지금 전문가에게 문의하세요 !