사출 성형과 압력 성형의 차이점은 공정, 메커니즘 및 적용 분야에 있습니다.사출 성형은 용융된 재료를 고압으로 금형 캐비티에 주입하여 원하는 모양으로 냉각 및 응고시킵니다.반면에 압력 성형은 열과 압력의 조합을 사용하여 재료를 성형하며, 용융된 재료를 주입할 필요가 없는 경우가 많습니다.두 가지 방법 모두 제조에 널리 사용되지만 재료, 디자인 복잡성 및 생산 요구 사항에 따라 적합성이 달라집니다.
핵심 사항을 설명합니다:
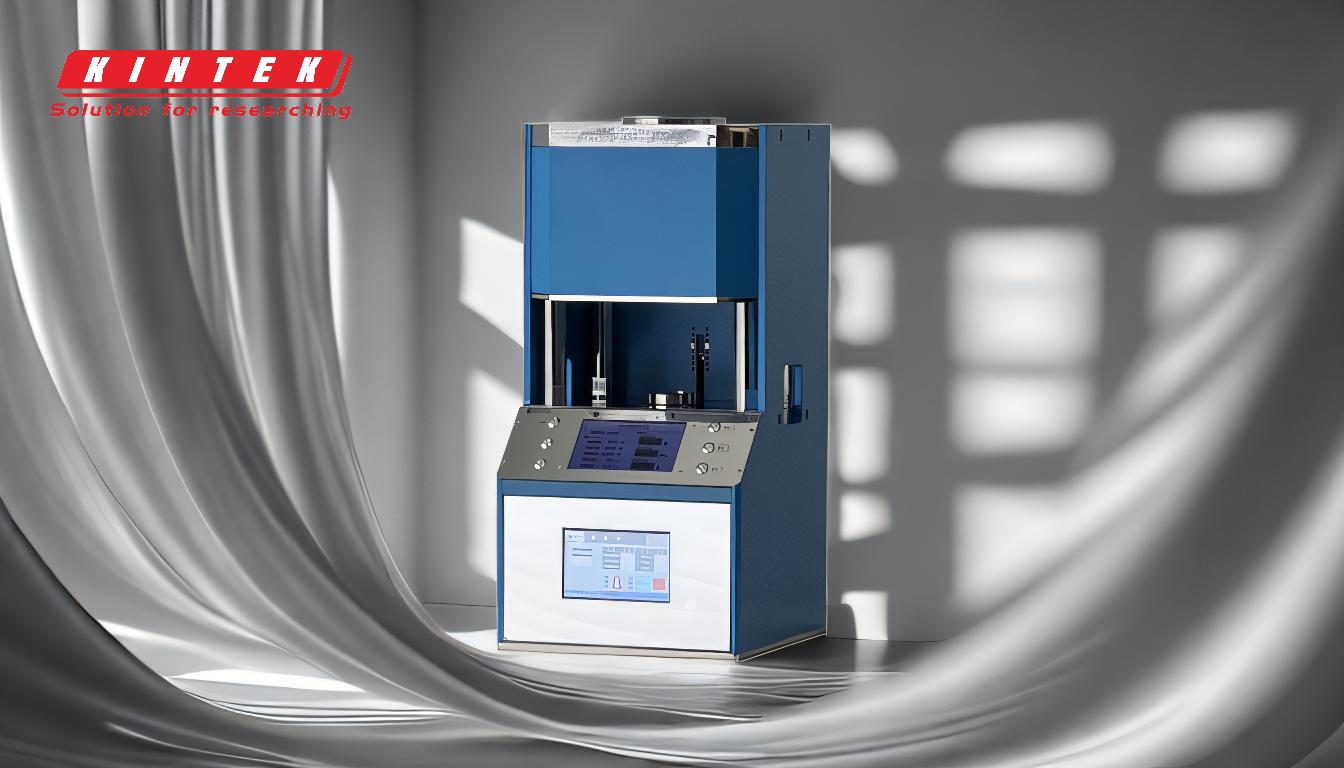
-
프로세스 메커니즘:
- 사출 성형:이 공정에는 재료(일반적으로 플라스틱)를 녹여 고압으로 금형에 주입하는 과정이 포함됩니다.재료가 금형 캐비티를 채우고 식은 후 응고되어 최종 제품을 형성합니다.고도로 자동화되고 효율적인 공정으로 대량 생산에 적합합니다.
- 압력 성형:이 방법은 재료(주로 열경화성 플라스틱 또는 복합재)에 열과 압력을 가하여 금형으로 성형하는 방법입니다.사출 성형과 달리 재료가 반드시 녹는 것이 아니라 압력을 받아 부드러워지고 성형됩니다.압력 하에서 경화 또는 경화가 필요한 재료에 자주 사용됩니다.
-
재료 적합성:
- 사출 성형:여러 번 녹여 모양을 바꿀 수 있는 열가소성 플라스틱에 가장 적합합니다.일반적인 재료로는 폴리에틸렌, 폴리프로필렌, ABS 등이 있습니다.
- 압력 성형:성형 중 화학적 변화를 겪으며 재용융이 불가능한 열경화성 소재에 이상적입니다.페놀 수지 및 에폭시 복합 재료가 그 예입니다.
-
설계 복잡성:
- 사출 성형:미세한 디테일이 있는 매우 복잡하고 정교한 부품을 제작할 수 있습니다.얇은 벽, 언더컷 및 복잡한 형상을 가진 부품에 적합합니다.
- 압력 성형:단순한 모양과 큰 부품에 더 적합합니다.자동차 부품이나 전기 절연체와 같이 높은 강도와 내구성이 요구되는 부품에 주로 사용됩니다.
-
생산량:
- 사출 성형:자동화와 빠른 사이클 타임으로 대규모 생산에 매우 효율적입니다.수천 개 또는 수백만 개의 동일한 부품을 생산할 때 비용 효율적입니다.
- 압력 성형:일반적으로 소량에서 중간 규모의 생산량에 사용됩니다.사출 성형에 비해 노동 집약적이며 사이클 시간이 더 깁니다.
-
툴링 및 장비:
- 사출 성형:사출 성형기 및 정밀 금형과 같은 전문 장비가 필요합니다.초기 설정 비용은 높지만 수량에 따라 단위당 비용이 감소합니다.
- 압력 성형:고압과 열을 견딜 수 있도록 설계된 프레스와 금형을 사용합니다.이 장비는 일반적으로 사출 성형기보다 덜 복잡하지만 금형에는 여전히 상당한 투자가 필요할 수 있습니다.
-
응용 분야:
- 사출 성형:자동차, 소비재, 의료 기기 및 전자 제품과 같은 산업에서 하우징, 용기 및 기어와 같은 부품을 생산하기 위해 일반적으로 사용됩니다.
- 압력 성형:항공우주, 전기, 중장비 등 고강도 부품이 필요한 산업에서 주로 사용됩니다.예를 들면 회로 차단기, 절연체, 구조 부품 등이 있습니다.
요약하면 사출 성형과 압력 성형 중 어떤 것을 선택할지는 재료, 설계 요구 사항, 생산량 및 용도에 따라 달라집니다.사출 성형은 열가소성 수지로 만든 복잡한 대량 부품에 이상적이며, 압력 성형은 열경화성 재료로 만든 고강도 내구성 부품에 더 적합합니다.
요약 표
측면 | 사출 성형 | 압력 성형 |
---|---|---|
공정 메커니즘 | 고압으로 재료를 녹여 금형에 주입합니다. | 열과 압력을 사용하여 용융된 재료를 주입하지 않고 재료를 성형합니다. |
재료 적합성 | 열가소성 플라스틱(예: 폴리에틸렌, 폴리프로필렌)에 가장 적합합니다. | 열경화성 소재(예: 페놀 수지, 에폭시 복합재)에 이상적입니다. |
디자인 복잡성 | 섬세한 디테일이 있는 복잡하고 정교한 부품에 적합합니다. | 더 단순한 모양과 더 큰 고강도 구성 요소에 더 적합합니다. |
생산량 | 빠른 사이클 타임으로 대량 생산. | 더 긴 사이클 타임의 중저가 생산량. |
툴링 및 장비 | 특수 기계와 정밀 금형이 필요합니다. | 고압 및 고열용으로 설계된 프레스와 금형을 사용합니다. |
애플리케이션 | 자동차, 소비재, 의료 기기, 전자 제품. | 항공우주, 전기, 고강도 부품을 위한 중장비. |
프로젝트에 적합한 성형 공정을 선택하는 데 도움이 필요하신가요? 지금 바로 전문가에게 문의하세요!