플라즈마 질화와 전통적인 질화(가스 질화 또는 배스 질화 등)는 금속 부품의 내마모성, 피로 강도 및 내식성을 개선하는 데 사용되는 표면 경화 기술입니다.주요 차이점은 공정 메커니즘과 그에 따른 이점에 있습니다.플라즈마 질화는 이온화된 가스(플라즈마)를 사용하여 재료 표면에 질소를 도입하는 반면, 기존 질화는 가스 또는 액체 매체를 사용합니다.플라즈마 질화는 낮은 공정 온도, 왜곡 감소, 처리 시간 단축, 환경 호환성 향상 등의 이점을 제공합니다.또한 특별한 준비 단계가 필요하지 않으므로 스테인리스 스틸을 비롯한 다양한 소재에 적합합니다.
핵심 포인트 설명:
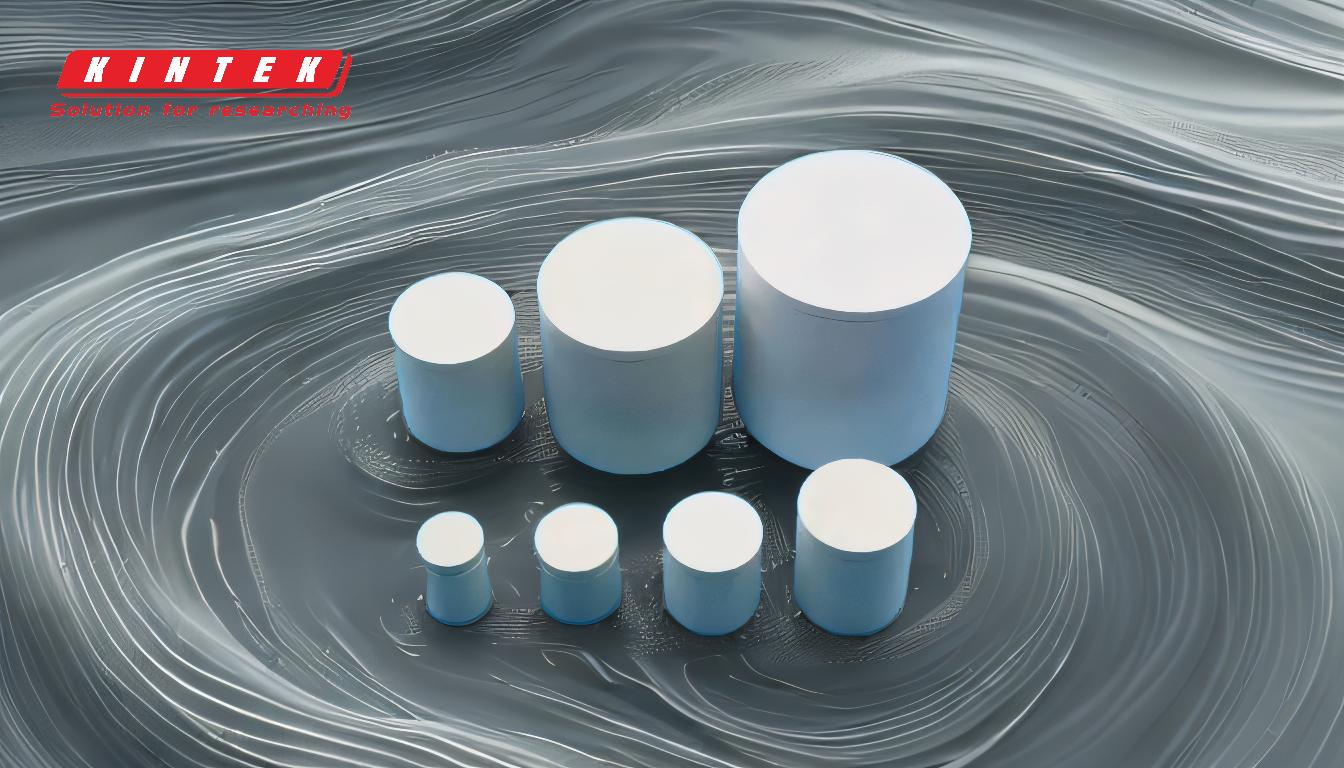
-
플라즈마 질화의 메커니즘과 기존 질화의 메커니즘 비교:
- 플라즈마 질화는 질소 가스를 이온화하여 플라즈마를 생성하고, 이 플라즈마가 공작물 표면을 강타하여 질소가 재료로 확산되도록 합니다.이 공정은 고도로 제어 가능하며 특정 재료 요구 사항에 맞게 조정할 수 있습니다.
- 가스 질화와 같은 전통적인 질화는 고온에서 분해되는 암모니아 가스(NH₃)를 사용하여 질소를 방출한 다음 재료로 확산시킵니다.반면 수조 질화는 질소가 풍부한 화합물이 포함된 용융 소금 용액에 공작물을 담그는 방식입니다.
-
재료 호환성:
- 플라즈마 질화는 다목적이며 특별한 준비나 활성화 단계 없이 스테인리스강을 포함한 모든 철 합금에 적용할 수 있습니다.이는 특정 소재에 대해 추가적인 표면 처리가 필요한 기존 질화에 비해 상당한 장점입니다.
- 기존 질화는 질소 확산을 방해하는 수동 산화물 층이 형성되기 때문에 일부 스테인리스강에는 적합하지 않을 수 있습니다.
-
공정 온도 및 왜곡:
- 플라즈마 질화는 기존 질화 방식에 비해 낮은 온도에서 작동합니다.따라서 열 변형의 위험이 줄어들어 정밀 부품에 이상적입니다.
- 또한 온도가 낮을수록 공작물의 치수 안정성이 더 잘 보존되므로 재작업의 필요성이 최소화됩니다.
-
처리 시간 및 효율성:
- 플라즈마 질화는 플라즈마 환경의 효율적인 질소 확산으로 인해 일반적으로 처리 시간이 더 짧습니다.
- 기존의 질화 공정, 특히 가스 질화는 비슷한 결과를 얻기 위해 더 긴 처리 시간이 필요할 수 있습니다.
-
환경 및 에너지 고려 사항:
- 플라즈마 질화는 유해한 화학 물질을 사용하거나 유해한 부산물을 생성하지 않기 때문에 환경 친화적입니다.또한 작동 온도가 낮고 사이클 시간이 짧아 에너지 효율이 더 높습니다.
- 기존의 질화 방법, 특히 용융 질화는 용융 염을 사용하므로 환경 및 안전 문제가 발생할 수 있습니다.
-
표면 품질 및 재현성:
- 플라즈마 질화로 생성된 층은 취성과 다공성이 낮아 표면 특성이 개선되고 내마모성이 향상됩니다.
- 플라즈마 질화는 공정 파라미터를 정밀하게 제어하여 일관된 결과를 얻을 수 있으므로 재현성이 높습니다.
-
마스킹 및 선택적 처리:
- 플라즈마 질화를 사용하면 나사 구멍이나 처리 후 부드러움을 유지해야 하는 기타 부위를 덮는 등 기계적 방법을 사용하여 특정 부위를 쉽게 마스킹할 수 있습니다.이는 기존 질화 공정에서는 더 까다로운 작업입니다.
요약하면, 플라즈마 질화는 기존 질화 방식보다 더 발전되고 효율적인 대안으로 공정 온도 감소, 왜곡 감소, 처리 시간 단축, 환경 호환성 향상 등의 이점을 제공합니다.특별한 준비 없이 광범위한 재료를 처리할 수 있기 때문에 많은 산업 분야에서 선호되는 방법입니다.
요약 표:
측면 | 플라즈마 질화 | 전통적인 질화 |
---|---|---|
메커니즘 | 이온화된 가스(플라즈마)를 사용하여 질소를 재료로 확산시킵니다. | 기체(예: 암모니아) 또는 액체(예: 용융 소금) 매체에 의존합니다. |
재료 호환성 | 스테인리스강을 포함한 모든 철 합금에 별도의 준비 없이 사용할 수 있습니다. | 스테인리스강과 같은 특정 소재에는 특별한 준비가 필요할 수 있습니다. |
공정 온도 | 온도가 낮을수록 왜곡과 열 스트레스가 줄어듭니다. | 온도가 높을수록 왜곡의 위험이 증가합니다. |
치료 시간 | 효율적인 질소 확산으로 치료 시간 단축. | 비슷한 결과를 얻기 위해 더 긴 처리 시간. |
환경 영향 | 환경 친화적이며 유해 화학물질이나 부산물이 없습니다. | 유해 화학물질(예: 용융염) 및 환경 문제가 발생할 수 있습니다. |
표면 품질 | 덜 부서지기 쉽고 다공성인 레이어를 생성하여 내마모성을 개선합니다. | 공정에 따라 레이어가 더 부서지기 쉽거나 다공성일 수 있습니다. |
재현성 | 프로세스 파라미터를 정밀하게 제어하여 재현성이 높습니다. | 공정 조건의 가변성으로 인해 결과의 일관성이 떨어집니다. |
선택적 처리 | 특정 영역의 선택적 치료를 위한 간편한 마스킹. | 특정 부위를 효과적으로 마스킹하기는 어렵습니다. |
고급 플라즈마 질화로 금속 부품을 개선할 준비가 되셨나요? 지금 바로 문의하세요 에 문의하여 자세히 알아보세요!