고무 몰딩은 경화되지 않은 고무를 금속 캐비티에서 가열하고 모양을 변형하여 기능성 제품으로 만드는 데 사용되는 다목적 제조 공정입니다.고무 성형의 세 가지 주요 유형은 사출 성형, 압축 성형, 트랜스퍼 성형이며, 각각 고유한 접근 방식과 용도가 있습니다.이러한 공정은 컴파운딩, 압출, 캘린더링, 가황, 라텍스 가공 및 폴리우레탄 생산을 포함하는 광범위한 고무 제조 워크플로우의 일부입니다.고무 성형과 관련된 특정 단계와 기술을 이해하는 것은 다양한 산업에 맞는 고품질 고무 제품을 생산하기 위해 필수적입니다.
핵심 사항을 설명합니다:
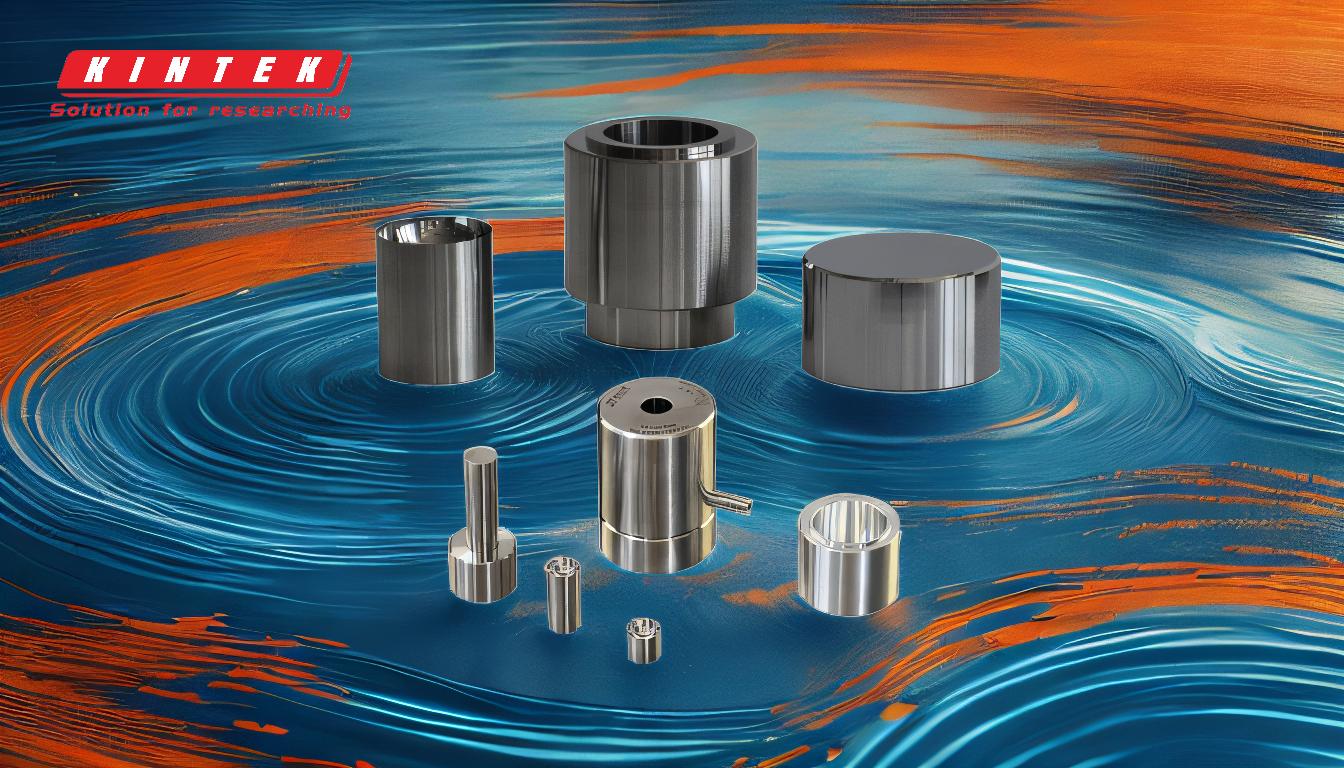
-
고무 성형 개요
- 고무 성형은 경화되지 않은 고무를 금속 주형에서 가열하고 성형하여 사용 가능한 제품으로 바꾸는 공정입니다.
- 압출, 다이컷 시트 압연, 개방형 가황, 연속 가황과 함께 고무 제품을 제조하는 여러 방법 중 하나입니다.
- 이 공정은 내구성이 뛰어나고 유연하며 정밀한 부품을 생산할 수 있기 때문에 자동차, 항공우주, 의료, 소비재 등의 산업에서 널리 사용됩니다.
-
고무 성형 공정의 유형
-
사출 성형:
- 경화되지 않은 고무를 가열된 금형 캐비티에 고압으로 주입합니다.
- 공차가 엄격한 복잡한 형상의 대량 생산에 이상적입니다.
- 씰, 개스킷, 오링에 주로 사용됩니다.
-
압축 성형:
- 미리 측정된 고무를 열린 금형 캐비티에 넣은 다음 닫고 압력을 가하여 가열합니다.
- 크고 단순한 부품 및 중저가 생산량에 적합합니다.
- 부싱 및 마운트와 같은 자동차 부품에 자주 사용됩니다.
-
트랜스퍼 몰딩:
- 플런저를 사용하여 챔버에서 밀폐된 몰드 캐비티로 고무를 이송합니다.
- 사출 성형과 압축 성형의 요소를 결합하여 정밀성과 단순성의 균형을 제공합니다.
- 일관된 재료 분배가 필요한 복잡한 부품에 자주 사용됩니다.
-
사출 성형:
-
고무 성형 공정의 주요 단계
-
재료 준비:
- 고무 컴파운드는 원료 고무와 필러, 가소제, 경화제 등의 첨가제를 혼합하여 제조합니다.
- 이 단계를 통해 탄성, 강도, 열 또는 화학 물질에 대한 내성 등 원하는 특성을 갖춘 고무를 만들 수 있습니다.
-
금형 설계 및 준비:
- 금형은 제품의 사양에 따라 맞춤 설계됩니다.
- 일반적으로 고온과 압력을 견딜 수 있도록 강철이나 알루미늄과 같은 내구성 있는 소재로 만들어집니다.
-
성형 공정:
- 선택한 성형 방법(사출, 압축 또는 전사)을 사용하여 고무를 성형합니다.
- 열과 압력을 가하여 고무를 경화시켜 원하는 형태로 굳힙니다.
-
후처리:
- 성형 후 고무 제품은 트리밍, 표면 마감 또는 품질 검사와 같은 추가 단계를 거칠 수 있습니다.
- 이러한 단계를 통해 제품이 필요한 사양 및 성능 표준을 충족하는지 확인합니다.
-
재료 준비:
-
고무 성형의 장점
- 다용도성:다양한 모양, 크기 및 복잡성을 생성할 수 있습니다.
- 내구성:고무 제품은 마모, 찢어짐 및 환경적 요인에 강합니다.
- 비용 효율성:사용 방법에 따라 대량 생산 및 소량 생산 모두에 적합합니다.
- 정밀도:특히 사출 성형 시 일관된 품질과 엄격한 공차를 보장합니다.
-
고무 성형의 응용 분야
- 자동차:씰, 개스킷, 진동 댐퍼 및 호스.
- 의료:주사기 마개, 씰 및 의료 기기 구성품.
- 소비재:신발, 그립 및 보호 커버.
- 산업:개스킷, 씰 및 방진 부품.
고무 성형의 유형, 단계, 적용 분야를 포함한 제조 공정을 이해함으로써 장비 및 소모품 구매자는 특정 요구 사항에 가장 적합한 방법과 재료에 대해 정보에 입각한 결정을 내릴 수 있습니다.이러한 지식은 산업 표준 및 성능 요구 사항을 충족하는 고품질 고무 제품을 생산할 수 있도록 보장합니다.
요약 표:
측면 | 세부 정보 |
---|---|
몰딩 유형 | 주입, 압축, 전송 |
주요 단계 | 재료 준비, 금형 설계, 성형 공정, 후가공 |
장점 | 다용도성, 내구성, 비용 효율성, 정밀도 |
애플리케이션 | 자동차, 의료, 소비재, 산업 |
고무 성형으로 생산 요구 사항을 충족하는 방법을 알아보세요. 지금 바로 전문가에게 문의하세요 !