디바인딩은 테크니컬 세라믹 및 3D 프린팅 부품 제조에서 중요한 단계로, 그린 바디에서 유기 바인더나 캐리어 재료를 제거하는 작업을 포함합니다. 이 공정을 통해 최종 제품에는 소결 중 구조적 완전성에 영향을 미칠 수 있는 오염 물질이 없음을 보장합니다. 탈지 작업은 열적 또는 화학적 방법을 통해 달성할 수 있으며, 온도, 가스 분위기 및 시간을 정밀하게 제어해야 하는 경우가 많습니다. 이 공정은 일반적으로 산소 수준을 낮추기 위해 질소 퍼지로 시작하고, 이어서 바인더를 점진적으로 분해하는 가열 사이클이 이어집니다. 미량이라도 소결 단계를 손상시킬 수 있으므로 완전한 바인더 제거를 보장하려면 용광로를 여러 번 통과해야 할 수 있습니다. 탈지 기간은 부품 형상 및 바인더 구성과 같은 요인에 따라 달라지며, 최대 24~36시간이 소요되는 경우도 있습니다.
설명된 핵심 사항:
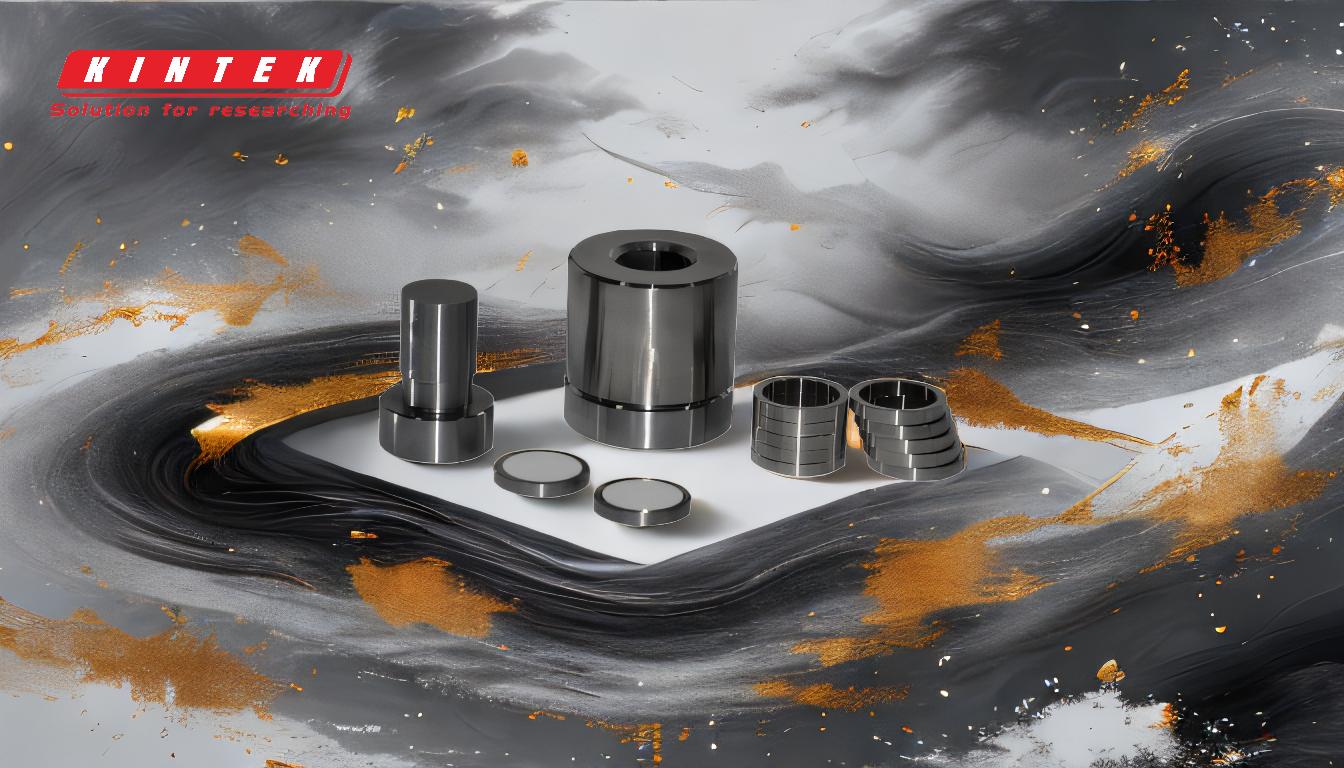
-
디바인딩의 목적:
- 디바인딩은 3D 프린팅 부품이나 기술 세라믹의 녹색 몸체에서 유기 바인더나 캐리어 재료를 제거합니다.
- 최종 제품에 재료의 밀도를 높이는 공정인 소결을 방해할 수 있는 오염 물질이 없는지 확인합니다.
-
디바인딩 방법:
- 열탈지: 결합제를 분해하기 위해 용광로에서 부품을 가열하는 과정이 포함됩니다. 온도 범위는 일반적으로 150°C ~ 600°C(300°F ~ 1110°F)입니다.
- 화학적 탈지: 바인더를 용해시키기 위해 용제를 사용하며, 보다 복잡한 부품의 경우 열적 방법과 결합하는 경우가 많습니다.
-
프로세스 단계:
- 질소 퍼지: 산화를 방지하고 통제된 환경을 보장하기 위해 용광로 내 산소 함량을 줄이는 것부터 시작됩니다.
-
가열주기: 부품은 바인더를 분해하기 위해 종종 여러 단계로 점진적으로 가열됩니다. 예를 들어:
- 2°C/분 속도로 225°C까지 가열합니다.
- 1°C/분 속도로 550°C까지 증가시키고 2시간 동안 유지합니다.
- 6°C/min의 속도로 1,300°C까지 추가 가열하며 유지 시간은 40~180분입니다.
- 냉각: 부품을 분당 6°C의 속도로 600°C까지 냉각한 후 노에서 추가로 냉각시킵니다.
-
탈결합에 영향을 미치는 요인:
- 부품 형상: 복잡한 형상은 바인더를 완전히 제거하기 위해 더 긴 탈지 시간이 필요할 수 있습니다.
- 바인더 구성: 다양한 바인더는 다양한 온도에서 분해되므로 맞춤형 가열 프로필이 필요합니다.
- 용광로 분위기: 제어된 가스 환경(예: 질소)은 뒤틀림이나 균열과 같은 결함을 방지하는 데 중요합니다.
-
과제 및 고려 사항:
- 추적 바인더 잔류물: 소량의 잔여 바인더라도 소결 단계를 오염시킬 수 있으므로 여러 번의 퍼니스 통과가 필요합니다.
- 결함 예방: 뒤틀림, 균열 등의 불량을 방지하기 위해서는 온도, 압력, 가스분위기의 세심한 관리가 필수적입니다.
- 시간 강도: 디바인딩은 부품 및 바인더 유형에 따라 최대 24~36시간이 소요될 수 있습니다.
-
소결과의 통합:
- 탈지 작업은 치밀화를 위해 부품을 고온으로 가열하는 소결을 포함하는 대규모 공정의 일부인 경우가 많습니다.
- 탈지 및 소결 공정은 밀접하게 연결되어 있으므로 부품 무결성을 보장하려면 온도 사이클 간의 원활한 전환이 필요합니다.
이러한 핵심 사항을 이해함으로써 장비 및 소모품 구매자는 탈지 공정에 대한 요구 사항을 더 잘 평가하고 특정 응용 분야에 적합한 재료와 장비를 선택할 수 있습니다.
요약표:
측면 | 세부 |
---|---|
목적 | 소결 오염을 방지하기 위해 유기 바인더를 제거합니다. |
행동 양식 | 열(150°C~600°C) 또는 화학적 탈지. |
프로세스 단계 | 질소 퍼지, 가열 주기, 냉각. |
주요 요인 | 부품 형상, 바인더 구성, 로 분위기. |
도전과제 | 미량 잔류물, 결함 방지, 시간 집약적(24~36시간). |
완성 | 치밀화를 위한 소결과 밀접하게 연관되어 있습니다. |
완벽한 소결을 위해 탈지 공정을 최적화하세요. 지금 전문가에게 문의하세요 !