PVD(물리적 기상 증착) 코팅은 다양한 기판에 얇고 밀착력이 높으며 내구성이 뛰어난 코팅을 적용하는 데 사용되는 정교한 공정입니다.이 공정에는 기판의 세척 및 전처리, 대상 물질의 기화, 기화된 원자의 운반, 가스와의 반응(필요한 경우), 기판 위에 증착 등 몇 가지 주요 단계가 포함됩니다.그 결과 기본 재료와 상호 침투하는 미크론 두께의 층이 형성되어 뛰어난 접착력과 박리 또는 칩핑에 대한 저항성을 제공합니다.이 공정은 아르곤과 같은 불활성 가스를 사용하는 진공 환경에서 진행되어 화학적으로 반응하지 않는 분위기를 보장하므로 코팅의 품질과 내구성이 향상됩니다.
핵심 포인트 설명:
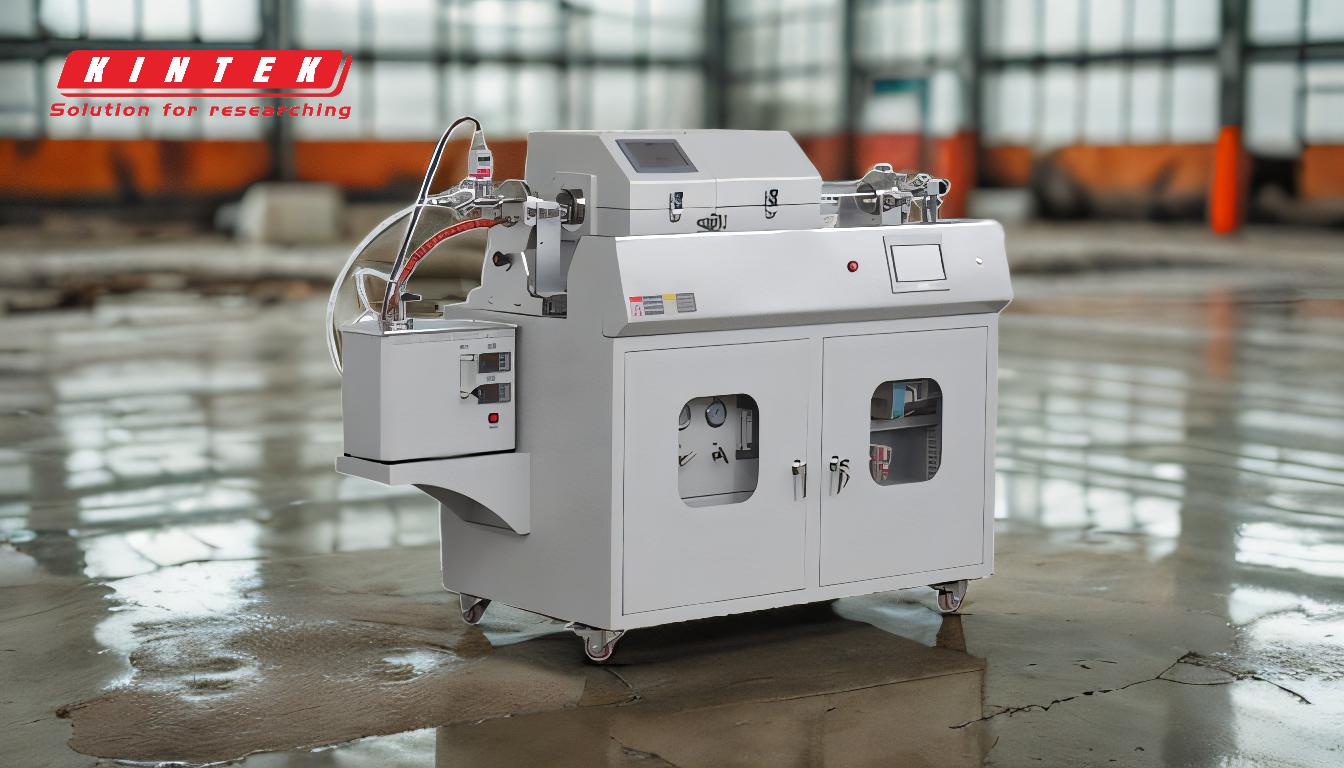
-
기판의 청소 및 전처리:
- 청소: 인쇄물은 기름, 먼지 또는 산화물과 같은 오염 물질을 제거하기 위해 철저히 청소해야 합니다.표면의 불순물이 코팅의 접착력과 품질에 부정적인 영향을 미칠 수 있으므로 이는 매우 중요합니다.세척 방법에는 초음파 세척, 화학 세척 또는 플라즈마 세척이 포함될 수 있습니다.
- 전처리: 세척 후 기판은 코팅 접착력을 향상시키기 위해 전처리 공정을 거치는 경우가 많습니다.여기에는 표면 거칠기, 이온 충격 또는 프라이머 층 적용이 포함될 수 있습니다.전처리는 표면이 코팅을 받을 수 있도록 화학적, 물리적으로 준비되도록 합니다.
-
대상 재료의 기화:
- 증발/증발: 코팅의 소스인 대상 물질을 진공 챔버에 넣습니다.전자, 이온 또는 레이저와 같은 고에너지 소스를 사용하여 대상 물질에 충격을 가하여 기화시킵니다.이 과정을 통해 고체 표적 물질이 증기상으로 전환됩니다.
- 운송: 기화된 원자 또는 분자는 진공 챔버를 통해 기판 쪽으로 운반됩니다.진공 환경은 기화된 입자가 공기 분자의 간섭 없이 이동하도록 보장하여 보다 제어되고 균일한 증착을 가능하게 합니다.
-
가스와의 반응(필요한 경우):
- 반응: 경우에 따라 기화된 원자는 챔버로 유입된 질소, 산소 또는 메탄과 같은 선택된 가스와 반응합니다.이 반응은 금속 산화물, 질화물 또는 탄화물과 같은 화합물을 형성하여 경도, 색상 및 내화학성과 같은 코팅의 최종 특성을 결정합니다.
- 반응 조건 제어: 가스 조성, 압력, 온도 등 반응 조건은 원하는 코팅 특성을 얻기 위해 세심하게 제어됩니다.예를 들어 질소 가스를 도입하면 경도와 내마모성으로 잘 알려진 금속 질화물이 형성될 수 있습니다.
-
기판에 증착:
- 응축: 기화된 원자 또는 분자가 기판 표면에 응축되어 박막을 형성합니다.증착 공정은 균일한 적용 범위와 두께를 보장하기 위해 제어됩니다.코팅이 한 층씩 쌓여 기판과 강력하게 결합합니다.
- 접착력: 코팅이 기본 소재와 상호 침투하여 강력한 결합을 형성하여 박리 또는 칩핑을 방지합니다.이는 뛰어난 접착력과 내구성을 제공하는 PVD 코팅의 주요 장점 중 하나입니다.
-
품질 관리 및 마감:
- 품질 관리: 증착 후 코팅된 기판은 품질 관리 검사를 거쳐 코팅이 필요한 사양을 충족하는지 확인합니다.여기에는 두께, 경도, 접착력 및 표면 거칠기 측정이 포함될 수 있습니다.모든 결함이나 불일치가 식별되고 해결됩니다.
- 마무리: 적용 분야에 따라 코팅된 기판은 외관이나 성능을 향상시키기 위해 추가적인 마감 공정을 거칠 수 있습니다.여기에는 연마, 어닐링 또는 내식성 또는 미적 매력을 개선하기 위한 탑코트 적용이 포함될 수 있습니다.
-
불활성 가스 사용:
- 불활성 대기: PVD 공정 전반에 걸쳐 아르곤과 같은 불활성 가스를 사용하여 화학적으로 반응하지 않는 분위기를 조성합니다.이는 코팅 재료와 환경 사이의 원치 않는 반응을 방지하여 코팅의 순도와 품질을 보장합니다.또한 불활성 가스는 증착 공정이 완료된 후 챔버에서 잔류 증기를 제거하는 데 도움이 됩니다.
-
진공 환경:
-
고진공 조건:
전체 PVD 공정은 고진공 환경에서 진행됩니다.이는 여러 가지 이유로 필수적입니다:
- 오염 최소화: 진공은 코팅 공정을 방해할 수 있는 오염 물질의 존재를 줄여줍니다.
- 제어된 증착: 진공을 통해 증착 공정을 정밀하게 제어할 수 있어 균일하고 고품질의 코팅을 보장합니다.
- 에너지 효율: 진공 환경은 에너지 손실을 최소화하여 프로세스를 더욱 효율적으로 만듭니다.
-
고진공 조건:
전체 PVD 공정은 고진공 환경에서 진행됩니다.이는 여러 가지 이유로 필수적입니다:
-
애플리케이션 및 이점:
- 광범위한 적용 분야: PVD 코팅은 자동차, 항공우주, 의료 기기, 가전제품 등 다양한 산업 분야에서 사용됩니다.부품의 성능, 내구성 및 미관을 향상시키는 능력으로 높은 평가를 받고 있습니다.
- 이점: PVD 코팅은 높은 경도, 내마모성, 내식성, 장식적인 마감 처리 기능 등 다양한 이점을 제공합니다.또한 유해한 화학 물질을 사용하거나 유해 폐기물을 생성하지 않기 때문에 환경 친화적입니다.
요약하면, PVD 코팅 공정은 다양한 기판에 얇고 내구성이 뛰어나며 밀착력이 높은 코팅을 적용하기 위한 고도로 제어되고 정밀한 방법입니다.세척 및 전처리부터 증착 및 품질 관리에 이르기까지 공정의 각 단계를 이해하면 고성능 PVD 코팅을 만드는 데 수반되는 복잡성과 정교함을 이해할 수 있습니다.
요약 표:
단계 | 설명 |
---|---|
세척 및 전처리 | 오염 물질을 제거하고 더 나은 접착력을 위해 기판을 준비합니다. |
기화 | 진공 챔버에서 고에너지원을 사용하여 대상 물질을 기화시킵니다. |
기체와의 반응 | 기화된 원자는 기체와 반응하여 질화물이나 탄화물과 같은 화합물을 형성합니다. |
증착 | 기화된 원자가 기판에 응축되어 얇고 내구성 있는 코팅을 형성합니다. |
품질 관리 | 코팅이 두께, 경도 및 접착력에 대한 사양을 충족하는지 확인합니다. |
불활성 가스 | 아르곤 또는 기타 불활성 가스는 고품질 코팅을 위해 화학적으로 반응하지 않는 분위기를 조성합니다. |
진공 환경 | 고진공 조건은 오염을 최소화하고 정밀하고 균일한 증착을 보장합니다. |
응용 분야 | 자동차, 항공우주, 의료 기기, 가전 제품에서 성능 향상을 위해 사용됩니다. |
장점 | 높은 경도, 내마모성, 내식성 및 장식적인 마감 처리. |
PVD 코팅으로 부품을 강화할 준비가 되셨나요? 지금 바로 문의하세요 에 문의하여 자세히 알아보세요!