웨이퍼 제조의 증착은 반도체 산업에서 중요한 공정으로, 기판에 고품질의 박막과 고체 물질을 만드는 데 사용됩니다. 이 공정은 일반적으로 램프 업, 에칭, 코팅, 램프 다운의 네 가지 주요 단계로 구성됩니다. 램프 업 단계에서는 온도와 압력을 조정하여 챔버를 준비합니다. 에칭은 접착력을 높이기 위해 기판을 청소하고, 코팅은 원하는 재료를 기판에 투사하는 과정을 거칩니다. 마지막으로 램프 다운을 통해 챔버를 주변 조건으로 되돌립니다. 재료와 애플리케이션 요구 사항에 따라 LPCVD, PECVD, ALD, PVD 등 다양한 증착 기술이 사용됩니다. 알루미늄과 텅스텐과 같은 재료가 일반적으로 사용되며, 정밀한 증착을 보장하는 HDP-CVD 및 플라즈마 강화 CVD와 같은 기술이 사용됩니다.
핵심 사항 설명:
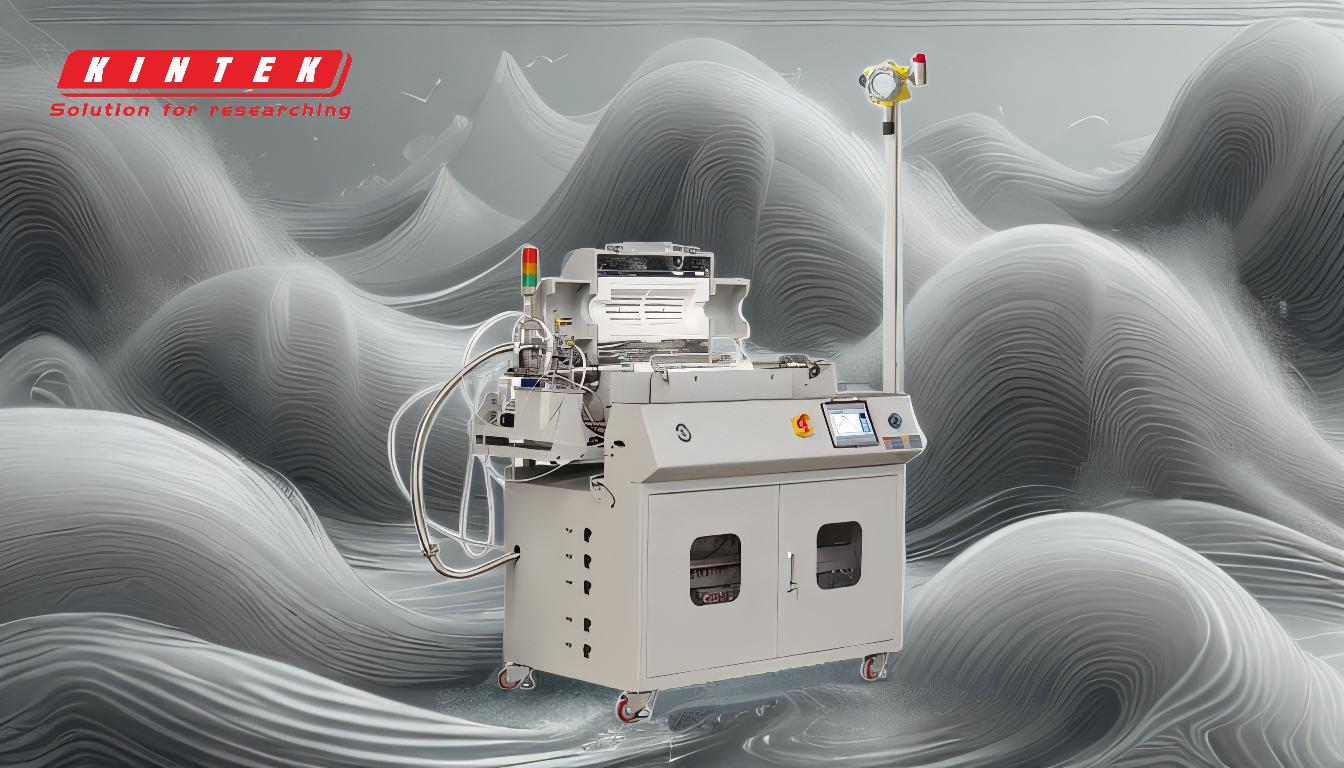
-
웨이퍼 제조의 증착 개요
- 증착은 반도체 제조의 기본 공정으로, 기판(일반적으로 실리콘 웨이퍼)에 박막 또는 재료 층을 만드는 데 사용됩니다.
- 이러한 층은 집적 회로 및 기타 반도체 장치를 구성하는 기초를 형성합니다.
- 이 공정은 고품질의 고성능 재료가 균일하고 정밀하게 증착되도록 보장합니다.
-
증착의 네 가지 주요 단계
-
램프 업:
- 챔버는 온도를 서서히 높이고 압력을 낮추어 제어된 환경을 조성하여 준비됩니다.
- 이 단계를 통해 기판과 챔버가 증착 공정을 위한 준비가 완료됩니다.
-
에칭:
- 플라즈마 에칭은 기판 표면을 청소하고 오염 물질을 제거하며 증착된 재료의 접착력을 향상시키는 데 사용됩니다.
- 이 단계는 증착된 층의 품질과 신뢰성을 보장하는 데 매우 중요합니다.
-
코팅:
- 증착할 재료는 스퍼터링, 증착 또는 화학 반응과 같은 기술을 사용하여 기판에 투영됩니다.
- 기술 선택은 재료와 필름의 원하는 특성에 따라 달라집니다.
-
램프 다운:
- 증착 후 챔버는 서서히 냉각되어 주변 압력으로 되돌아갑니다.
- 이 단계는 열 스트레스를 방지하고 증착된 층의 안정성을 보장합니다.
-
램프 업:
-
일반적인 증착 기술
-
화학 기상 증착(CVD):
- 저압 CVD(LPCVD), 플라즈마 강화 CVD(PECVD), 대기압 이하 CVD(SACVD)가 포함됩니다.
- CVD는 이산화규소, 질화규소 또는 텅스텐과 같은 재료를 증착하기 위한 화학 반응을 포함합니다.
-
원자층 증착(ALD):
- 재료를 한 층씩 증착하여 균일한 두께와 높은 적합성을 보장하는 정밀한 기술입니다.
-
물리적 기상 증착(PVD):
- 스퍼터링 또는 증착과 같은 기술을 사용하여 알루미늄이나 구리와 같은 금속을 증착합니다.
-
에피택셜 증착(Epi):
- 기판 위에 결정층을 성장시키는 데 사용되며, 주로 고성능 반도체 재료를 만드는 데 사용됩니다.
-
화학 기상 증착(CVD):
-
증착에 사용되는 재료
-
알루미늄:
- 일반적으로 반도체 소자의 주요 전도성 층에 사용됩니다.
-
텅스텐:
- 높은 전도성과 내구성으로 인해 인터커넥트 및 접점에 CVD 기술을 사용하여 증착됩니다.
-
실리콘 기반 재료:
- 절연 및 패시베이션 층을 위해 이산화규소와 질화규소가 증착됩니다.
-
다이아몬드 유사 탄소(DLC):
- 높은 경도와 내마모성이 요구되는 특수 용도에 사용됩니다.
-
알루미늄:
-
증착의 응용 분야와 중요성
- 증착은 최신 반도체 소자의 복잡한 층과 구조를 만드는 데 필수적입니다.
- 이를 통해 디바이스 기능에 중요한 트랜지스터, 인터커넥트 및 절연층을 생산할 수 있습니다.
- 증착 공정의 품질은 반도체 소자의 성능, 신뢰성, 수율에 직접적인 영향을 미칩니다.
-
증착 공정에 영향을 미치는 요인
-
온도 및 압력:
- 균일한 증착을 보장하고 결함을 방지하려면 정밀한 제어가 필요합니다.
-
기판 준비:
- 강력한 접착력과 고품질 필름을 얻기 위해서는 세척과 에칭이 중요합니다.
-
재료 특성:
- 증착 기술의 선택은 융점 및 반응성과 같은 재료의 특성에 따라 달라집니다.
-
온도 및 압력:
-
증착의 도전 과제
- 대형 웨이퍼에서 균일한 두께 달성.
- 보이드, 균열 또는 불순물과 같은 결함 최소화.
- 리소그래피 및 에칭과 같은 후속 처리 단계와의 호환성 보장.
반도체 제조업체는 증착 공정과 주요 구성 요소를 이해함으로써 제조 공정을 최적화하여 고성능 디바이스를 효율적으로 생산할 수 있습니다.
요약 표:
측면 | 세부 사항 |
---|---|
주요 단계 | 램프 업, 에칭, 코팅, 램프 다운 |
공통 기술 | LPCVD, PECVD, ALD, PVD, 에피택셜 증착 |
사용 재료 | 알루미늄, 텅스텐, 이산화규소, 질화규소, 다이아몬드 유사 탄소 |
응용 분야 | 트랜지스터, 인터커넥트, 절연층 |
도전 과제 | 균일한 두께, 결함 최소화, 다른 공정과의 호환성 |
전문가의 인사이트를 통해 웨이퍼 제조 공정을 최적화하세요. 지금 문의하세요 !