스파크 플라즈마 소결(SPS) 은 일축 압력과 펄스 직류(DC)를 결합하여 분말을 조밀하고 균질한 재료로 빠르게 응집시키는 최신 소결 기술입니다.이 공정은 기존 소결 방식에 비해 속도와 효율성이 뛰어나고 낮은 온도에서 고밀도화를 달성할 수 있다는 특징이 있습니다.SPS의 주요 단계에는 가스 제거 및 진공 생성, 압력 가하기, 저항 가열 및 냉각이 포함됩니다.각 단계는 분말 입자의 성공적인 치밀화 및 결합을 보장하는 데 중요한 역할을 합니다.이 공정은 플라즈마 방전, 줄 가열 및 소성 변형을 활용하여 빠른 가열, 입자 결합 및 재료 통합을 달성합니다.
핵심 포인트 설명:
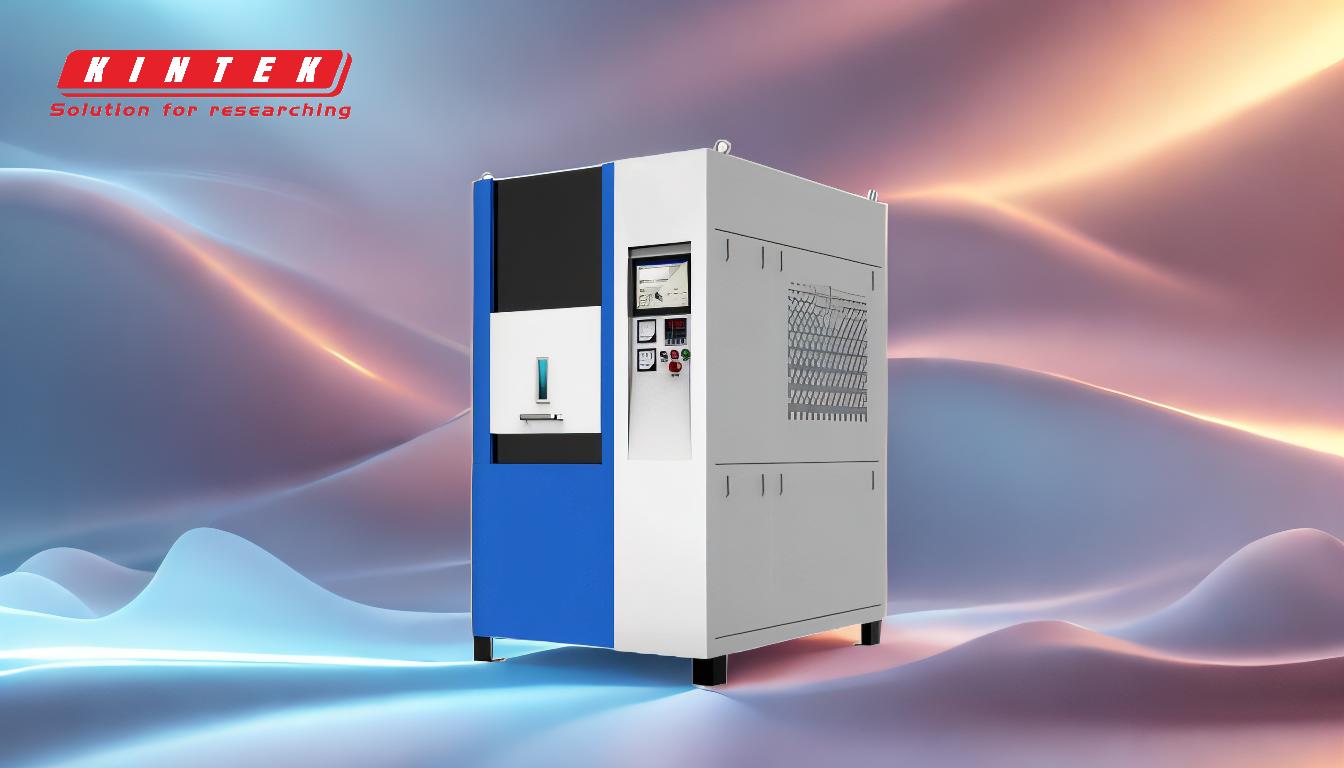
-
가스 제거 및 진공 생성
- SPS의 첫 번째 단계는 소결 챔버에서 가스를 제거하고 진공 또는 제어된 분위기를 조성하는 것입니다.
- 이는 분말 재료의 산화와 오염을 방지하여 최종 제품의 순도와 품질을 보장하는 데 매우 중요합니다.
- A 진공 환경 은 또한 후속 단계에서 열 전달과 플라즈마 생성을 더 원활하게 합니다.
-
압력 적용
- 일반적으로 다음과 같이 만들어진 금형 내의 분말 재료에 일축 압력이 가해집니다. 흑연 .
- 압력은 분말 입자를 압축하여 입자 사이의 간격을 줄이고 소결 시 더 나은 접촉을 촉진하는 데 도움이 됩니다.
- 또한 가해진 압력은 입자의 소성 변형을 도와 고밀도화를 달성하는 데 필수적인 역할을 합니다.
-
저항 가열
- 펄스 DC 전류는 흑연 다이를 통과하고, 전도성인 경우 파우더 재료 자체를 통과합니다.
- 이렇게 하면 입자 사이에 국부적인 고온과 플라즈마 방전이 발생하여 빠른 가열이 이루어집니다.
-
이 과정에는 세 가지 가열 메커니즘이 포함됩니다:
- 플라즈마 가열:입자 사이의 방전은 플라즈마를 생성하여 표면 확산과 결합을 촉진합니다.
- 줄 가열:재료 내 전기 저항이 열을 발생시켜 소결을 더욱 촉진합니다.
- 소성 변형:열과 압력의 조합으로 입자가 변형되고 계면에서 결합합니다.
- 이러한 메커니즘을 통해 기존 방식에 비해 훨씬 낮은 온도와 짧은 시간으로 소결할 수 있습니다.
-
냉각 단계
- 소결 공정이 끝나면 재료는 실온으로 빠르게 냉각됩니다.
- 급속 냉각은 소결된 재료의 미세 구조와 특성을 보존하는 데 도움이 됩니다.
- 최종 제품의 열 응력이나 균열을 방지하기 위해 냉각 속도를 제어합니다.
-
SPS의 장점
- 속도:SPS는 기존 방법보다 훨씬 짧은 시간 내에 소결 공정을 완료합니다.
- 낮은 온도:SPS는 기존 소결보다 수백도 낮은 온도에서 치밀화를 달성합니다.
- 향상된 재료 특성:빠른 가열 및 냉각 속도로 미세한 미세 구조와 향상된 기계적 특성을 얻을 수 있습니다.
- 다용도성:SPS는 세라믹, 금속, 복합재 등 다양한 소재에 사용할 수 있습니다.
-
SPS의 응용 분야
- SPS는 나노 구조 세라믹, 기능 등급 재료, 복합재와 같은 첨단 재료의 제조에 널리 사용됩니다.
- 특히 항공우주, 자동차, 전자 등 미세 구조와 특성을 정밀하게 제어할 수 있는 고성능 소재를 필요로 하는 산업에서 유용합니다.
다음 단계를 따르세요, 스파크 플라즈마 소결 은 우수한 특성을 지닌 고품질의 고밀도 소재를 생산할 수 있어 고급 소재 제작에 선호되는 기술입니다.
요약 표:
단계 | 주요 세부 정보 |
---|---|
가스 제거 및 진공 | 가스를 제거하고 산화를 방지하며 제어된 분위기를 보장합니다. |
압력 적용 | 파우더 입자를 압축하고 간격을 줄이며 소성 변형을 돕습니다. |
저항 가열 | 플라즈마 방전, 줄 가열 및 빠른 입자 결합을 위해 펄스 DC를 사용합니다. |
냉각 단계 | 빠른 냉각으로 미세 구조를 보존하고 열 스트레스를 방지합니다. |
장점 | 속도, 낮은 온도, 향상된 특성, 다양한 소재를 사용할 수 있습니다. |
애플리케이션 | 항공우주, 자동차, 전자, 첨단 소재 제조. |
스파크 플라즈마 소결로 소재 제조 공정을 혁신하는 방법을 알아보세요. 지금 문의하세요 !