사출 성형과 인서트 성형은 플라스틱 부품을 만드는 데 사용되는 두 가지 제조 공정으로, 각각 고유한 응용 분야와 장점이 있습니다.사출 성형은 용융된 플라스틱을 금형 캐비티에 주입하여 부품을 형성하는 반면, 인서트 성형은 미리 성형된 인서트(주로 금속)를 금형에 넣고 그 주위에 플라스틱을 주입하는 방식입니다.주요 차이점은 인서트 몰딩에는 표준 사출 성형에는 사용되지 않는 인서트가 있다는 것입니다.관련 공정인 오버몰딩은 두 번의 재료 사출을 통해 기판과 오버몰드를 만들지만, 단일 공정에서 여러 재료를 사용한다는 점에서 인서트 몰딩과 다릅니다.
핵심 사항을 설명합니다:
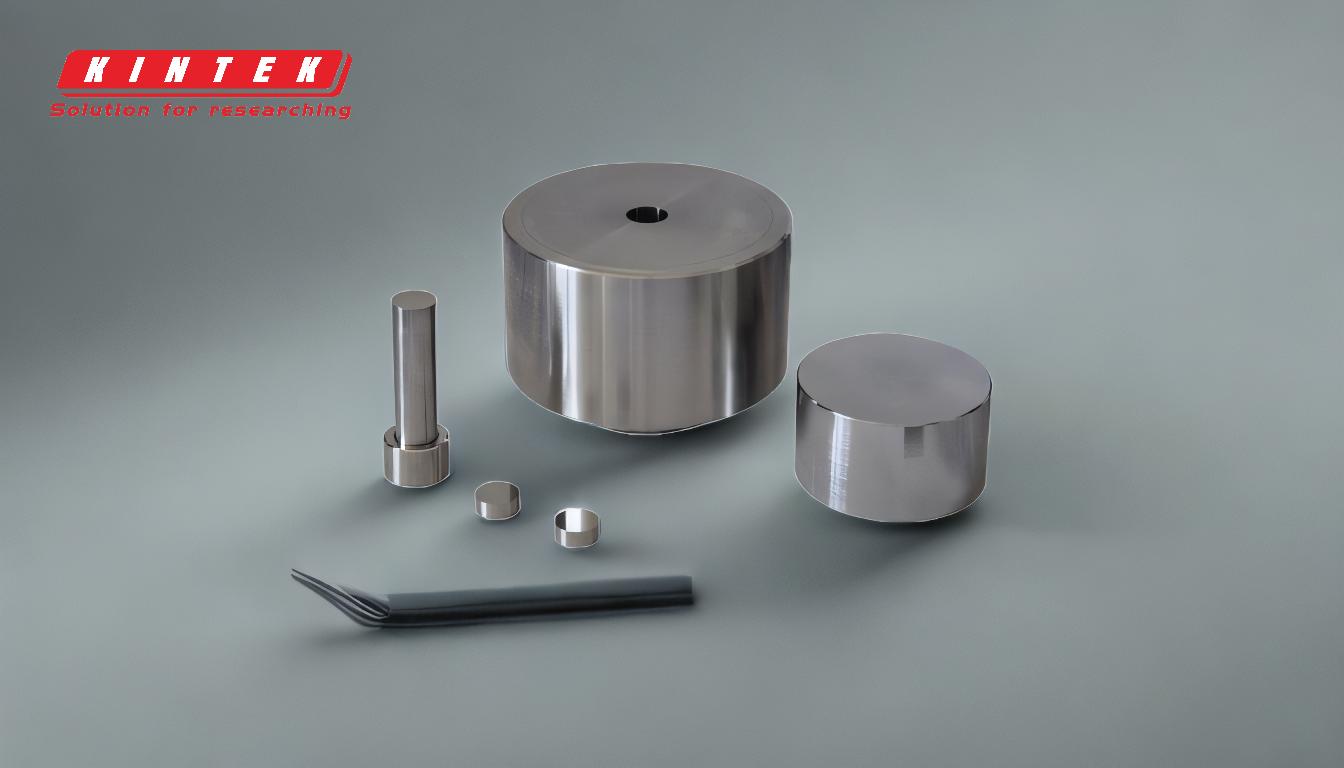
-
정의 및 프로세스:
- 사출 성형:용융된 플라스틱을 고압으로 금형 캐비티에 주입하는 제조 공정입니다.플라스틱이 식고 굳으면 금형이 열리고 부품이 배출됩니다.단일 재료 공정으로 다양한 플라스틱 부품을 생산하는 데 널리 사용됩니다.
- 인서트 몰딩:이 공정에서는 플라스틱을 사출하기 전에 미리 성형된 인서트(주로 금속으로 제작됨)를 금형에 넣습니다.그런 다음 용융된 플라스틱이 인서트 주위를 흐르며 식으면서 인서트와 결합합니다.이 공정은 나사산 인서트나 전기 커넥터와 같이 플라스틱과 금속의 특성을 결합한 부품을 만드는 데 사용됩니다.
-
사용되는 재료:
- 사출 성형:일반적으로 한 가지 유형의 플라스틱 소재를 사용합니다.재료는 강도, 유연성 또는 내열성 등 최종 부품의 원하는 특성에 따라 선택됩니다.
- 인서트 몰딩:플라스틱과 금속, 세라믹 또는 다른 재질로 만들어진 사전 성형된 인서트가 모두 포함됩니다.플라스틱은 인서트와 잘 접착되도록 선택되어 견고하고 내구성이 뛰어난 최종 제품을 보장합니다.
-
애플리케이션:
- 사출 성형:일반적으로 소비재, 자동차 부품, 의료 기기 등 다양한 플라스틱 부품 생산에 사용됩니다.효율성과 반복성이 뛰어나 대량 생산에 이상적입니다.
- 인서트 몰딩:전자 부품, 의료 기기 및 자동차 부품 생산과 같이 다양한 재료의 조합이 필요한 분야에 사용됩니다.금속 보강 또는 특정 기계적 특성이 필요한 부품을 제작할 때 특히 유용합니다.
-
장점:
-
사출 성형:
- 높은 생산 효율성과 반복성.
- 복잡한 형상을 높은 정밀도로 생산할 수 있습니다.
- 대량 생산에 비용 효율적입니다.
-
인서트 몰딩:
- 플라스틱과 금속의 장점을 결합하여 강도와 내구성이 강화된 부품을 제작할 수 있습니다.
- 인서트가 부품에 직접 성형되므로 2차 조립 작업의 필요성이 줄어듭니다.
- 다양한 소재를 통합하여 부품의 전반적인 성능을 향상시킬 수 있습니다.
-
사출 성형:
-
도전 과제:
-
사출 성형:
- 단일 소재 부품으로 제한되어 특정 애플리케이션의 요구 사항을 충족하지 못할 수 있습니다.
- 높은 초기 툴링 비용으로 인해 소규모 생산에 장애가 될 수 있습니다.
-
인서트 몰딩:
- 인서트를 정밀하게 배치해야 하므로 성형 공정이 복잡해질 수 있습니다.
- 인서트는 플라스틱 소재와 호환되어야 제대로 접착할 수 있습니다.
- 인서트에 대한 추가 비용과 더 복잡한 금형 설계가 필요할 수 있습니다.
-
사출 성형:
-
오버몰딩과 비교:
- 오버몰딩:이 공정은 두 개의 재료를 사출하여 기판과 오버몰드를 만드는 과정입니다.서로 다른 재료를 결합한다는 점에서 인서트 몰딩과 유사하지만, 한 번의 공정으로 한 재료를 다른 재료 위에 성형하는 방식으로 진행됩니다.오버몰딩은 부드러운 그립, 다양한 색상의 부품 또는 다양한 재료 특성을 가진 부품을 제작하는 데 자주 사용됩니다.
- 인서트 몰딩:오버몰딩과 달리 인서트 몰딩은 플라스틱 소재와 미리 성형된 인서트를 한 번에 사출하는 방식입니다.인서트는 성형되지 않고 플라스틱이 사출되기 전에 금형에 배치됩니다.이 공정은 여러 플라스틱을 겹겹이 쌓는 것이 아니라 플라스틱과 금속 등 다른 재료를 결합하는 데 더 중점을 둡니다.
-
디자인 고려 사항:
- 사출 성형:설계자는 벽 두께, 게이트 위치 및 구배 각도와 같은 요소를 고려하여 적절한 금형 충진 및 부품 배출을 보장해야 합니다.
- 인서트 몰딩:추가 고려 사항으로는 인서트의 배치와 디자인, 인서트와 플라스틱 소재 간의 결합이 있습니다.인서트는 성형 공정을 견디고 원하는 기계적 특성을 제공하도록 설계되어야 합니다.
요약하면, 사출 성형과 인서트 성형은 모두 플라스틱 부품을 만드는 데 사용되지만 서로 다른 용도로 사용되며 다양한 응용 분야에 적합합니다.사출 성형은 대량으로 생산되는 단일 소재 부품에 이상적이며, 인서트 성형은 성능을 향상시키기 위해 플라스틱과 금속 등 다른 소재를 결합한 부품을 제작하는 데 사용됩니다.이러한 공정 간의 차이점을 이해하는 것은 주어진 애플리케이션에 적합한 제조 방법을 선택하는 데 매우 중요합니다.
요약 표:
측면 | 사출 성형 | 인서트 몰딩 |
---|---|---|
프로세스 | 용융된 플라스틱을 금형 캐비티에 주입합니다. | 미리 성형된 인서트를 금형에 배치한 후 주위에 플라스틱을 주입합니다. |
재료 | 단일 플라스틱 소재. | 플라스틱과 사전 성형된 인서트(예: 금속)가 결합된 형태. |
애플리케이션 | 소비재, 자동차 부품, 의료 기기. | 전자 부품, 의료 기기, 금속 보강재가 있는 자동차 부품. |
장점 | 높은 효율성, 정밀도, 비용 효율성으로 대량 생산에 적합합니다. | 플라스틱과 금속을 결합하여 조립을 줄이고 부품 성능을 향상시킵니다. |
도전 과제 | 단일 소재 부품으로 제한, 높은 툴링 비용. | 정확한 인서트 배치, 호환성 및 추가 비용. |
프로젝트에 적합한 몰딩 공정을 선택하는 데 도움이 필요하신가요? 지금 바로 전문가에게 문의하세요. !