소결 유리는 분말 유리를 재료의 녹는점에 도달하지 않은 상태에서 열과 압력을 가하여 밀도가 높은 고체 형태로 변형시키는 공정입니다.이 방법은 내구성이 강하고 튼튼한 유리 부품을 만들기 위해 제조 분야에서 널리 사용됩니다.이 공정은 일반적으로 파우더 컴팩트를 준비하고, 입자 융합을 위해 제어된 분위기에서 가열한 후 냉각하여 통일된 덩어리를 형성하는 과정을 거칩니다.주요 단계에는 결합제를 제거하고 1차 재료를 저다공성 구조로 융합하는 조성, 압축 및 열 적용이 포함됩니다.소결은 녹는점이 높은 재료에 특히 유용하며 세라믹 및 분말 야금과 같은 산업에서 필수적입니다.
핵심 포인트 설명:
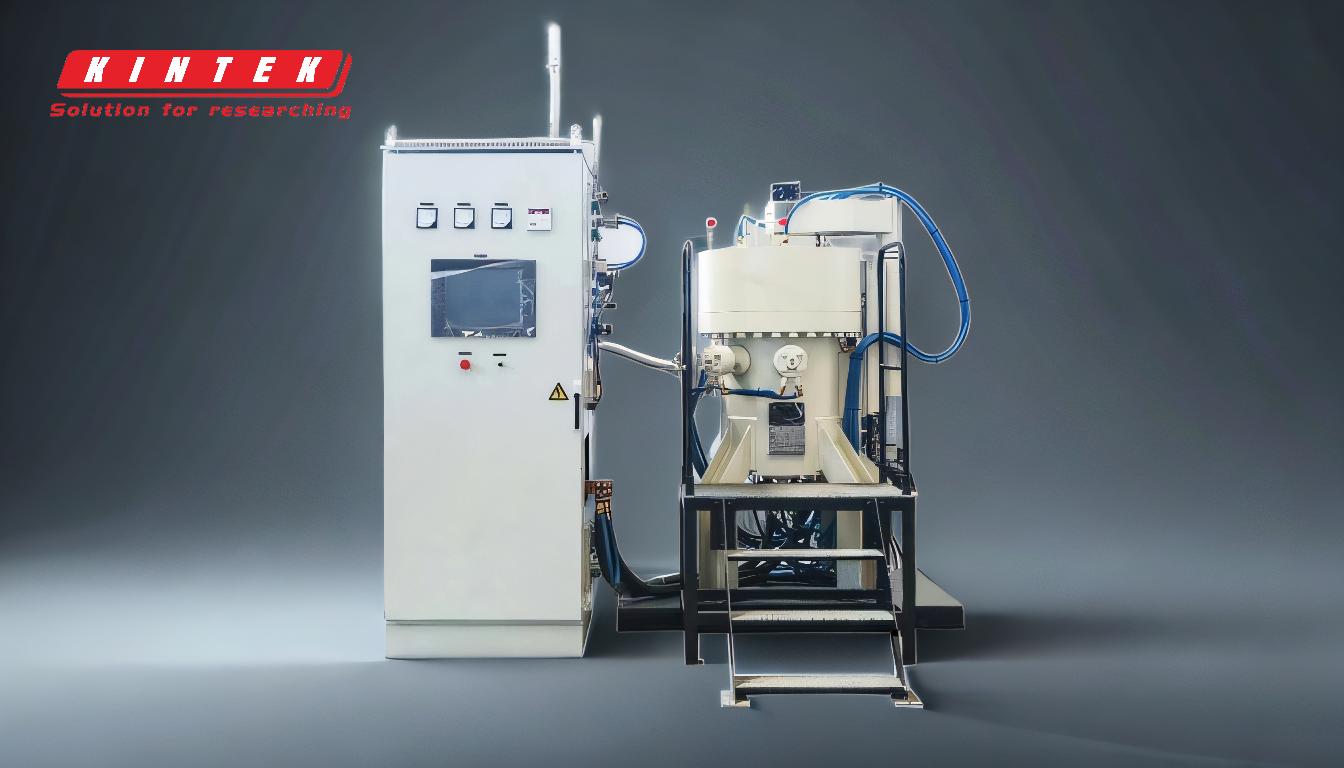
-
파우더 컴팩트 준비:
- 과정: 첫 번째 단계는 미세하게 분말화된 유리로 파우더 컴팩트를 준비하는 것입니다.이 작업은 냉간 용접, 3D 프린팅 레이저 또는 제어된 분위기에서 프레싱 도구와 같은 방법을 사용하여 수행할 수 있습니다.
- 세부 사항: 파우더는 균일성을 보장하기 위해 1차 재료 및 결합제와 혼합됩니다.그런 다음 혼합물을 금속 부품이 있는 경우 이를 지지하는 흑연 몰드를 사용하여 원하는 모양으로 압착합니다.
-
열과 압력 가하기:
- 공정: 고주파 유도 가열을 사용하여 제어된 분위기(일반적으로 질소-수소 혼합 환경)에서 고열과 고압을 가하여 분말 컴팩트를 성형합니다.
- 세부 사항: 액화를 방지하기 위해 온도를 유리의 녹는점 이하로 유지하도록 세심하게 제어합니다.이 단계에서는 결합제가 증발하거나 연소되어 1차 입자가 표면에서 융합을 시작할 수 있도록 합니다.
-
입자 융합 및 밀도화:
- 프로세스: 온도가 상승하면 1차 입자가 녹기 시작할 정도로 충분히 가열되어 개별 입자가 표면에서 융합됩니다.또는 청동과 같은 중간 결합제가 녹아서 입자 사이에 결합할 수도 있습니다.
- 세부 사항: 이 단계에서는 고온에서 재료 이동과 입자 경계 이동이 발생하여 세라믹 재료가 점진적으로 치밀화됩니다.시간이 지남에 따라 재료는 일정한 강도를 가진 도자기 몸체를 형성합니다.
-
냉각 및 응고:
- 프로세스: 입자가 충분히 융합된 후, 재료는 냉각되어 통일된 덩어리로 응고됩니다.
- 세부 사항: 균열이나 뒤틀림으로 이어질 수 있는 열 응력을 방지하기 위해 냉각 공정을 제어해야 합니다.최종 제품은 기계적 특성이 강화된 고밀도 저다공성 유리 부품입니다.
-
제어된 분위기:
- 프로세스: 소결 과정 내내 산화 및 기타 원치 않는 화학 반응을 방지하기 위해 제어된 분위기가 유지됩니다.
- 자세히 알아보기: 질소-수소 혼합 분위기를 사용하는 것은 원하는 재료 특성을 달성하고 최종 제품의 무결성을 보장하는 데 매우 중요합니다.
-
적용 분야 및 이점:
- 프로세스: 소결은 세라믹 및 분말 야금 등 다양한 산업에서 고강도와 내구성을 갖춘 부품을 생산하기 위해 사용됩니다.
- 자세히 알아보기: 이 공정은 텅스텐이나 몰리브덴과 같이 융점이 매우 높아 기존의 용융 및 주조 방법이 실용적이지 않은 재료에 특히 유용합니다.
소결 공정은 이러한 단계를 거쳐 분말 유리를 다양한 산업 분야에 적합한 고밀도, 내구성, 고성능 소재로 효과적으로 변환합니다.
요약 표:
단계 | 프로세스 | 세부 정보 |
---|---|---|
1.파우더 컴팩트 준비 | 파우더를 1차 재료 및 결합제와 혼합한 후 프레스하여 모양을 만듭니다. | 흑연 금형을 사용하여 균일성을 보장하고 금속 부품을 지지합니다. |
2.열과 압력의 적용 | 통제된 분위기에서 높은 열과 압력을 가합니다. | 액화를 방지하기 위해 온도가 녹는점 이하로 유지되고 결합제가 증발합니다. |
3.입자 융합 및 치밀화 | 입자는 표면에서 또는 청동과 같은 중간 결합제를 통해 융합됩니다. | 재료 이동과 입자 경계 이동은 치밀화 및 포세린 형성으로 이어집니다. |
4.냉각 및 응고 | 재료가 냉각되어 통일된 덩어리로 응고됩니다. | 제어된 냉각은 균열이나 뒤틀림을 방지하여 조밀하고 다공성이 낮은 구조를 만들어냅니다. |
5.제어된 대기 | 질소-수소 혼합 분위기가 유지됩니다. | 산화를 방지하고 원하는 재료 특성을 보장합니다. |
6.응용 분야 및 이점 | 고강도 부품을 위한 세라믹 및 분말 야금에 사용됩니다. | 텅스텐과 몰리브덴처럼 녹는점이 높은 재료에 이상적입니다. |
소결 유리로 제조 공정을 개선하는 방법을 알아보세요. 지금 바로 전문가에게 문의하세요 !