세라믹은 경도와 내마모성으로 잘 알려져 있지만, 압력을 가했을 때 세라믹의 거동은 더 복잡합니다.세라믹은 원자 구조로 인해 본질적으로 강하지만 깨지기 쉽기 때문에 스트레스를 받으면 큰 변형 없이 부서질 수 있습니다.그러나 고압과 같은 특정 조건에서 세라믹은 미세 구조의 치밀화로 인해 강도가 증가될 수 있습니다.이러한 치밀화는 다공성을 감소시키고 기계적 특성을 개선할 수 있습니다.압력과 세라믹 강도 사이의 관계는 재료 구성, 입자 크기, 결함 유무 등의 요인에 의해 영향을 받습니다.산업 기계나 항공우주 부품과 같이 세라믹에 높은 응력이 가해지는 분야에서는 이러한 요소를 이해하는 것이 중요합니다.
핵심 포인트 설명:
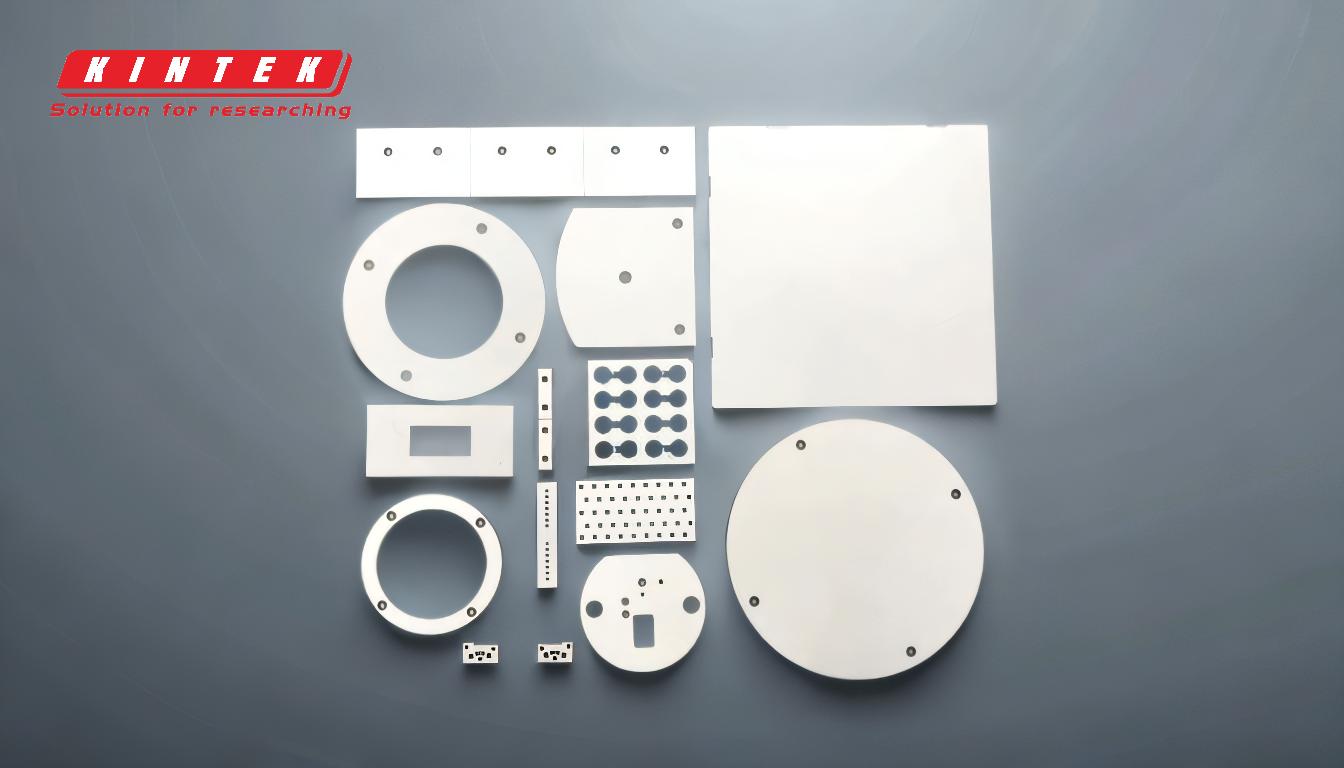
-
세라믹의 고유한 힘:
- 세라믹은 강력한 이온 결합과 공유 결합으로 구성되어 있어 경도가 높고 변형에 대한 저항력이 높습니다.
- 세라믹의 원자 구조는 본질적으로 강하지만 부서지기 쉽기 때문에 파손되기 전에 소성 변형이 일어나지 않습니다.
-
세라믹에 가해지는 압력의 영향:
- 고압에서 세라믹은 재료의 미세 구조가 더 조밀해지는 치밀화를 겪을 수 있습니다.
- 이러한 치밀화는 다공성을 감소시키고 재료가 더 균일해지고 균열 전파가 덜 발생하기 때문에 강도를 증가시킬 수 있습니다.
-
압력 하에서 강도에 영향을 미치는 요인:
- 재료 구성:세라믹의 종류(예: 알루미나, 탄화규소)는 압력에 반응하는 방식에 중요한 역할을 합니다.일부 세라믹은 다른 세라믹보다 치밀화되기 쉽습니다.
- 입자 크기:입자 크기가 작을수록 균열 전파를 방해할 수 있는 입자 경계가 많아지기 때문에 일반적으로 압력 하에서 세라믹이 더 강해집니다.
- 결함 및 다공성:결함이나 다공성이 있으면 세라믹이 약해질 수 있지만, 압력을 받으면 이러한 결함이 압축되어 강도가 높아질 수 있습니다.
-
고압 세라믹의 응용 분야:
- 압력 하에서 강도가 증가하는 세라믹은 절삭 공구, 갑옷 및 항공 우주 부품과 같이 스트레스가 높은 환경에서 사용됩니다.
- 압력-강도 관계를 이해하는 것은 극한의 조건에서도 고장 없이 견딜 수 있는 세라믹을 설계하는 데 매우 중요합니다.
-
한계와 도전 과제:
- 세라믹은 압력을 받으면 더 강해질 수 있지만, 취성은 여전히 도전 과제입니다.가해지는 응력이 파단 인성을 초과하면 세라믹은 여전히 갑작스러운 파손을 일으키기 쉽습니다.
- 압력 하에서의 치밀화 과정은 항상 예측 가능한 것은 아니며 균일한 강도 증가를 달성하는 것은 어려울 수 있습니다.
요약하면, 세라믹은 치밀화 및 다공성 감소로 인해 압력을 받으면 실제로 더 강해질 수 있지만 이러한 효과는 재료 구성, 입자 크기 및 결함의 존재 여부에 영향을 받습니다.이러한 강도의 증가는 특정 용도에 유용하지만, 세라믹의 고유한 취성은 스트레스가 많은 환경에서 주의 깊게 관리해야 하는 한계로 남아 있습니다.
요약 표:
핵심 요소 | 압력 하에서 세라믹 강도에 미치는 영향 |
---|---|
재료 구성 | 다양한 세라믹(예: 알루미나, 탄화규소)은 압력에 고유하게 반응하여 치밀화에 영향을 미칩니다. |
입자 크기 | 입자 크기가 작을수록 더 많은 입자 경계를 제공하여 균열 전파를 방해함으로써 강도가 향상됩니다. |
결함 및 다공성 | 결함은 세라믹을 약화시키지만 압력을 받으면 압축되어 다공성이 감소하고 강도가 높아질 수 있습니다. |
응용 분야 | 고압 세라믹은 절삭 공구, 갑옷, 항공우주 부품에 사용되어 강도를 높입니다. |
세라믹이 압력 하에서 어떻게 작동하는지 자세히 알고 싶으신가요? 지금 바로 전문가에게 문의하세요. 맞춤형 인사이트를 확인하세요!