분말 야금에서 다공성은 최종 제품의 기계적 특성과 성능에 영향을 미치는 중요한 요소입니다.제조 공정 중 몇 가지 주요 파라미터를 최적화하여 다공성을 줄일 수 있습니다.여기에는 압축 압력, 소결 온도 및 소결 시간 증가가 포함되며, 이는 총체적으로 겉보기 다공성을 감소시키고 부피 밀도를 높이는 데 도움이 됩니다.또한 입자가 클수록 다공성이 증가하는 경향이 있으므로 입자 크기를 조절하는 것도 중요합니다.제조업체는 이러한 요소를 신중하게 관리함으로써 기계적 특성이 향상된 고밀도, 저다공성 부품을 생산할 수 있습니다.
핵심 포인트 설명:
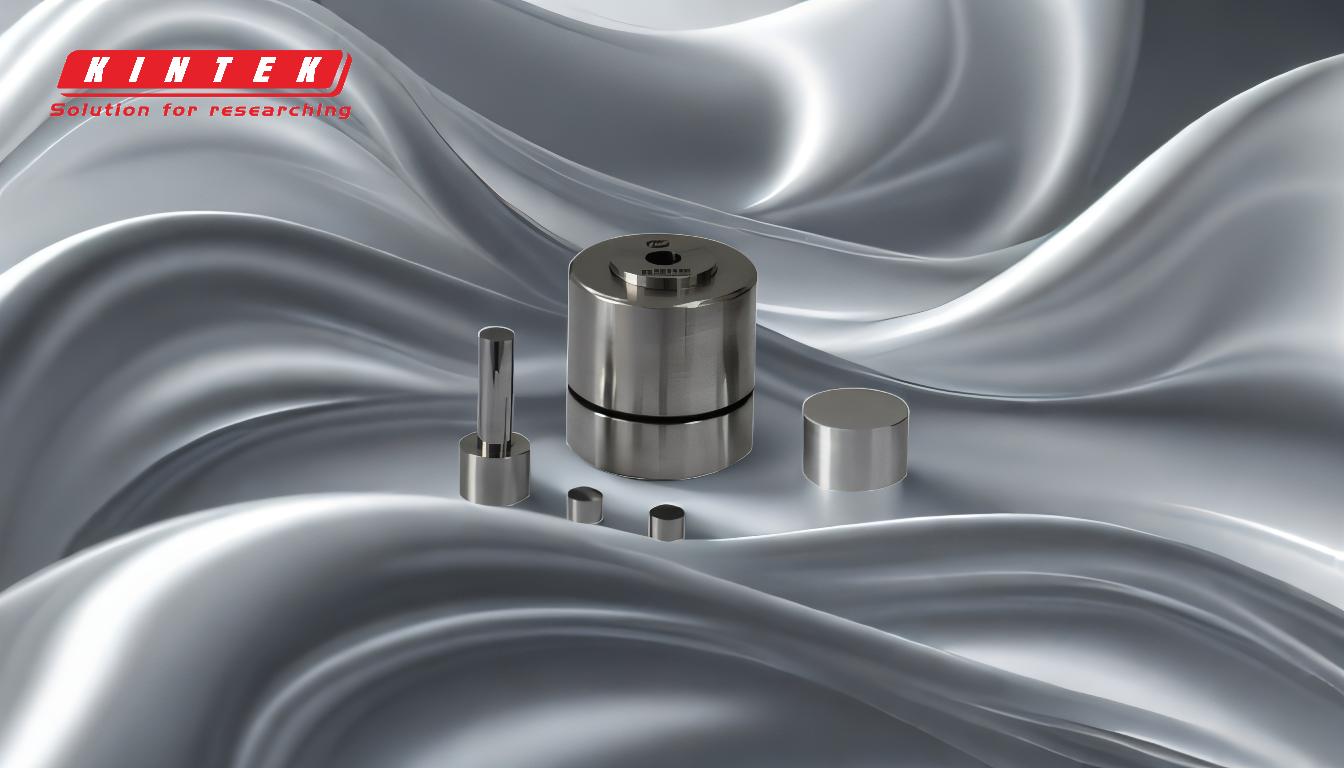
-
압축 압력 증가:
- Impact:압축 압력이 높을수록 분말 입자 사이의 간격이 줄어들어 다공성이 낮고 밀도가 높은 컴팩트가 만들어집니다.
- 메커니즘:다짐 단계에서 압력이 가해지면 입자가 서로 밀착되어 공극이 최소화되고 그린 컴팩트의 부피 밀도가 증가합니다.
- 실용적인 고려 사항:높은 압력은 유리하지만 다이가 손상되거나 부품의 밀도 분포가 불균일해질 수 있는 위험과 균형을 맞춰야 합니다.
-
소결 온도 및 시간 최적화:
- Impact:더 높은 소결 온도와 더 긴 소결 시간은 입자 결합과 확산을 촉진하여 다공성을 줄이고 밀도를 향상시킵니다.
- 메커니즘:소결은 압축된 분말을 녹는점 이하로 가열하여 원자가 입자 경계를 가로질러 확산되도록 하여 기공을 닫고 재료를 강화하는 과정을 포함합니다.
- 실용적인 고려 사항:과도한 온도나 시간은 입자 성장이나 왜곡을 유발할 수 있으므로 세심한 최적화가 필요합니다.
-
입자 크기 제어:
- Impact:입자 크기가 작을수록 일반적으로 더 효율적으로 포장되어 빈 공간을 적게 남기기 때문에 다공성이 낮아집니다.
- 메커니즘:미세 입자는 표면적 대 부피 비율이 높아 소결 및 결합을 향상시킵니다.반면 입자가 클수록 더 많은 틈이 생기고 다공성이 증가합니다.
- 실용적인 고려 사항:입자가 작을수록 좋지만 응집의 위험이 높아질 수 있으므로 가공 중에 관리해야 합니다.
-
분말 생산 방법:
- Impact:금속 분말을 생산하는 데 사용되는 방법은 크기, 모양 및 분포에 영향을 미치며, 이는 다시 다공성에 영향을 미칩니다.
- 메커니즘:분무와 같은 기술은 다공성을 최소화하도록 크기 범위를 조절할 수 있는 분말을 생산합니다.분쇄 및 분쇄는 불규칙한 모양의 입자를 생성하여 포장 효율이 떨어질 수 있습니다.
- 실용적인 고려 사항:원하는 입자 특성을 달성하고 다공성을 최소화하려면 적절한 분말 생산 방법을 선택하는 것이 필수적입니다.
-
재료 선택:
- Impact:기본 재료(예: 구리 베이스 또는 철 베이스)의 선택은 입자 모양, 크기 및 소결 거동의 차이로 인해 다공성에 영향을 미칠 수 있습니다.
- 메커니즘:일부 재료는 다른 재료보다 더 쉽게 소결되어 밀도가 향상되고 다공성이 낮아집니다.
- 실용적인 고려 사항:재료 선택은 사용 목적과 원하는 기계적 특성에 따라 이루어져야 합니다.
이러한 핵심 요소를 해결함으로써 제조업체는 분말 야금에서 다공성을 효과적으로 줄여 강도, 내구성 및 성능이 향상된 부품을 만들 수 있습니다.
요약 표:
핵심 요소 | 영향 | 메커니즘 | 실용적인 고려 사항 |
---|---|---|---|
압축 압력 증가 | 입자 사이의 간격을 줄여 다공성이 낮고 밀도가 높은 컴팩트를 만듭니다. | 압력이 입자를 더 밀착시켜 공극을 최소화하고 부피 밀도를 높입니다. | 다이 손상이나 고르지 않은 밀도 분포를 방지하기 위해 압력의 균형을 유지합니다. |
소결 온도 및 시간 최적화 | 입자 결합을 촉진하고 다공성을 줄이며 밀도를 높입니다. | 녹는점 이하로 가열하면 원자가 확산되어 기공이 닫히고 재료가 강화됩니다. | 입자의 성장이나 왜곡을 방지하기 위해 과도한 온도나 시간을 피하세요. |
입자 크기 제어 | 입자가 작을수록 효율적으로 포장되어 다공성이 감소합니다. | 미세 입자는 부피 대비 표면적 비율이 높아 소결 및 결합력이 향상됩니다. | 입자가 작아 응집 위험을 관리할 수 있습니다. |
분말 생산 방법 | 입자 크기, 모양, 분포에 영향을 미치며 다공성에 영향을 미칩니다. | 분무는 제어된 크기 범위를 생성하지만 분쇄/분쇄는 불규칙한 입자를 생성할 수 있습니다. | 원하는 입자 특성을 얻기 위해 적합한 방법을 선택하세요. |
재료 선택 | 기본 재료는 소결 거동의 차이로 인해 다공성에 영향을 미칩니다. | 일부 재료는 더 쉽게 소결되어 치밀도가 향상되고 다공성이 낮아집니다. | 응용 분야와 원하는 기계적 특성에 따라 재료를 선택하세요. |
분말 야금 공정을 최적화할 준비가 되셨나요? 지금 바로 전문가에게 문의하세요. 맞춤형 솔루션에 대해 문의하세요!