특히 진공 증착 공정에 사용되는 코팅 챔버는 다양한 표면에 얇고 내구성 있는 보호층을 적용하도록 설계된 정교한 시스템입니다.이 챔버는 진공 상태에서 작동하여 고체 금속 재료를 기화시키고, 기화된 원자가 제품 표면에 침투하여 결합하여 보호 코팅을 형성합니다.이 공정에는 코팅 공정의 전반적인 기능과 효율성에 기여하는 여러 가지 주요 구성 요소가 포함됩니다.이러한 구성 요소가 어떻게 함께 작동하는지 이해하면 진공 코팅 기술의 복잡하면서도 정밀한 특성에 대한 통찰력을 얻을 수 있습니다.
핵심 포인트 설명:
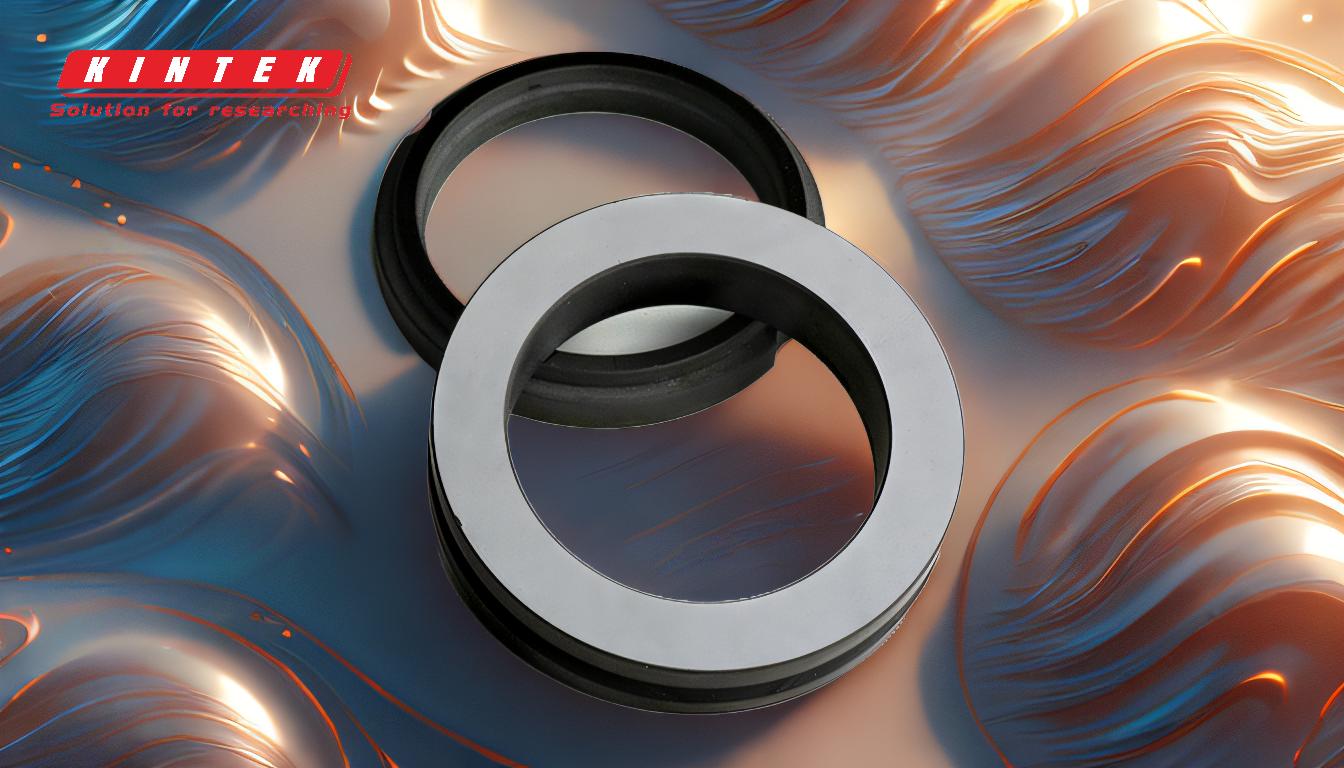
-
진공 챔버 및 코팅 장비:
- 진공 챔버는 코팅 공정이 이루어지는 핵심 부품입니다.진공 챔버는 재료의 기화 및 증착에 필수적인 고진공 환경을 유지하도록 설계되었습니다.
- 챔버는 일반적으로 고온과 고압을 견딜 수 있는 재료로 만들어져 코팅 공정에 안정적인 환경을 보장합니다.
- 챔버 내부에 코팅할 제품을 넣고 기화된 재료가 그쪽으로 향하도록 하여 보호층을 형성합니다.
-
진공 획득 부품:
- 이 구성 요소는 챔버 내부의 진공을 생성하고 유지하는 역할을 합니다.여기에는 챔버에서 공기 및 기타 가스를 제거하는 펌프와 밸브가 포함됩니다.
- 진공은 오염을 방지하고 기화된 물질이 제품 표면으로 방해받지 않고 이동할 수 있도록 하기 때문에 매우 중요합니다.
-
진공 측정 부품:
- 진공 레벨의 정확한 측정은 코팅 공정을 제어하는 데 필수적입니다.이 부분에는 챔버 내부의 압력을 모니터링하는 게이지와 센서가 포함됩니다.
- 정확한 진공 수준을 유지하면 코팅의 품질과 일관성을 보장할 수 있습니다.
-
전원 공급 부품:
- 전원 공급 장치는 고체 금속 재료를 기화시키는 데 필요한 에너지를 제공합니다.여기에는 스퍼터링 또는 증착 소스를 위한 고전압 전원 공급 장치가 포함될 수 있습니다.
- 전원 공급 장치는 코팅 재료의 정확한 증착을 보장하기 위해 안정적이고 제어가 가능해야 합니다.
-
공정 가스 입력 시스템:
- 일부 코팅 공정에서는 증착 공정을 개선하거나 코팅의 특성을 변경하기 위해 특정 가스를 챔버에 도입합니다.
- 가스 입력 시스템은 이러한 가스의 흐름과 구성을 제어하여 코팅의 접착력, 밀도 및 기타 특성에 영향을 줄 수 있습니다.
-
기계식 전송 부품:
- 이 부품에는 챔버 내에서 제품을 이동하고 배치하는 메커니즘이 포함되어 있습니다.제품이 균일하게 코팅되고 기화된 재료가 균일하게 분포되도록 합니다.
- 일관된 코팅 두께와 품질을 달성하려면 정밀한 움직임이 중요합니다.
-
가열 및 온도 측정 장비:
- 코팅 공정에서 온도 제어는 매우 중요합니다.발열체와 온도 센서는 챔버와 제품이 증착을 위한 최적의 온도를 유지하도록 보장합니다.
- 적절한 온도 관리는 기화 속도와 코팅의 품질에 영향을 미칩니다.
-
이온 증발 및 스퍼터링 소스:
- 이 소스는 고체 물질을 증발시키는 데 사용됩니다.이온 증발은 물질이 기화될 때까지 가열하는 반면, 스퍼터링은 고에너지 이온을 사용하여 대상 물질에서 원자를 떨어뜨립니다.
- 소스 선택은 사용되는 재료와 코팅의 원하는 특성에 따라 달라집니다.
-
수냉식 냉각 시스템:
- 코팅 공정에서는 상당한 열이 발생하므로 장비의 손상을 방지하고 일관된 공정 조건을 보장하기 위해 관리해야 합니다.
- 수냉 시스템은 챔버와 기타 구성 요소를 통해 물을 순환시켜 열을 발산하고 안정적인 작동 온도를 유지합니다.
요약하면, 코팅 챔버는 정밀하고 고품질의 코팅을 위해 다양한 구성 요소를 통합하는 복잡한 시스템입니다.각 구성 요소는 진공 환경을 조성하고 코팅 재료를 기화하며 제품 표면에 균일한 증착을 보장하는 데 특정한 역할을 합니다.이러한 구성 요소와 그 기능을 이해하는 것은 코팅 공정을 최적화하고 원하는 코팅의 보호 및 기능적 특성을 달성하는 데 필수적입니다.
요약 표:
구성 요소 | 기능 |
---|---|
진공 챔버 및 코팅 장비 | 재료 기화 및 증착을 위한 고진공 환경을 유지합니다. |
진공 획득 부품 | 오염을 방지하기 위해 진공 상태를 생성하고 유지합니다. |
진공 측정 부품 | 일관된 코팅 품질을 위해 진공 수준을 모니터링하고 제어합니다. |
전원 공급 부품 | 고체 물질을 기화시키는 데 필요한 에너지를 제공합니다. |
공정 가스 입력 시스템 | 증착을 향상시키거나 코팅 특성을 변경하기 위해 가스를 도입합니다. |
기계식 전송 부품 | 제품을 정밀하게 배치하여 균일한 코팅을 보장합니다. |
가열 및 온도 측정 | 기화 및 코팅 품질을 위한 최적의 온도를 유지합니다. |
이온 증발 및 스퍼터링 소스 | 열 또는 고에너지 이온을 사용하여 증착할 재료를 증발시킵니다. |
수냉식 냉각 시스템 | 열을 발산하여 안정적인 작동 조건을 유지합니다. |
첨단 진공 증착 시스템으로 코팅 공정을 최적화하세요. 지금 바로 전문가에게 문의하세요 !